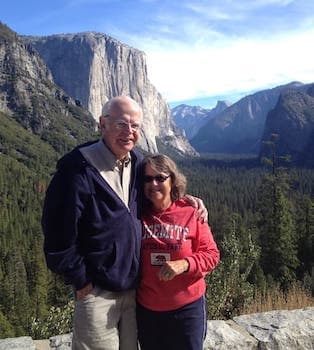
Curated with aloha by
Ted Mooney, P.E. RET
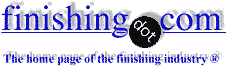
The authoritative public forum
for Metal Finishing 1989-2025
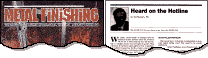
-----
STEP test problem in Duplex Ni Plating Plant
Q. We are not achieving Potential Difference (STEP value) between two layers of Nickel - Semi Bright and Bright. The solution is already purified by Carbon, High pH, Oxidation treatment. sulfur content in Semi Bright is 0.002% and 0.04% in Bright solution. Request your advice.
A.K.Kansal- India
2005
A. The pH of the semi bright nickel should be 0.5 lower than the bright nickel.


Sara Michaeli
Tel-Aviv-Yafo, Israel
2005
2005
A. Hello Sara,
We have gotten used to maintaining the same pH in both baths on account of adhesion issues with the lower pH in the SB.
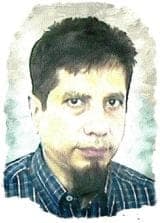
Khozem Vahaanwala
Saify Ind

Bengaluru, Karnataka, India
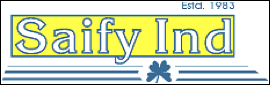
A. You can operate your SB at pH 4 and your bright nickel at
4.5.
I still cannot understand what does it have to do with adhesion.


Sara Michaeli
Tel-Aviv-Yafo, Israel
2005
A. Hi there,
If everything is in order in terms of ph , sulfur content, temperature, bath chemistry, then the things wrong may be with the additives used in semi-bright nickel. Request for a special additive to increase the potential difference in semi-bright nickel just check in Hull Cell adjusting the make up and maintenance additives. Please also look for the rinses and filtration before semi-bright and try to improve filtration in semi-bright.
Regards,
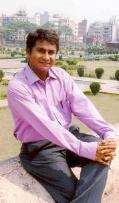
Praveen Kumar
plating process supplier
Mumbai, India
2005
2005
A. Dear sir,
sulfur is not the only criteria; you need to check Impurity level as well. Step value mainly depends on semi-bright as well as bright additives. Talk to your supplier.
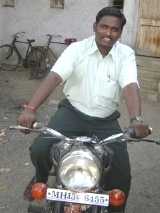
Vishwas Nangare
motorcycle accessories mfgr.
- Aurangabad, Maharashtra, India
A. Dear sir,
First you see in Hull Cell panel; it must be semi bright effect (HCD dull, LCD little bright). If it is totally bright than please add STEP booster with initial additive. Don't use maintenance additive until you get semi-bright effect; and continuously run filter with carbon.
It will definitely give you best result with STEP TEST.
THANKS,
VIJAY
- Mumbai, Maharashtra, India
2007
Q. I also face same problem (STEP test value). In our plating shop, some of the chemical can be analyzed (basic salt, leveler, pH). However, we don't know how to check maintenance additive which gives the STEP reading. Supplier not help much on this issue. Our plating thickness for semi bright is 1.5-2 micron and Bright Nickel 3.5-4 micron?
Is it ok?
As far as I know, if ratio between Semi-bright and bright Ni thickness too far, you can get high STEP reading, but the potential graph will not be good enough to be used.
On carbon treatment to remove sulfur, does it work? Another issue with carbon treatment is, it will remove other additives too (leveler, wetter)?
- Johor Bahru, MALAYSIA
January 13, 2012
January 18, 2012
A. Dear Norddin,
Absolutely your thickness is too low and the opposite from normal practice (lower thickness on semibright nickel and higher thickness on bright nickel).
Normally in automotive field, people plate Semibright Nickel almost 1:1, e.g., 10 microns Semibright and 10 microns Bright Nickel with total 20 microns,
but some people plate with total thickness 25 microns, then they use 15 microns Semibright nickel and 10 micron bright nickel.
In your case I think total thickness just 5 - 6 micron, to have single layer with 10 micron is better than duplex nickel (corrosion resistance low, and brightness not enough).
STEP value is dependent of the type of additive, ask your supplier; in old days <100mV is enough but nowadays must be > 100-140mV as I heard.
For improving STEP, some branded suppliers got tools called STEP repairing additive.
Mostly STEP went down due to heavy load of organics in Semibright nickel (Hull Cell looked strange), either from pre-treatment (cleaners) or leveler additive or wetting agent.
Just do carbon treatment in semibright nickel solution (some branded supplier called Active Aids) and in my older time we can put a bit of formaldehyde in semibright nickel solution to improve the STEP (test in Hull Cell bit by bit and you can see the Hull Cell pattern will come back as normal), but I don't know whether it's allowed or not right now.
Good luck.
Best regards,
- Jakarta, Indonesia
February 1, 2012
Thank you Mr. Tony, really appreciate your time to give feedback on my problem.
Q. I would like to ask further on the thickness ratio between Semibright and Bright Nickel. Is it still same if later process after bright nickel is Satin Nickel?
If not, what is the best ratio between Semibright, Bright Ni and satin Nickel for automotive part? In my opinion satin nickel does not influence much on the STEP test reading.
regards
- Johor Bahru, MALAYSIA
March 11, 2012
A. Dear Noordin,
You must have a 2:1 ratio of semi-bright to bright nickel for good corrosion resistance. For improving the STEP result use as less additives as possible in the sulfur free plating and keep the bath in mint condition with regular treatments, etc. The bright nickel hardly has an influence on the step result.
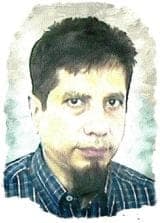
Khozem Vahaanwala
Saify Ind

Bengaluru, Karnataka, India
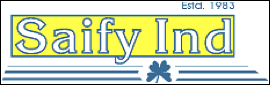
Q, A, or Comment on THIS thread -or- Start a NEW Thread