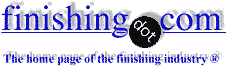
-----
Conservator has questions on Bs 5493 repairs
2005
Q. Hello,
My name is Allan Walker, I am a metal conservator for English Heritage and National Trust, etc.
I work on many historically important objects such as gates and railings in an outdoor situation from the 18th & 19th century.
When repairs have been made to the iron gates or railings the preparation for cleaning is blasting and then zinc spraying, all to BS 5493. If we are replacing missing parts then we use mild steel so that the repair is "an honest repair", one that can be recognized in the future as a 20th - 21st century repair.
Wrought iron tends to last longer than steel in an outdoor situation, so that is why we look to prepare and coat to BS 5493.
At last my question: Because BS 5493 is a 20th century invention I have had difficulty in finding out what the repeated use will be for historical objects. I need to know if, although slowing down the corrosion process we might be causing more damage to the surface by repeated bead, sand or grit blasting?.
How long would it be before a second blasting and coating to BS 5493 in an inland outdoor UK situation would be needed.
Any help would be very well received. ALLAN
metal conservator - uk
A. You might know already, but BS 5493 is 140 pages long, but trust me is a good read. No really, not Jane Austen but does contain a huge amount of useful information on the factors governing choices of prevention systems, etc.
That being said, could you measure the before & after blasting dimensions to give you an idea of amount of removed material?
How long before a repeat treatment would be needed would depend on a number of factors; the quality of the previous treatment, environment considerations - degree of exposure etc, type & thickness of spray coat - if zinc then usually 100 microns, whether sealed or unsealed, and more.
On balance though, I would guess that as long as not too much material is being removed by the pre-treatment, then you are not likely to be causing an increased rate of deterioration, and a (very) ball-park figure for duration would be in the order of 10 years; you would certainly expect to get that life out of a 100 micron galvanized coat in a non-polluted inland UK location.
Regards
Ship Repair - Plymouth, UK
2005
A. WD-40 ⇦ on eBay or Amazon [affil links] worked really well for me.
Michael Sweeney- Cramlington, Northumberland UK
November 19, 2017
Q, A, or Comment on THIS thread -or- Start a NEW Thread