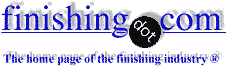
-----
Tin-copper galvanic corrosion in electrical contacts?
Q. Does the exposure of copper in tin plated electrical contacts result in any galvanic corrosion (to the tin) when subjected to high humidity/high temperature environment. I am seeing darkening of the tin (after high temp/humidity during reliability evaluation), at the edge where the plated strip has been cropped off. The rest of the tin, away from the cropped region does not show any discoloration. Not sure what the nature of the dark surface is. Could this be oxidation? What is the driving force? Should I be concerned?
Thank you,
Interconnects/connectors - San Jose, California, USA
2005
A. It may be just burnt on account of high temperature, millions of lugs are used all around the world with copper-tin. If you want no discolouration, then use a thin nickel plating in between.
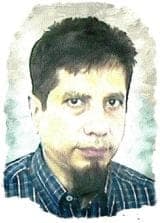
Khozem Vahaanwala
Saify Ind

Bengaluru, Karnataka, India
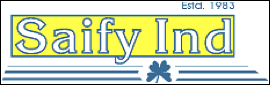
2005
Q. Thanks Khozem,
The test condition is around 60 °C / 93% RH. Not enough to burn the coating.
I heard concerns about corrosion/oxidation of the pure tin, with the resultant whiskering, and potential shorting.
My question is: does oxidation merely happen due to moisture/high temperature, or is the presence of exposed copper needed to accelerate the corrosion (galvanically)?
- San Jose, California, USA
2005
A. Copper ions will migrate thru a thin tin layer. The higher the heat, the faster the migration. Your dark color is quite probably a copper-tin alloy. It should continue to be functional for a rather long time, but not beautiful.
The nickel layer between the copper and the tin stops/greatly reduces the migration.
- Navarre, Florida
2005
A. The darkening is due to the formation of oxides of tin and copper.
Edges are normally more prone to corrosion attack. For this reason, in salt spray tests, sealing of the edges of the test panels is suggested.
At high temperature, the rate of oxidation of tin will increase. Besides, Cu-Sn Intermetallic compounds, namely Cu6Sn5 and Cu3Sn, will also form at the interface. The formation of tin oxides and the intermetallic compounds will affect the contact resistance and the reliability of the connectors. Because of these reasons, tin plated copper contacts are not recommended for high temperature applications.
The formation of intermetallic compounds due to the diffusion of copper could be prevented with the use of a nickel undercoat.
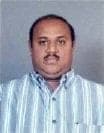
T.S.N. Sankara Narayanan
- Chennai, Tamilnadu, India
(ed.note: The good doctor offers a fascinating blog, "Advancement in Science" )
2005
A. I have subjected PPF frames with 100% Sn plating and after L3 Preconditioning (30 °C / 60% RH), I also noticed the darkening of the leads. The Ni+Au-Ag flash should have blocked the Cu migration. Could this darkening be caused by other than the Cu to Sn intermetallic?
Mya KohSemiconductor - Singapore
2006
2006
A. There is no doubt that in the high temperature / humidity environment of the test Sn will suffer from galvanic corrosion if coupled to copper.
Indeed, as already mentioned in this discussion, this has emerged as a major concern in damp - heat testing of tin plated component terminations for whisker growth.
As a rule, if there is no exposure of copper, galvanic coupling shouldn't occur; however, the tin coating may be porous or damaged, and depending on thickness this may also results in galvanic coupling and corrosion.
The same may happen with a nickel barrier. Indeed, this is a thin film, as a rule, and it may be damaged or porous.
But MIND: in all cases, both copper and tin surface must be exposed to the environment and close to each other to produce the galvanic couple and the resulting corrosion.
So no surprise, that it was noticed at the cropped edge.
Hope this may be of help.
Regards,
- Milan, ITALY
Hi. Sounds to me like Antonello has understood the proposition especially well.
Hassan used the word "cropped" and I think, as Antonello apparently does, that Hassan is saying that his component is made of sheared preplate, and therefore has bare copper edges. In that case, certainly there can be corrosion of the exposed copper and galvanic activity as a result of the exposure of the two different metals in close proximity.
Regards,
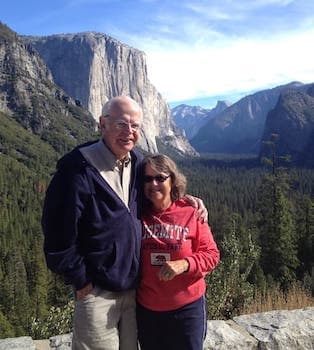
Ted Mooney, P.E. RET
Striving to live Aloha
finishing.com - Pine Beach, New Jersey
Q, A, or Comment on THIS thread -or- Start a NEW Thread