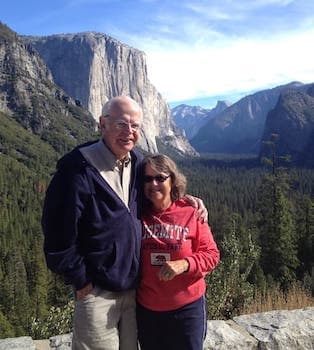
Curated with aloha by
Ted Mooney, P.E. RET
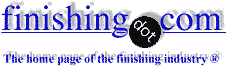
The authoritative public forum
for Metal Finishing 1989-2025
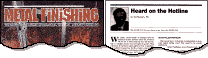
-----
Etching Solution for Inconel 625
December 6, 2021
Q. Hi All,
My company plans to set up inconel etching.
We are using Inconel 625.
What is the best solution to use for Inconel etching?
This is the solution suggested to me, but it's not 100% effective:
Nitric Acid: 10-30 g/L
HCl: 700-900 g/L
ferric chloride
⇦ this on
eBay or
Amazon [affil links] :150-170 g/L
- Penang Malaysia
ACRONYMS:
FPI = fluorescent particle inspection
Q. I am working in aerospace industry. We are performing etching prior to FPI and Shot peening on Nickel alloy.
Previously, the rust situation didn't occur. And now, we having some cases.
The quality of process is dependent on stock-loss test results. We complied with this requirement. But the surface had rust; it is unacceptable.
We have analyzed the rust composition, it mainly includes Cl, % rate Fe and Cr are decreased as initial material.
Do you have any ideas?
(Sulfuric acid 95.0-98.0 wt.%) 150 ± 5 ml
(Hydrochloric acid 35.0 wt.% ) 1880 ± 35 ml
(Nitric acid 68.0 wt.%) 510 ± 10 ml
(Glacial acetic acid
⇦ this on
eBay
or
Amazon [affil links] 99.5 wt.% min) 750 ± 15 ml
(ferric chloride
⇦ this on
eBay or
Amazon [affil links] -Anhydrous): as FeCl3 272 ± 5 g
H2O 840 ± 15 ml
- Hanoi, Vietnam
⇩ Related postings, oldest first ⇩
2005
Q. Dear sir,
I am looking for micro & macro etching solution for Inconel 625.
I used this solution
15 mL HCl
10 mL glycerol
5 mL nitric acid
-- but not good.
Thank you
Roorki University - Roorki, India
Nitric acid doesn't remove black oxidation layer
Q. I am using Inconel 625 as glass extrusion die. After the glass extrusion, a black layer of oxidation layer formed on the Inconel and it can't be removed by Nitric acid. When we reuse the Inconel extrusion die, the black oxidation particle is found in our extruded glass tube, hence affecting the properties of our glass tube. I would like to know if there is a way to remove this black oxidation layer. Thank you.
Jason Kiang- Charlton, Massachusetts
2005

Never use HF anywhere unless trained!
If you do, you MUST have the antidote gel on hand for instant use!
Calcium Gluconate
for HF acid burns
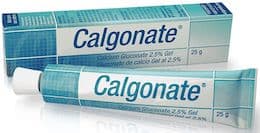
on eBay or
Amazon
(affil links)
A. Nitric acid is a strong oxidizing agent. No wonder it does not remove your oxide layer when used straight. Try mixing it with 7% hydrofluoric acid. Beware, this is THE most dangerous acid to all forms of life, burns have to be treated at once with shots of calcium gluconate around it. Another alternative, if geometry allows it, would be to use a very fine polishing paste.
Guillermo MarrufoMonterrey, NL, Mexico
2005
Q. Hello Guillermo, thank you for the advice, I would like to know if I need NaOH treatment on the Inconel surface before using the mixture of HNO3+7%HF in order to completely remove the Black oxidation. For the acid mixture is it 1:1 volume. Will the surface of the etched Inconel be rough. Please advice, thank you.
Kiang Kai Ming- Charlton, Massachusetts [returning]
2005
A. Excuse me, I forgot to tell you the mixture will be diluted 3 to 1. That is to say 300 mL/L nitric, 20 mL/L HF, rest water, temp 125 °F. This treatment will leave no visible etch at all to your die surface provided it is carefully attended not to over etch. Experiment first on a non working area of the die to calculate time. Regarding the pre treatment with NaOH, it is a good practice to use it to remove greases, oils and other soils that are not dissolved by acids. Silicon or teflon impregnated lubricants may require special pre-cleaning steps, special chemicals or mechanical means.
Guillermo MarrufoMonterrey, NL, Mexico
2005
A. Kiang, Guillermo is correct; an HF (or ammonium bifluoride) solution or brushable slurry (stainless steel weld descaler) should work. However, this is definitely not a Do-it-Yourself project for someone untrained in handling hazardous chemicals. It violates your company's safety policies and OSHA regulations. Locate a properly trained chemist or technician or welder to do this safely. Less expensive than a long-term injury and hospital bill.
What is the extrusion temperature and glass composition? Anything more reactive towards Inconel 625 than silica? Black color could be Fe+2 or Ni+2 or a carbide. Perhaps have the black material analyzed.
Also, contact Special Metals regarding this problem. Inconel® 603XL may be a better die material:
"The excellent resistance to oxide spalling make Inconel alloy 603XL an excellent choice for applications where oxide contamination can not be tolerated such as the electronics, glass and ceramics/tableware industries."
- Goleta, California

Rest in peace, Ken. Thank you for your hard work which the finishing world, and we at finishing.com, continue to benefit from.
2005
How to etch Inconel 625 .0003-4" quickly
Q. I am in a midwest anodizing shop. I need to pull .0003-4" in 20 min from Inconel 625 for a pre pen etch. For most of the common reasons I would like to keep this ambient in temp, and something I can titrate the constituents or use etch rate as the determining factor for the active ingredient. If possible I would like to go with HF and Nitric but have so far tried almost all variations there. I have found that the bath quickly losses its punch. I believe that nitric is less effective above 45% and have tried to etch with HF concentrations of 2-70%. I did get closer using heat although not close enough to justify 150 degree HF.
I have read a few others based on Hydrochloric or Sulfuric.
At my disposal is Hydrofluoric, Hydrochloric, Phosphoric, Nitric, Sulfuric, Chromic, and some ferric chloride
⇦ this on
eBay or
Amazon [affil links] although its expensive if I can only use it once.
If anybody has some experience it would be greatly appreciated.
Eric
plating shop - Grove Oklahoma
July 26, 2011
A. Sounds like reverse current etch in hydrochloric acid could do it but several things like amperage, time, voltage, temperature, concentration and final surface finish would have to be determined by trial and error first. You can use SS cathodes (your part becomes the anode). If geometry is irregular and complicated, cathodes must be designed with electric current distribution in mind.
G. Marrufo-Mexico
Monterrey, NL, Mexico
August 2, 2011
Inco 625 Parts Get White Spots on Some Surfaces after Chemical Etching
October 17, 2018Q. Hi All,
We perform chemical etching on Inco 625 part by using a mixture solution of HNO3 + HCL + FeCL. After finish the etching process, some of the parts we can observe there was some small shiny white patches on certain area of the part. Before run the actual part, we perform stock loss test on coupon to determine the etching time to remove material based on our customer requirement. We don't observe any of this defect on the test coupon. What could go wrong? Is this defect related to part surface before etching or related to the etching process?
Inco 625 test coupon for stock loss test. Coupon looks good after etching
Small shiny white patches on certain areas of part surface
Special Process Engineer - Bayan Lepas, Malaysia
Schantz Reagent + HCl for Surface Preparation
by Seenivasan, Manonmani k, periyasamy s
on AbeBooks
or Amazon
(affil links)
Q. Schantz reagent is sometimes used to etch stainless or nickel superalloy materials as a preparatory step for fluorescent penetrant inspection(FPI). I have seen two variants of the mixtures called out for the same base alloy (say Inconel 625, 718 or Hastelloy X), depending on who is calling out the mixture: one variant uses the Shantz reagent straight up, and the other requires a 1:1 mixture Schantz with hydrochloric acid. The basic formula of the reagent (see below) has some HCl in it already. Why would you add additional HCl in some cases? Also, when Shantz reagent is mixed with HCl its working life is 15 minutes. Does the HCl make the mixture very active and have a reaction that exhausts itself somehow?
The mixture reagent is:
(from report DOT/FAA/AR-03/73; Appendix D)
45.4 grams FeCl3 solid (1/10 lb.)
18 ml HCl
15 ml H2SO4
50 ml HNO3
75 ml C2H4O2 (acetic acid )
75 ml H2O
- Mentor, Ohio USA
Q, A, or Comment on THIS thread -or- Start a NEW Thread