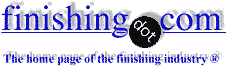
-----
Bearing Bore Re-Sizing - Hard Chrome/Nickel/Something Else?
2005
We are an FAA Shop repairing/reconditioning actuators. We have a precision bore .2500-.2505 that is running up to .251 in an aluminum casting on returns. The casting is anodized, and the bore is unfinished telling me a good process for reconditioning would be a nickel sulfamate plate followed by a finish hone to size. (Sometimes holes are elongated too). The surface is not a dynamic bearing surface (no motion across it) but rather clamps
a martensic steel pin.
Any opinions here if I am barking up the wrong tree?
- Setauket, New York
First of two simultaneous responses --
You can bring the bore size into tolerance by simply anodizing it. That will be the least expensive and most relieble method.
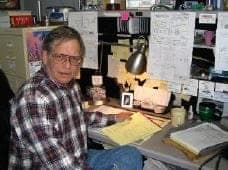
Jeffrey Holmes, CEF
Spartanburg, South Carolina
2005
Second of two simultaneous responses --
Is brush plating permitted by the applicable specification? If so, I think it would be more economical to restore one or a few holes without having to mask the part all over to immerse it in a bath. There are good alternatives to plate onto aluminum including but not limited to brush sulfamate nikel.
Guillermo MarrufoMonterrey, NL, Mexico
2005
It does not matter what we think. You have to use the method of repair by the OEM or go thru a process (painfull) to have your process approved. Extremely few repair facilities have this type of staff or certifications. You can lose your FAA license in a heartbeat for unapproved repairs. The in an inflight failure, liability is unreal, even tho your process may be perfect.
James Watts- Navarre, Florida
2005
Absolutely correct on approvals James - but I want to know which method to propose.
Clint Brown- New York
2005
It is hard to say what would be a recommended procedure. How big is the part? How many holes per part? What is the depth of the hole?
Anodize with a temperature less than type II might work, possibly approaching hard anodize. And then hone to size. But this will involve masking, a huge drawback for some parts, especially large parts.
You could probably brush the holes to near size and then hone. Hone would call for hard nickel rather than sulfamate. If you want to machine after brush plate, you probably would have to bore the holes oversize to allow for 0.003" per side for plate, plus machine stock using sulfamate nickel. Minimal masking required, but it is extremely operator sensitive as far as quality of the plate. Would require good equipment, excellent layout and well trained operators.
You might talk to several brush plate companies about selective
(brush ) anodizing which can be done to very close to size with a minor hone touch up.
- Navarre, Florida
2005
Q, A, or Comment on THIS thread -or- Start a NEW Thread