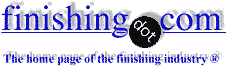
-----
How to calculate Cathode Efficiency in Plating
Q. What is the procedure for measuring/calculating Cathode efficiency if colometer [ed. note: Coulomb meter = Ampere-second meter?] is not available?
V. Ranga Bhuvana Balajiengine valves - Medchal, Andra Pradesh, India
2005
2005
A. Cathode efficiency is simply calculated by actual weight of metal deposited divided by theoretical weight of metal as per Faraday's Law.
Okay: Then how to calculate as per Faradays Law?
Weight as per Faradays Law is equal to
AWite / VF
where AW = Atomic weight of metal being deposited
V= Valance (Number of electrons required to deposit one atom)
I = Current flowing through the plating solution
t = Time duration of current flow
e = cathode cathode efficiency ( % of current that deposits the metal)
F= faradays constant = 96485 * A seconds or 1608 * A mins or 26.8 * A hours per equivalent weight.
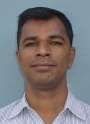
V. G. Rajendran
- Trichy, Tamilnadu, India
2005
A. Mr. Balaji,
1. Take your working solution in a liter beaker [beakers on
eBay
or
Amazon [affil links] .
2. Maintain your working solution temperature.
3. Place Conforming Lead anodes.
4. Plate an accurately known surface area (preferably a steel mandrel with no sharp edges) at your operating Current Density.
5. Note that the current and Plating Duration have to accurately controlled and measured.
6. % Efficiency = ((W2-W1)x 18560)/(Amps x minutes)
W2 and W1 are weight of substrate (in grams) after and before plating measured to four decimal places.
Hope this information helps.
- Toronto, Ontario, Canada
A. Testing in the lab with conforming anode and somewhat closer anode to cathode spacing will give a false answer compared to a part in the tank with tank anodes and a different power supply. It is OK if you do not mind a 20 to 50% error.
James Watts- Navarre, Florida
2005
Q. Sir, can you please help in calculating electrochemical equivalent weight of an alloy, for instance Ni-W(53:47), to calculate current efficiency of an alloy.
u pramod kumar- coimbatore, tamilnadu and India
March 22, 2015
A. Hi. The calculation isn't different than previously described, nor difficult. You know the weight of the deposit, and you know the percentage nickel and percentage tungsten in it, so you know the weight of the nickel you deposited and the weight of the tungsten you deposited.
Now just calculate how many ampere minutes that much nickel ought to require per Faradays Law, and how many ampere minutes that much tungsten ought to require, and simply add them together. This calculated number of ampere minutes divided by the actual measured ampere minutes is the cathode efficiency.
It would probably be interesting to the readers to know why you care though. Thanks.
Regards,
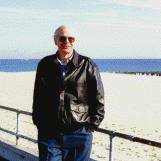
Ted Mooney, P.E.
Striving to live Aloha
finishing.com - Pine Beach, New Jersey
March 2015
August 7, 2015
Q. Please,
I have a question concerning the calculation of the cathodic efficiency through this relationship --
cathode cathode efficiency % = (W / Wt) * 100
Where (W) is the experimental weight of the deposit and (Wt) is the theoretical weight of the deposit.
The theoretical weight of the individual metal deposited can be calculated as follows:
Where (Q = I x t) is the amount of electricity passed through the cell and expressed in ampere seconds and Faraday's constant is 96485.
I = Current flowing through the plating solution
t = Time duration of current flow
e = cathode cathode efficiency ( % of current that deposits the metal)
F= faradays constant = 96485 * A seconds
My question is how to calculate Wt, for example in the case of tin plating (SnSO4) in the presence of H2SO4 acid medium.
The Electroplating is done at a current density of 15 mA / cm 2, for 10 min. Then Q = 15.10-3 * 600
-- or how to calculate 'Equivalent weight of metal'?
Cordially
- kenitra morocco, North africa
August 2015
A. Hi Abdelillah. The beauty of Faraday's Law is not its complexity but it's dead easiness. So, before you get too wrapped up in all those constants and variables and formulas, please forget them for 2 minutes and just follow this thought experiment. If you do, I promise that you will understand it completely and with crystal clarity:
Just picture one Sn++ ion drifting around in your solution of plating salt.
It's no more complicated than this:
So if you pump a whole bunch of electrons from anode to cathode, for every two electrons you move, you'll move one atom of Tin from the anode to the cathode.
Now, an atom of tin has a given atomic weight, which happens to be 118.71 (look it up in the Periodic Table). It happens to oxidize in the "plus 2" state in stannous sulfate as we've both noted, such that you have to move two electrons to move only one atom, as we've said. So a gram equivalent weight of stannous tin is 118.71/2 or 59.36 grams.
The Faraday constant, 96485, is nothing more than a conversion factor between atomic weight, coulombs (ampere-seconds), and Avogadro's number; and it simply enunciates that 96485 amp-seconds will move 1 gram equivalent weight of metal from anode to cathode because of the simple mechanism we have been talking about. Therefore 96485 amp-seconds will move 59.36 grams of stannous tin from anode to cathode.
But something else might sometimes happen with some of those electrons we moved from the anode to the cathode rather than their always converting Sn++ ions to Sn0 atoms. For example, suppose we applied a sudden big surge of electricity: atoms can't instantaneously dissolve into solution from the anode and migrate through the solution over to the cathode at the speed of light. So what will probably happen in that case is that the excess of electrons accumulating on the cathode, with not enough Sn++ ions in the vicinity to satisfy them, will start pulling hydrogen out of the surrounding water, converting the water to H2^ gas and 2OH- ions. That's where your efficiency factor comes into play: Faraday's Law still held overall if you count both tin and hydrogen, but you didn't want hydrogen, so that is an inefficiency in your mind -- and your "efficiency" is the percentage of electricity which actually served to deposit tin. You calculate it by dividing the actual weight of tin deposited by the theoretical amount that would have been deposited according to Faraday's Law (as your opening sentence addressed).
Luck and Regards,
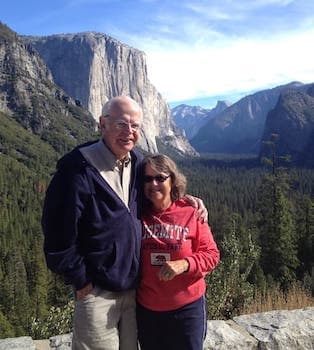
Ted Mooney, P.E. RET
Striving to live Aloha
finishing.com - Pine Beach, New Jersey
Thank you very much Mr. Ted Mooney' for your explanation.
- kenitra morocco, Nord africa
August 16, 2015
Q. I have 3 Alkaline Zinc barrels and I wants to calculate Current efficiency, what is the Method?
Zn -12 gm/lit, NaOH 130 gm/lit, Barrel RPM 6
Load 35 kg, Barrel capacity 50 kg, Ampere-350 @1 A/dm2
time 60 mins.
Thickness I can [ed. note: can't?] measure accurately of all 35 kg please guide me.
Thanks,
- nanded Maharashtra, India
September 17, 2015
A. Hi Vinayak. We appended your inquiry to a thread which explains what "efficiency" is: it is the amount of metal actually deposited divided by the amount that should have been deposited according to Faraday's Law. If you know that you have applied 350 Amps for 60 minutes, you know how many Amp-hours you have applied, and I also explained how to determine how much metal should thus have been deposited.
Your problem is: if you do not know how much metal you have deposited, you cannot determine the efficiency. So how are you going to determine how much metal was deposited? You may have to rely on your supplier's estimate of efficiency if you can't determine how much zinc you have deposited.
Regards,
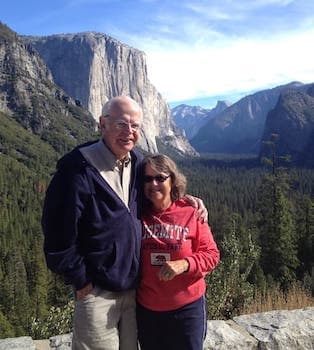
Ted Mooney, P.E. RET
Striving to live Aloha
finishing.com - Pine Beach, New Jersey
Hi Ted
Thanks
My Target Thickness is 8-10 microns.
Practically I observed lot of thickness variation in barrel thickness because of barrel rotation.
I have a destruct thickness machine which is giving 8-9 microns.
And do not have X-ray facility to check thickness.
Please advise.
You mean to say I have to calculate total weight of deposit-minus weight of Base material.
If yes, then how are further calculations?
Thanks.
- NANDED MAHARASHTRA INDIA
September 2015
Hi VINAYAK. I don't know why it is important to you to calculate efficiency, but as explained, it is the ratio of how much metal was actually deposited divided by how much metal should have been deposited by Faraday's Law. So you can't do the calculation without both numbers.
The first number can be estimated from thickness measurements, from anode usage over the long term, or from weight gain of the parts.
The second number is determined from ampere-hours of current consumed, as explained on this page. If you did not follow how that is done, I can clarify if you tell me what part you are not understanding. But once you do the division, there are no "further calculations".
But as the enquiry stands right now, it sounds like you are asking how to calculate the efficiency preferably without accumulating the necessary information; and that is not possible. If it is important to you to know the efficiency, that's what you would need to do. Good luck.
Regards,
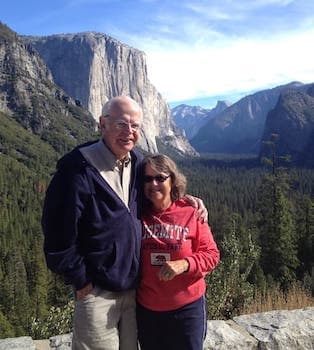
Ted Mooney, P.E. RET
Striving to live Aloha
finishing.com - Pine Beach, New Jersey
September 19, 2015
Hi Ted
Thanks a lot,
I want to calculate bath efficiency because some of chemical supplier told myth I want to calculate & compare.
cathode cathode efficiency % = (W / Wt) * 100
pl rectify me if m wrong
Case I-or Method I
Suppose I take weight W2-W1 (After Plating-Before plating) is X then how are further calculations?
(Time 60 mins & Amps are 360)
Case II-OR Method II
for 700 lits bath
WE will start at 14 gm/lit metal & 140 NaOH & anodes are M.S. anodes (We remove all Zinc anodes)
We run bath up 1000 Amp.hrs then Analyse Zinc metal suppose its 12 gm/lit
(again my plating time is 60 mins & amps 360)
Please help me to derive efficiency
Thanks
Vishal
- NANDED, MAHARASHTRA, India
September 2015
Hi again, Vinayak. Your efficiency formula is correct, and method 1 or method 2 can be used to calculate "W", the actual weight gain. You can do both methods together as a check on each other if you wish.
But I don't like to do arithmetic for you and it won't help :-)
So start with:
1). How many amp-hours you are applying?
2). How many Faradays is that?
3). How many gram-equivalent weights should it therefore deposit?
4). How much does a gram equivalent weight of zinc weigh?
5). So much weight of metal should be deposited.
Tell me any term or any step you don't understand. Thanks!
Regards,
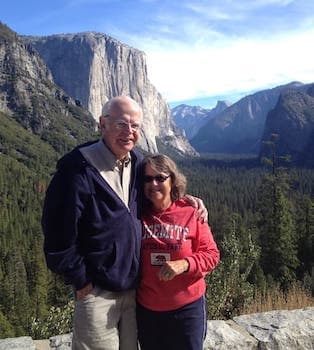
Ted Mooney, P.E. RET
Striving to live Aloha
finishing.com - Pine Beach, New Jersey
September 21, 2015
Hi Ted
Good Evening
1). How many amp-hours you are applying? 360 Amp x60/60=360 Amp hrs/lot
2). How many Faradays is that? Can't tell?
3). How many gram-equivalent weights should it therefore deposit?1.22 x 360=439.2 gm is it correct?
4). How much does a gram equivalent weight of zinc weigh? can't tell
5). So much weight of metal should be deposited. can't tell
Ted you help me a lot if you can simplify me I would be grateful.
plating owner - NANDED, MAHARASHTRA, India
September 2015
Hi. I don't know exactly how to simplify for you, but if you read the page and tell me what words or phrases or concepts you are not understanding, I can try different words.
1). Correct.
2). 360 Amp-hrs is 1,296,000 amp-seconds because there are 3600 seconds in an hour. We have tried to make clear on this page repeatedly that a Faraday is 96485 ampere-seconds or coulombs. So 360 amp-hours or 1,296,000 amp-seconds is 1,296,000/96485, or 13.43 Faradays. Once you understand what a Faraday is, this was baby arithmetic.
3). Therefore it should deposit 13.43 gram equivalent weights because of the definition of a Faraday (Sorry, I don't know what your "1.22" represents).
4). A gram equivalent weight of zinc is the atomic weight of zinc divided by the oxidation state, or 65.38/2, or 32.69 grams.
5). 13.43 gram equivalent weights x 32.69 grams per gram equivalent weight = 439 grams.
Again, please carefully read this whole page and tell me what words or concepts you are having trouble following, because you need to understand the concepts so you can apply the arithmetic. Having me do arithmetic for you for one case probably won't help you. Good luck.
Regards,
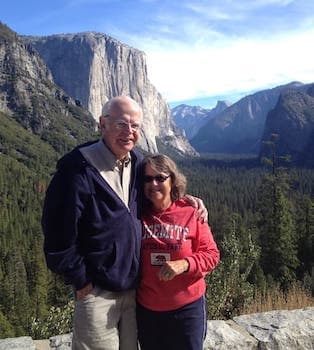
Ted Mooney, P.E. RET
Striving to live Aloha
finishing.com - Pine Beach, New Jersey
October 20, 2015
Q. Hi Ted,
Sorry for trouble you again.
Please check calculations.
w/wt*100 = efficiency
weight before plating 23.05 kg & after 23.4 = 0.35 kg = 350 gms
so Wt = 360 amp-hr = 360*3600/96485 = 13.43 Faradays * 32.69 = 439 gms
Therefore cathode efficiency = 350/439*100 = 79.72%
Is it Correct?
Please advise.
Vinayak
plating owner - NANDED, MAHARASHTRA, India
Hi Vinayak. Yes, that sounds exactly right to me!
Regards,
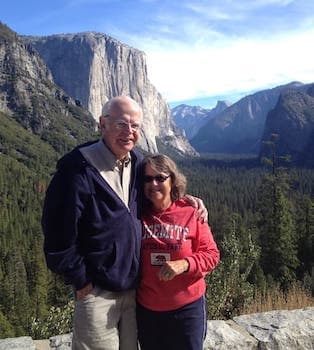
Ted Mooney, P.E. RET
Striving to live Aloha
finishing.com - Pine Beach, New Jersey
October 2015
Calculating alkali zinc plating bath optimal efficiency
Q. Hi everyone, I'm new to the plating industry and I was wondering how do I conduct an experiment or study of somesort to get the optimal current density, given that the zinc plating bath has a wide operating range of concentration. How does efficiency relate with current density? I've read that at higher current densities the deposition efficiency changes but how can I quantify it? Where can I read related literature about this things?
Any advice or help will be deeply appreciated. Cheers.
- Philippines
October 21, 2015
A. Hi Kelvin. We appended your inquiry to a thread about calculating efficiency in alkaline zinc plating baths. Usually, you purchase these plating chemicals as proprietary processes, and you get the benefit of experienced technical service people to guide you in proper application. But the biggest source of inefficiency is the reduction of water into hydrogen gas instead of the deposition of zinc, and inefficiency is usually highest at low current density and lowest at high current density.
Usually, high quality plating at good production rates is sought, but high efficiency is not deliberately sought as a specific target.
Regards,
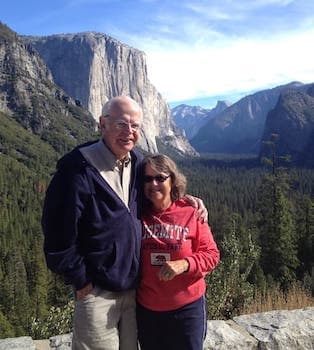
Ted Mooney, P.E. RET
Striving to live Aloha
finishing.com - Pine Beach, New Jersey
October 2015
Q, A, or Comment on THIS thread -or- Start a NEW Thread