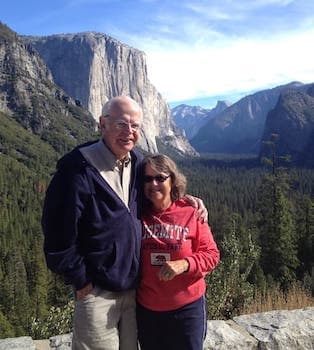
Curated with aloha by
Ted Mooney, P.E. RET
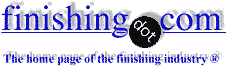
The authoritative public forum
for Metal Finishing 1989-2025
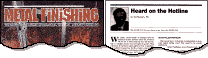
-----
Plating nickel on nickel
See also topic 17382, "Activating/reactivating old Nickel plating"
2002Q. I am working with a sulfamate bath
600 g/l of sulfamate
40 g/l of boric acid
10 g/l of NiCl2
T=44°C +-0.5
maximum current density 1.5 amps square decimeter
Thickness = 1 mm
I need to plate nickel over nickel. I have no possibilities (at the moment) to make a sulfamate strike or a Woods strike. I have some information about nickel activation with 20% sulfuric acid with this sequence:
5 minutes of reverse current at 10 amps/dm2
2 minutes of reverse current at 20 amps/dm2
2 minutes of direct current at 10 amps/dm2
... then rinse with deionized water and plate nickel at 0.6-0.8 amps/dm2.
In all the tests I made in laboratory the adherence was perfect but I have doubts in passing from the laboratory to the plant. Any suggestion in this respect it will be very appreciated.
- Spain
A. I would agree that it may be a problem taking this method to production. If you could keep the sulfuric acid clean by dummying, you may have a better chance. As soon as any copper or other metal builds up in the sulfuric acid, you will start plating a non-adherent smut which will be a problem.


Tom Pullizzi
Falls Township, Pennsylvania
2002
A. I don't like to use the words direct and reverse, however, what you are doing makes good adhesion, Make the part CATHODIC in the clean electronic grade sulfuric acid using bagged carbon anodes. Be aware that any sulfuric soluble impurities (iron, copper, zinc,) either coming in with the sulfuric acid or dragged in by you, will co-deposit but not adhere over old nickel oxide, and then your deposit will blister off. Also the addition of about 1/2 oz/gal very clean and pure ammonium bifluoride will enhance the adhesion. Any metallic impurities will compromise this process, and it will also compromise a Sulfamate strike or a Woods Strike. Theoretically the only difference in the results from electrolytic plain acid versus a metallic strike is that NOW you must transfer to the plating tank more rapidly.
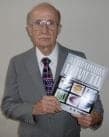
Robert H Probert
Robert H Probert Technical Services

Garner, North Carolina
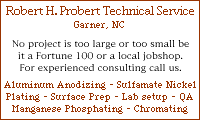
2002
A. I am aware of the fact that cyanide sounds like a four letter word but in case that you have cyanide in your premises, a cathodic activation in an alkaline cyanide solution is the best way to activate nickel and to enable plating nickel on nickel. If you stick to the sulfuric acid activation, use the previous reply and add fluorides. I recommend to activate in the sulfuric acid only when parts are activated cathodically.(what you call direct).


Sara Michaeli
Tel-Aviv-Yafo, Israel
2002
A. Hi, we run a Pulse Reverse Nickel chloride process. We are able to run reverse for e.g. 5 min. and then start up the electroforming process, without the item leaving the bath. This could solve all your problems.
Lars B. Andersen- Denmark
2002
Thank you very much Tom, Robert, Sara and Lars for your comments. The part is already plated and everything has gone OK. It was 1 piece, 8 tons, but only 1 piece. The sulfuric was as clean as possible and the dead time was as short as we could.
Thanks again,
- Spain
2002
Multiple threads merged: please forgive chronology errors and repetition 🙂
Q. One of our lines is a barrel bright nickel.
I have plated Bright nickel on some 200 kg of brass washers.
Due to the fact of them sticking to the sides of the barrel they have funny brown marks on them. I have solved the sticking problem but do not want to strip the 200 kg and replate but I am trying to reactivate the nickel so that I can plate nickel on top of the existing nickel. I know that it is not advised to do so but has anyone got the magical answer for me.
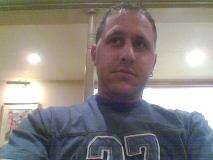
Gary Joseph
Johannesburg,
South Africa
2005
A. I don't think the approach you want to use is extraordinary, Gary. Bumper platers have, for years, replated internal rejects without stripping the nickel; it's the environmentally savvy thing to do if it works. With luck, it involves no more than running the parts through the preplate cycle, then through a nickel strike tank, then plating. Obviously, the parts must be properly reactivated or peeling will be a problem.
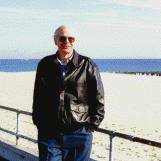
Ted Mooney, P.E.
Striving to live Aloha
finishing.com - Pine Beach, New Jersey
2005
A. You will need to go through a good cleaning cycle and use a nickel strike, such as Wood's nickel. If the nickel contains lots of organics, you may need to machine it to give a rough surface.
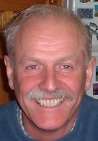
Trevor Crichton
R&D practical scientist
Chesham, Bucks, UK
2005
A. Gary
You might consider using a cathodic cyanide nickel activator if this is amenable with your overall process. Most any supplier would have their version of this chemistry.
- Warwick, Rhode Island, USA
2005
A. Gary,
I have used acid salts containing fluorides, hot @ one pound per gallon, soak time depends on how passive your bright Nickel is, but at least 5 minutes. Consult supplier for the proper tank and heater materials used.
- Mays Landing, New Jersey, USA
2005
![]() |
2005 A. Hi! - Kranj, Slovenija (EU) A. Regarding Ted's recommendation to go again through the preplate cycle, I would like to mention that if the preplate cycle includes an anodic cleaner you should not enter this bath. ![]() ![]() Sara Michaeli Tel-Aviv-Yafo, Israel 2005 |
A. Hi,
In my opinion re-activating nickel is very touch and go. We always use a copper strike plate over the existing nickel and then re-nickel and we have never had a problem.
Cheers,
- UK
2005
2005
A. This is how I do it:
Hot alkaline cathodic cleaner
15% sulfuric dip - 1 min
Cyanide cathodic cleaner - 1 min
15% sulfuric dip - 1 min
Woods Nickel strike - 20 secs
Works every time.
- East Sussex, England
A. You might want to check out my response to question #36845 in section 2B I have used this method quite a bit, we can plate stainless without a Wood's nickel strike. We use a Macdermid product by the name of Metex LDA,ammonium bi-fluoride & HCl -- maybe worth a shot. We activate for 2 minutes in this acid and, of course, we soak clean it and then go I the electrocleaner -- but we do make contact.
Brian C. Gaylets- Scranton,Pennsylvania, U.S.A.
2005
Multiple threads merged: please forgive chronology errors and repetition 🙂
Q. In electroforming there are a few different approaches to re-activation of a nickel deposit when re-entering a part into plating solution.
We electroform in a nickel sulfamate bath containing @ 12 oz/gal Ni metal. This is a non-chloride bath using S-rounds. I am considering reverse polarity activation in the plating bath as opposed to chemical de-oxidizing.
What suggestions/success stories do others have to offer and on what type of parts and nickel plating baths?
Thanks
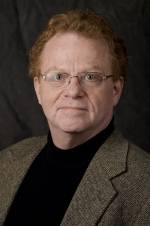
Bob Adams CEF
Tijuana, Mexico
June 26, 2008
A. Hi, Bob. The typical nickel activation process is "Wood's Nickel", which is nickel chloride based (32 oz/gal Nickel Chloride, 12 oz/gal Hydrochloric acid). There is also a nickel sulphamate strike (which may be more compatible with your nickel sulphamate plating); the ratio of nickel to acid is probably similar, but I don't know the exact numbers without researching it.
If you use the search engine to look for "Wood's Nickel" and
"nickel sulphamate strike", though, you find some variations on both of these formulations. Good luck.
Regards,
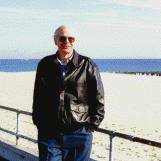
Ted Mooney, P.E.
Striving to live Aloha
finishing.com - Pine Beach, New Jersey
July 5, 2008
You may endup by passivating your part
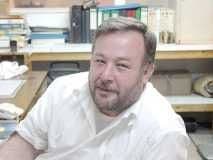
Khair Shishani
aircraft maintenance - Al Ain, UAE
July 6, 2008
Bob, Unfortunately you give very little detail of your process - perhaps it is sensitive information or just an oversight. Either way, not knowing your process makes giving an answer a bit like shooting a bow and arrow in a totally dark room and hoping to hit the target.
Anyway, Ted is correct about using a nickel strike. You need to reactivate the nickel surface prior to further metal deposition otherwise subsequent layers will delaminate. You also need to activate the nickel before you use a nickel strike, so a quick anodic treatment in a good acid activator normally does the trick. The level of activation will be dependent on your nickel electroforming bath and what additives you are using. I used to also give a few seconds anodic treatment in the nickel strike before reversing the polarity to the more conventional cathodic polarisation. This ensures the surface is active and suitable for receiving fresh nickel and making it adhere. There are numerous nickel strikes around, but the most common ones are Woods nickel and sulphamate nickel; formulations for both are available in any good text book, the internet or your chemical supply house.
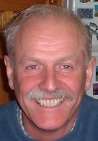
Trevor Crichton
R&D practical scientist
Chesham, Bucks, UK
July 7, 2008
Q. Trevor,
What are good anodic treatments before the Ni strike? I am working with a similar situation - however, I am trying to plate Ni on a films that has Ni and Cu exposed. Need to have good adhesion at the Ni-Ni interface.
Thanks,
mems - Boulder, Colorado, USA
July 21, 2008
A. Chiu,
If you are using a Woods nickel strike a brief reverse in the bath (seconds not minutes) will leave the surface slightly etched with a micro roughness ideal for maximum adhesion. A good indication that the anodic cycle was correct is to observe the surface. There should be a uniform color without burns, streaks, patches or excessive roughness and totally hydrophylic for a perfect water break test. You should start the cathodic step (forward) immediately after this. Then move to the following steps w/o delay.
Monterrey, NL, Mexico
July 21, 2008
A. As you have discovered, nickel can be very difficult to reactivate so that you get good adhesion. If the nickel deposit contains any additives, it becomes even harder to reactivate. However, often nickel can be reactivated by using the correct procedure. Reactivation of nickel should not be considered to be a full scale production process, but only one for remedial operations, as it is fiddly, time consuming and the process can run the risk of cross contamination from different solutions, as clean water rinsing should be minimised.
Firstly, ensure the nickel is totally free of any surface contamination; this is done by giving it a thorough chemical and electrochemical clean using both alkali and acid cleaners. If possible give the nickel a good scrub with a chalk slurry and then rinse it off before going into the aqueous clean stages. Your aqueous cleaning can be commercial products from your supply house, but it is important that the acid cleaner is a strong one (typically equivalent to at least 10% sulfuric acid. One good one I used was a mix of 25% HCl and 13% formic acid (HCOOH) at about 30C for at least 60 seconds. At no stage should your nickel surface be allowed to dry out or passivate, so rinses should be in slightly acid washes, sing the same acid as the process sequence. Once clean, the nickel can be reactivated in a good nickel strike. The most common one is Woods nickel (240g/l NiCl2, 125g/l HCl at 2-4A/dm2 and room temp.) Use the Woods nickel in both cathodic and anodic phases, say 10 seconds anodic, followed by 60 seconds cathodic. Do this for about five or so minutes. An alternative, that may be quite good, but I never compared them, was to use 20g/l NiCl2 with 30% H2SO4 at 8 Volts cathodic for 20-30 seconds; there may be some benefit is also using reverse polarity here too. Either way, ensure that your final cycle is cathodic! Once you have reactivated the nickel, transfer it to your main nickel bath. Depending on your plating bath (sulphate based, chloride based, fluoborate based or sulphamate based), you may want to consider using a compatible acid rinse between the strike and the main bath.
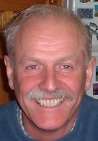
Trevor Crichton
R&D practical scientist
Chesham, Bucks, UK
July 26, 2008
July 28, 2008
A. I suggested to Bob Adams that he reactivate his parts in the sulfamate nickel bath. I have some clients who do this and all report good results.
Using the plating bath to activate the parts has many advantages:
1. it is impossible for the parts to dry between activation
and plating
2. rinsing is not required
This works for parts that have not been machined, formed, heat treated or had other secondary operations performed after the first plating. Basically you are reactivating a clean plated nickel surface that has been exposed to air for about 4 hours or less.
You should try it before going to more extensive reactivation.
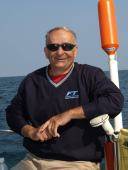
Pat Mentone
St Paul, Minnesota
July 30, 2008
A. Pat, I agree with you about the benefits of reactivating in the plating bath and under the right conditions, I would agree with you.
My last response was more directed towards Chui Tao rather than Bob Adams; Chui's question was much vaguer than Bob's and with less detail, so I gave a broader answer.
As far as Bob is concerned, from my experiences of nickel electroforming, the only reasons for reactivating the nickel are after the workpiece has lost polarisation or there has been a need to carry out a processing step off-line. If polarisation has been lost by a loss of power and it is simply a power cut, as long as the workpiece has not been removed from the bath, then in-situ reactivation is possible, but only as long as it doesn't affect the mandrel and contaminate the bath.
The only real problem with reactivating in a sulphamate bath is that anodic polarisation will require a higher chloride level in the bath, since the deposited nickel will not be S-depolarised and will hence need chloride to ensure good polarisation and no passivation. If there is inadequate chloride in the bath, the workpiece runs the risk of passivation with nickel oxide and this will certainly cause delamination.
However, one of the best things about sulphamate baths is that they produce low stress deposits, but chloride induces stress, so you want to keep it as low as possible.
Electroforming with nickel sulphamate allows you to use a zero chloride bath, but most electroformers, us being a cautious breed, tend to add a bit of chloride, just for luck!
If the workpiece has been removed from the bath for off-line processing, it will certainly require extensive re-processing to ensure total and complete reactivation and the elimination of delamination
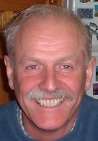
Trevor Crichton
R&D practical scientist
Chesham, Bucks, UK
A. Trevor
I always enjoy reading your comments and find them very helpful.
Frequently the reason for reactivating is because the part has to be taken out of solution for a thickness measurement or shields and auxiliary anodes need to be repositioned. reactivating after these processes is easy.
I think there is a common misunderstanding that electrodeposited nickel does not anodically dissolve without chloride. This is partially true. Nickel plated from a watts bath (without additives) is very pure and corrosion resistant. Nickel plated from a sulfamate bath is low stress because it always contains some sulfur and the sulfur makes the nickel less corrosion resistant similar to S nickel anodes.
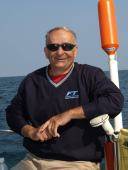
Pat Mentone
St Paul, Minnesota
July 31, 2008
A. Simple one to try in the lab is 20-30% H2SO4, Cathodic, 50 ASF (min), (try not to go over 5V in achieving this...) for 2-4 min. Watch out for etching.
No rinse, relatively quick transfer time.
Plate
Only works with relatively "clean" nickel deposits which I would assume you have out of an electroforming bath. May alleviate the need for a strike completely.
Try it out in the lab first, easy to do, if it works great, if not you are only out a few dollars of Sulfuric.
- Middletown, Pennsylvania
August 8, 2008
Q. I need to deposit a copper plate on the surface of a chrome plated antique chrome part using a copper strike plating solution. The initial step is an immersion in a hydrochloric acid solution to strip the chrome plate from the nickel plate. The resulting nickel surface needs to be activated prior to immersion in the copper strike.
This topic comments on the use of a cathodic cyanide cleaner for this purpose. What operating conditions pertain to this procedure (chemical composition, temperature, etc.)?
Another response to this question (topic 17382) referenced a procedure in the Canning Electroplating Handbook based on the use of H2SO4, KI, and solid iodine. Any practical comments on this procedure?
Plating shop employee - Providence, Rhode Island, USA
May 21, 2018
A. Yes. I've used the Canning activation process with good results more than a dozen times.
However, after stripping the chromium, you must buff, at least lightly, the nickel, then clean (scrub, if necessary, but no current), rinse, rinse, Canning activation, rinse and go right quickly into nickel plating.
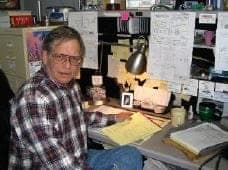
Jeffrey Holmes, CEF
Spartanburg, South Carolina
May 21, 2018
Q.
With chrome plated steel parts we sand the surface after chrome stripping to remove the nickel oxide layer and immediately immerse into the copper strike to deposit copper on the surface.
Many zinc die cast parts have geometric shapes that prevent a mechanical approach to remove the nickel oxide layer and 'activate' the surface. We would be unable to buff the surface prior to immersion in the iodide solution as recommended in your description.
Question: Can the buffing step be eliminated? Can immersion in a room temperature or heated iodine solution result in removal of the oxide layer?
Don
Plating shop employee - Providence, Rhode Island, USA
May 23, 2018
adv.: Supplier of Copper Anodes, Nickel Anodes, Bismuth Metal, & Other Metal Products for Industry & The Arts
Q, A, or Comment on THIS thread -or- Start a NEW Thread