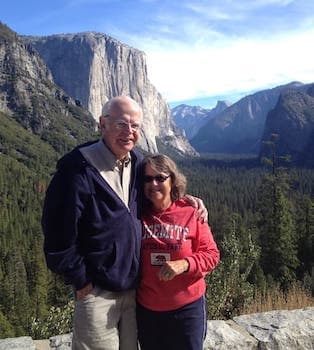
Curated with aloha by
Ted Mooney, P.E. RET
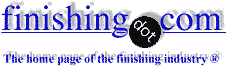
The authoritative public forum
for Metal Finishing 1989-2025
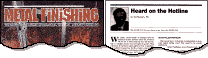
-----
Diffusion Treatment Of 316 Stainless Steel
Q. Hello. We sent these parts for Diffusion Treatment and came back stained. Is this normal or something went wrong?
Javier CostasQuality Manager - San Diego, California
April 27, 2022
----
Ed. note: If you send pics of this staining to mooney@finishing.com for posting here, it will probably be easier for readers experienced with the process to advise whether it's normal or not.
A. Javier,
"Stained" is such an imprecise term in the metals world. Sometimes "stained" refers to some residue of something that has dried on the surface. More often it means the surface has been etched by some chemical attack. In your case with the diffusion treatment/coating, it may mean the coating was unevenly applied or cured unevenly or some such thing.
In any event, it sounds like this was done by an outside vendor, so you likely need to have a discussion with them about your desired results versus what results they claim are achievable.
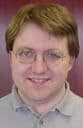
Ray Kremer
Stellar Solutions, Inc.

McHenry, Illinois
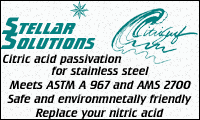
May 3, 2022
⇩ Related postings, oldest first ⇩
Q. My company is trying to identify a process used to modify the mechanical properties of 316 stainless steel. 316 is used for the control element in metal-seated gate and ball valves. We have seen samples of 316 valve components that have been manufactured using a process that produces a hard Rc70+ surface finish that doesn't affect the corrosion properties of 316. The process is claimed to add lubricity, resists galling, and can be done to finished components without distorting or changing the dimensional tolerances on the components. We understand this process can be used on any ferritic material. Treated components have a black, semi-gloss appearance.
Can anyone help us identify this finishing process so we can have some test pieces done to see if we can achieve these goals?
Valve Distributor - Vancouver, BC, Canada
2005
A. Sounds to me like salt bath nitriding, or possibly a cryogenic treatment or ion implantation. The nitriding sounds most likely.
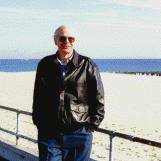
Ted Mooney, P.E.
Striving to live Aloha
finishing.com - Pine Beach, New Jersey
2005
A. We all could get a better idea if you told us how thick is the coating you're looking for (or after). Nitriding matches your described color but its main disadvantage is that it reduces the corrosion resistance of SS. So, it may very well be something else.
Guillermo MarrufoMonterrey, NL, Mexico
2005
Q. We're told the process provides a treated depth of 0.020 to 0.030". Our application is for the blades (gates) in knife gate valves used in mining and pulp mill applications. We use 316 plate for the gates, but run into problems in line media that is sticky or contains abrasive particles. We've tried Xylan (Teflon) coating the gates, which solves the sticking issue, but doesn't provide any protection against abrasion. We've tried are making the gates out of T15 tool steel, but they don't handles corrosive fluids well. 17-4PH stands up well against the abrasion, but it's chemical resistance is poor compared to 316 and it's quite expensive. Another option we've tried is applying a Stellite weld overlay to the gate leading edges, requiring considerable machining to get consistent finished sizes and is unpredictable when our process temperatures vary - the gates warp and will no longer shut-off properly.
Bottom line is we've been told a process like nitriding will do what we want, but we don't want to spend a huge amount of money trying 382 different process before we find one that works. What we are looking for is a company who can suggest some methods to achieve what we're looking for - narrow it down to 6 to 12 potential finishing systems so we can run tests to see how close we can get to our ideal product.
- Surrey, B.C., Canada
2005
A. 20 to 30 thousandths sound within modern HVOF range capabilities. Nitriding will not penetrate that far w/o loosing its hardness. Besides, it wouldn't do any good to the overall corrosion resistance of 316SS. Another option could be composite nickel or cobalt electroplating with SiC or other hard stuff. Both processes are low temp, highly technical and expensive, and will require smoothing out the surface.
Guillermo MarrufoMonterrey, NL, Mexico
2005
A. Electroless nickel, heat treated after plating, will provide a hard and corrosion resistant surface, and may do what you need done. 0.030" is probably not practical, but may well serve the purpose a few mils thick.
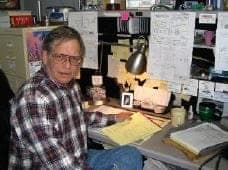
Jeffrey Holmes, CEF
Spartanburg, South Carolina
2005
A. For your application you can go for salt bath nitriding and
followed by oxidizing process.The treated parts will have black color finish.
- Bangalore, Karnataka, India
2005
A. Sheldon -
There are a few Heat Treat shops locally that would probably let you try a test piece ( or two) at no charge. I would look in the yellow pages under Heat Treating-metal to find out who they are.
- Surrey, BC Canada
2005
A. This sounds like the kolsterising process to me, which seems to be a carburizing process.
Jeroen Heijneman- Zevenaar, The Netherlands
2005
----
Ed. note: See thread 28871 for more on Kolsterizing
Q, A, or Comment on THIS thread -or- Start a NEW Thread