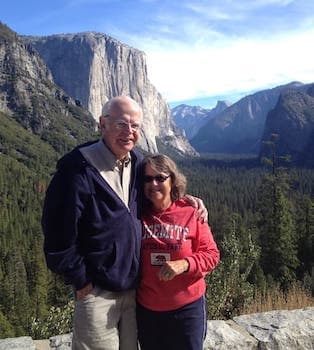
Curated with aloha by
Ted Mooney, P.E. RET
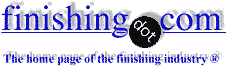
The authoritative public forum
for Metal Finishing 1989-2025
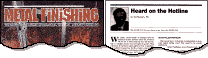
-----
Zinc plating rusts in shipment by sea
< Prev. page (You're on the last page of the thread)
Q. Why rust came in zinc plated parts? After plating process parts are packed in polythene. After some days, bright passivated parts became rusty? Why sir? Please give me solutions for precautions.
deb swainmetal finishers - delhi, India
January 7, 2015
Hi Deb. We appended your question to an earlier thread on the same subject to give you some hints about possible causes, and to suggest the type of data you would need to provide for readers to be able to help you. Good luck.
Regards,
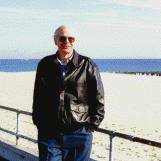
Ted Mooney, P.E.
Striving to live Aloha
finishing.com - Pine Beach, New Jersey
January 2015
A. If you plate enough zinc, say .0002", there will be no rust.
If you don't know how thick your zinc is, then all bets are off.
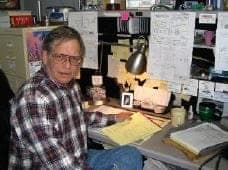
Jeffrey Holmes, CEF
Spartanburg, South Carolina
January 9, 2015
A. The red rusting is the result of low coating thickness and poor handling during shipment through ship.
A white rusting is the result of poor passivation film and that can be improved by applying top coat sealant after passivation.
engineering and trading - Abohar, Punjab, India
January 10, 2015
Q. Hello sir,
I need one clarification from you: whether it is possible before formation of white rust any chances of formation of red rust. And which criteria depends for white rust and red rust? Whether white rust depends on passivation and red rust depends on coating?
personal - rothak Haryana India
November 29, 2016
A. Hi Praveen. Rusting of the steel substrate is called red rust. Corrosion of the zinc plating is called white rust. The chromate conversion coating (passivation) deters white rust. Yes, red rust before white rust is certainly possible depending on the part (blind holes, spot-welded seams, or other areas of little or no plating). But you'll probably get better, more accurate, more enthusiastic, more helpful responses if you take the time to carefully provide the details of your own particular situation rather than keeping it vague and abstract.
Regards,
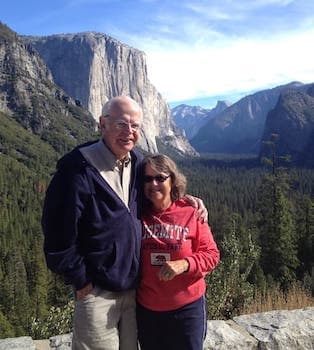
Ted Mooney, P.E. RET
Striving to live Aloha
finishing.com - Pine Beach, New Jersey
November 2016
Q. Dear sir,
We are currently working in an automobile sector and manufacturing vehicles which are used in very humid areas. We are facing rust issues on our connectors, e.g., HYDRAULIC FEMALE-FEMALE STRAIGHT REDUCER, A18 TO A15, M26X1.5 TO M22X1.5. As per the drawing requirement we want them to be electro galvanised on steel as per ISO 8434-1/DIN 2353/DIN 3016 [fastening clamps] standards.
Now are facing rust on these parts. Other than not using the correct coating what can be the other potential causes of rust on these parts?
Thanks
automotive - Abu Dhabi, UAE
January 16, 2018
A. Hi Mustafa. We appended your inquiry to earlier very similar inquiries so you can read of many contributing factors towards rusting. But you have not told us what your plating spec is, what salt spray hours you achieve, the actual rusting situation, etc., so all we can do is fire back a round of buckshot :-)
Regards,
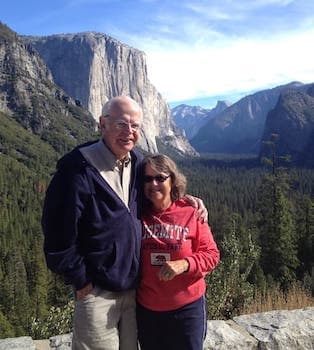
Ted Mooney, P.E. RET
Striving to live Aloha
finishing.com - Pine Beach, New Jersey
January 2018
Q. Hello,
I wanted to inquire what should be the testing conditions for a salt spray test (hours) for both white and red rust for hydraulic straight stud couplings.
The couplings are used in automobiles which will be subject to humid conditions. Material used is steel which is electro galvanized.
Thanks and regards,
Mustafa
- Abu Dhabi
January 21, 2018
A. Hi Mustafa. It seems to me that this project is being approached backwards. Salt spray testing is a QA test to make sure your plating quality is not deteriorating; it is a poor indicator of real life, especially in the case of zinc plating which corrodes very differently in a salt spray cabinet than in real life. Trial & error on zinc plating, to no particular spec, until you reach some arbitrary salt spray hours, probably isn't the best approach.
If the automobile company has issued no specs for this component, then you have to choose a specification for yourself. I think most auto companies would rather see 13 microns of a zinc alloy like zinc-iron, zinc-cobalt, zinc-nickel, or tin-zinc than anything else. Then you can search this site or other sources for good salt spray hours to use for white and red rust for QA of such coatings. Best of luck.
Regards,
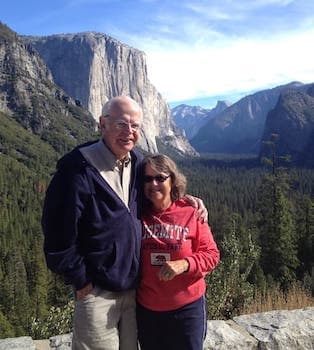
Ted Mooney, P.E. RET
Striving to live Aloha
finishing.com - Pine Beach, New Jersey
January 2018
![]() |
Zinc Nickel Plated Parts Have Red Rust on top of the platingQ. Hello. We are currently experiencing a corrosion issue on an automotive door component. Plating is (min) 6 microns of Zn-Ni plus an organic topcoat. In our case, the organic topcoat is a (anywhere from 1-10 micron) layer of an organic oil/lube. Analysis of the plating shows minimum Zn-Ni thickness is OK and Ni content is OK. - Detroit, Michigan, USA August 7, 2019 Q. We have some industrial parts that we outsource plating. The parts are 12L14 Steel and supposed to be zinc plated & yellow chromate per ASTM B633, SC-3, TYPE II. Engineer - Missouri December 19, 2019 A. Hi Mete. As you can see from this thread (and a dozen like it if you patiently search the site), there can be all sorts of reasons why the parts rusted: from poor cleaning to poor plating to poor post treatment to poor drying to poor packaging to bad storage conditions, to unrealistic expectations, and more. But the first step is that parts must comply with their specifications. If they are supposed to be SC-3 / 13 µM / 'severe exposure', and instead they are actually SC-2 / 8 µm / 'moderate exposure', that is an immediate problem that you must fix. If the plating shop talked you into accepting SC-2, it might be acceptable but only if you immediately changed the specification. Regards, ![]() Ted Mooney, P.E. RET Striving to live Aloha finishing.com - Pine Beach, New Jersey December 2019 A. 12L14 steel is a leaded steel. It requires special cleaning techniques. Specifically any pickle must be sulphate free. ![]() Tom Rochester CTO - Jackson, Michigan, USA Plating Systems & Technologies, Inc. ![]() ![]() December 19, 2019 ---- |
Zinc plated components got rusty during transition from India to Canada by sea
Q. we have been shipping electrical steel components since 1986. First time in the history, 13 nos full load 40' containers got rejected as boxes got wet during transition & zinc plated components got rusty. So what went wrong?
Arun kumar katiyar- alwar, India
May 9, 2020
A. Hi Arun. As you can see from the topic we appended your inquiry to, there are a half dozen or more possible causes: insufficient plating thickness, poor chromating practice, parts not fully dry, poor packaging materials, lack of desiccants & VCIs in the packaging, unreasonable environmental conditions during shipment, etc.
But you said you've had no problem in decades, but this time the boxes got wet, so that certainly sounds like the problem. Please get back to us with comments or additional details.
Regards,
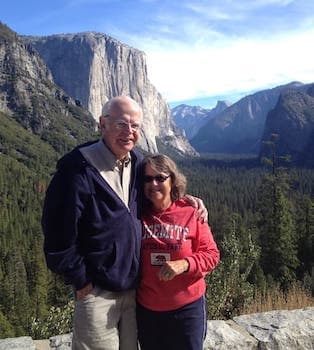
Ted Mooney, P.E. RET
Striving to live Aloha
finishing.com - Pine Beach, New Jersey
May 2020
Q, A, or Comment on THIS thread -or- Start a NEW Thread