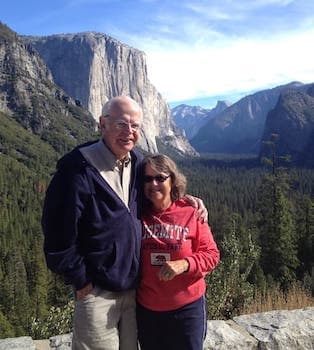
Curated with aloha by
Ted Mooney, P.E. RET
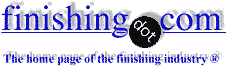
The authoritative public forum
for Metal Finishing 1989-2025
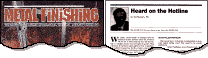
-----
Black Oxide Vs. E-coat
Q. My company is having an off shore part made that used to be made in the States. Previously the part had an E-coat finish. The off-shore place wants us to change to a Black Oxide finish. The part is a shaft that is going to be inserted into cast aluminum. The shaft then sits in a delrin bushing. What is the difference in the lubricity of these two finishes and should I be concerned about them? What about the difference in the thickness of these two finishes?
Mollie L [last name deleted for privacy by Editor]manufacturer - Easton, Pennsylvania
2005
One thing for sure is that the off-shore supplier will be able to black oxide the parts less expensively than your domestic supplier was able to e-coat them :-)
A. Black oxide has no discernible thickness (a few millionths of an inch), the e-coat thickness depends on what kind of coating was specified (Teflon, simple prime coat, etc.), but will be something like a few ten thousandths of an inch thick to maybe as much as one thousandth of an inch. The coefficient of friction of black oxide would be the same as steel, because that's what it is, and it will wear through immediately. The coefficient of friction of the e-coat would vary depending upon what kind of polymer is being applied --you must have had some spec for type of coating and thickness?
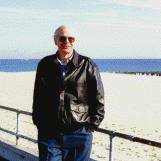
Ted Mooney, P.E.
Striving to live Aloha
finishing.com - Pine Beach, New Jersey
2005
A. The e-coat gives good corrosion resistance while the black oxide has no protection at all. I cannot understand how one can compare one to the other.


Sara Michaeli
Tel-Aviv-Yafo, Israel
2005
Agreed, Sara! The first sentence of my reply was satire, but apparently too obscure...
The manufacturer went offshore to try to reduce their costs, but the offshore finisher wants to provide a cheap, poor quality finish to make the promised cost savings actually possible :-)
That cost reduction could have been made without going offshore, and the manufacturer would have been able to discuss it locally and see and understand the difference instead of "throwing it over the wall" and operating blind :-)
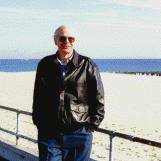
Ted Mooney, P.E.
Striving to live Aloha
finishing.com - Pine Beach, New Jersey
2005
Q. E-coat vs. Black Oxide. What is the difference?
Rob CollinsQuality - Anderson, Indiana
Q. I'm trying to understand (in general) if black oxide finish is less expensive than e-coating?
Currently I have a small steel stamping (approximately 170 mm x 170 mm x 100 mm) which is getting e-coated but I'm thinking that black oxide will be less expensive (I'm not worried about appearance or salt spray on this part).
Is there a "general rule of thumb" (i.e., coating cost per stamping weight) which can typically be applied for cost estimating?
Any insight would be greatly appreciated.
Automotive Seating - Farmington Hills, Michigan, U.S.A.
June 8, 2015
by Electrocoat Association
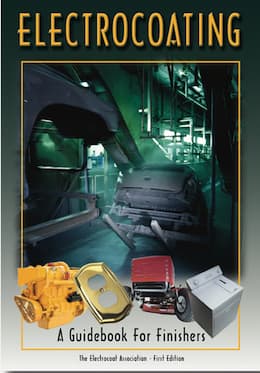
on eBay or
AbeBooks
or Amazon
(affil links)
A. Hi, Nelson. In order to help readers who may be following this, let me start by addressing Rob's question first even if my answer is not timely enough to help him. Most metal finishing books have chapters on black oxide, and there are whole books about e-coating, so this answer is obviously extremely abbreviated, but briefly ...
Black oxide is a finish that can only be applied to iron and steel (and with some modifications to stainless steel). It is an extremely thin engineered "rust" formed by putting the parts into a very hot aqueous bath with strong caustic soda ⇦liquid caustic soda in bulk on Amazon [affil link] and nitrites or other oxidizing agents. It can be fairly attractive, and gains its very minimal corrosion resistance from the waxes or oils applied to it. Typical applications include sprockets & gears & power transmission components where you want to make them look good without affecting the tight tolerances on bores, and firearms where the owner enjoys tinkering away, lovingly wiping them down and oiling them after each outing. Again, with wax or oil the corrosion resistance is minimal; without it, it is essentially zero -- black oxided parts sometimes flash rust in the finishing shop awaiting their trip to the wax dip tank.
E-coating, also called electrocoating, electropainting, electrophoretic lacquering, and cathodic electro-deposition (CED), is a process for very uniformly applying a very thin layer of paint to metallic parts. Operationally it is rather similar to electroplating, except that it applies organic paints instead of metal coatings. Just as parts to be electroplated are not placed into molten metal, but into an aqueous bath where ions of metal are dissolved and are converted to metal by electricity, electrocoating tanks don't quite contain "paint" -- they contain organic ions that are converted to a paint layer by the electricity. One advantage e-coating has over electroplating is that the deposited paint is an insulating covering, so once one spot on the item has been electrocoated, the electricity flows to exposed metal areas resulting in a thin uniform coating with no holes or missed areas. Electrocoating can be used either as a primer under other finishes like powder coating, or as a stand-alone finish.
I wish there were rules of thumb for quick cost estimating, and I've seen them in many other industries, but I've personally never seen one for metal finishing -- although I've heard that some large aerospace companies have such notebooks for internal use. Part of the reason may be that a substantial part of the cost is material handling, so trying to estimate the finishing cost based on the finishing process can be a case of "the tail wagging the dog" where changing the parts dimensions a little changes the cost so dramatically that it renders the differences based on finish almost moot.
For example, some black oxide on stampings is done in bulk (baskets or barrels), whereas the parts must be individually racked for electrocoating. An electrocoating line is usually a million dollar affair, whereas many midsize firearms shops have black oxide capability they have put together for a couple of thousand dollars. So black oxide should be less expensive in most cases, but darned if I can quantify it at all. Asking for quotes seems to always be the way to go :-)
Regards,
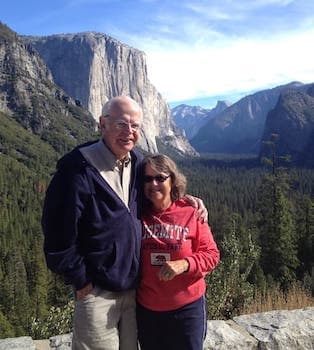
Ted Mooney, P.E. RET
Striving to live Aloha
finishing.com - Pine Beach, New Jersey
June 2015
Can we apply e-coating on top of a black oxide finish?
Q. We are currently using hardware for many of our products that is black oxide coated and we see that they are rusting. The reason for going with the Black oxide finish was to prevent rusting. Now we are seeking information on E-coating to help prevent the rusting. My question is, can black oxide coated hardware be e-coated? If so, does anyone have a preferred vendor? Thank you for your time and assistance today!! :)
Jenn
off road equipment - Warren, Pennsylvania USA
August 11, 2015
A. Hi Jennifer. You might consider retaining a finishing consultant to help you make these design and sourcing selections...
I don't know whether the parts your company offers are for undercarriage use or are more decorative and accessible like track lights. But generally, black oxide should never be specified for any application requiring corrosion resistance as it offers none beyond that resulting from periodic waxing or oiling.
Yes, I think you could e-coat on top of the black oxide -- but black e-coating on bare, phosphated metal would probably be better for many reasons. If these are undercarriage parts, rather than parts which require an attractive black oxide look, you can also consider Autophoretic coating.
We don't post product or sourcing recommendations on these pages, but perhaps one of our supporting advertisers who offers those services will reach out to you. Good luck.
Regards,
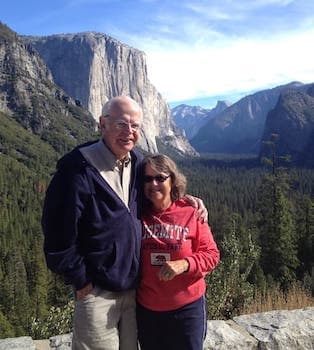
Ted Mooney, P.E. RET
Striving to live Aloha
finishing.com - Pine Beach, New Jersey
August 2015
Q. Hello,
I recently received some black oxide parts made per MIL-DTL-13924
[⇦ this spec on DLA] D Class 4. The only reason for this finish is make it electrically insulating. Now I found that the color of black oxide comes off easily which is not desirable.
Is there any way we can convert oxide to e-coating or add a top non-conductive coating?
Suggestions will be very appreciated.
- Santa Clara, California, USA
June 8, 2016
Q, A, or Comment on THIS thread -or- Start a NEW Thread