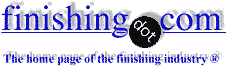
-----
Preparation for brush nickel plating over damaged EN plating
2005
Dear Reader,
We have been experimenting with nickel brush plating over damaged EN plating. Lets say the existing EN plating has been damaged with a tool thus exposing the substrate (Si-iron). The damage may only be as small as a .030" scratch or pit. What we do is the following:
Inspect the damage
Lightly scotchbrite or sand any sharp edges off the damage while very carefully trying not to remove plating in the surrounding area
Clean with IPA and cotton swab for 3 minutes
Activate with and acid activator (water, sodium chloride, hydrochloric acid) at forward polarity because the EN will turn black otherwise. 10-15 seconds time
Immediately plate with nickel acid (no rinse in between) for 2 minutes
Rinse with water
This process works. I would like to try Ammonium Hydroxide to clean the surface as the IPA doesn't seem to work effectively. I'd rather not add an electroclean step as I would then have three separate anodes set up for the process. This can become to tedious of an operation.
Does anyone have any suggestions or comments on pre-clean, or on this process?
Thank you in advance
Engineering - Wallingford, Connecticut
I would not recommend to use ammonia. Instead, you may find it useful to add a final cleaning step with liquid detergent and rinse after the isopropyl. This will further sweep minor contaminants left by the alcohol that acid activation cannot tolerate. But most important is to consult your brush plating supplier.
Guillermo MarrufoMonterrey, NL, Mexico
2005
2005
I am rather amazed that any call out for EN would allow touch up with a plated nickel.
You do not mention a strike. En is not easy to activate and most plated nickel will have problems without a Woods nickel strike. What kind of adhesion testing are you doing?
More anodes does add a bit to the process, but I would strongly stress using the procedure developed by your brush chemical manufacturer for optimum results. I have done brush plating that used
5 different anodes. It does require some planning and it helps to have more than one set of jacks.
- Navarre, Florida
James, I'm utilizing a tape test to check for adhesion. However, I don't always get consistent results. The plating almost always sticks to the exposed substrate (Si-iron), but not to the EN nickel that surrounds the damaged plating. Is nickel plating repair work something that is not common? I am following the procedure set by the manufacturer of the brush plating chemicals. Any advice or suggestions would be greatly appreciated.
Thank you.
Engineering - Wallingford
2005
Actually repair of damaged nickel coatings is a standard brush plating application. Many parts that nickel plated either bylytic or electroless means are then incorporated into larger or more complex components that could not tolerate to be stripped and replated.
During the activation process you will need to concentrate on the surrounding nickel coating to insure proper adhesion of the brush nickel coating. I am not familiar with the activation solution you are using but I would check with your supplier. Using an acid nickel solution that is specifically designed to plate over the dissimilar metals in the repair area is also important.
- Valencia, California
2005
Q, A, or Comment on THIS thread -or- Start a NEW Thread