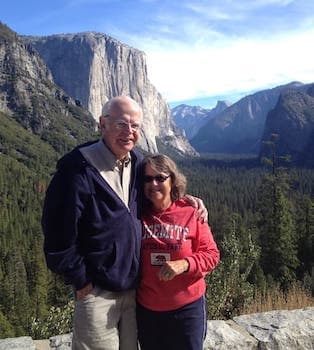
Curated with aloha by
Ted Mooney, P.E. RET
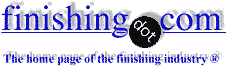
The authoritative public forum
for Metal Finishing 1989-2025
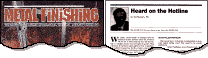
-----
Sandblasting aluminum parts prior to Alodine coating
Quickstart (no readers left behind):
Aluminum is often 'chromate conversion coated' as a corrosion resistant final finish or as a pretreatment for painting or powder coating. The process actually involves many steps, usually including alkaline cleaning, etching, deox/desmut, the chromate conversion step per se, and water rinses between each step.
MIL-C-5541 / MIL-DTL-5541 / MIL PRF-5541 is the most commonly cited spec. "Alodine" and "Iridite" are proprietary trade names from two suppliers of the process chemistry. "Chem film" is a slang term for the process often used in the USA.
Q. Machining an aluminum flat part which has a large number of holes results in burrs inside; so would sandblasting be a good way to remove burrs?
Parts need to be alodine coated.
- Ontario [?]
July 23, 2024
Tip: This forum was established to build camaraderie among enthusiasts through sharing tips, opinions, pics & personality.
The curator & some readers who publicly share their info will be less likely to engage with those who don't.
⇩ Related postings, oldest first ⇩
Q. I am a Planner for an industrial rebuild facility . I have some aluminum tubes that go on an air cycle unit. We have tried to bead blast these parts before Alodine but sand was left in them and caused clogs when the air cycle unit was built. Is there any type of sandblast procedure that can be used that won't leave a residue? Or is there a cleaning procedure that can be done to remove residue?
Tina LeemasterTank Rebuild Facility - Anniston, Alabama
2005
I would hope, for your sake, that the treatment house that applies the coating would at least have the ability to pre-clean prior to Alodine.
In its simplest form the parts should be preliminary cleaned using an alkaline soak cleaner, well rinsed in water, etched, rinsed well in water before the Alodine. This should remove any blast material from any simple form sheet or tube.
If shapes are complex, with blind holes or narrow bores there is always a chance of entrapment. In these cases I would avoid blasting of at all possible and rely on a really good etch.
Aerospace - Yeovil, Somerset, UK
How big are your parts? I suggest you use a mass finishing system if possible. If not, bottom line here is that all material are porous and blasting systems are good at getting into porous surfaces, but not good at getting out of them because of their irregular sizes and shapes due to break down. Best way to remove is to run parts through an ultrasonic system or high pressure or heated water system, in that order.
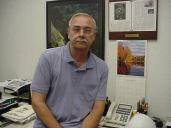
AF Kenton
retired business owner - Hatboro, Pennsylvania
Any kind of blasting or tumbling will imbed all sorts of organic and inorganic junk into the Kleenex-like soft spongy aluminum metal. Iron bearing media is the worst. Aluminum Oxide blasting is the least bad. Then as someone said above - etch as deep as you can stand to remove imbedded soil.
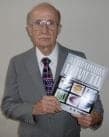
Robert H Probert
Robert H Probert Technical Services

Garner, North Carolina
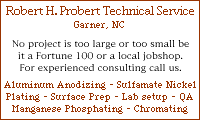
Q, A, or Comment on THIS thread -or- Start a NEW Thread
