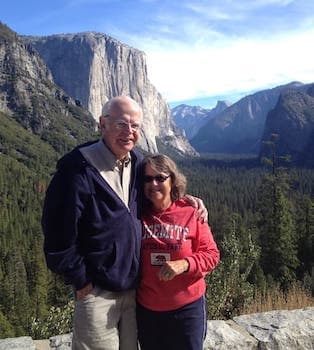
Curated with aloha by
Ted Mooney, P.E. RET
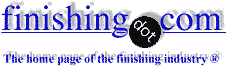
The authoritative public forum
for Metal Finishing 1989-2025
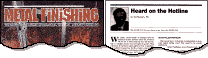
-----
Pulse Plating of Chrome
Q. I am searching for information about pulse plating in a chrome solution. I am doing work with a HEEF chrome solution. Is anyone interested to help me with information on this? Regards,
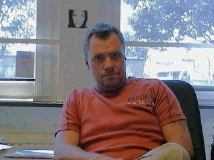
Anders Sundman
4th Generation Surface Engineering
Consultant - Arvika,
Sweden
1999
A. I am not sure that such a process exists at all. You cannot interrupt the current for chrome plating (hexavalent chrome) as deposit will turn grey.That is why you cannot plate chrome in barrel. Pulse plating is mainly used for acidic copper, silver, gold etc.


Sara Michaeli
Tel-Aviv-Yafo, Israel
1999
A. Chrome can be pulse plated, but it requires a very specific "window". Also it significantly changes the plate. Sulfamate nickel is more forgiving or amenable to pulse plating, but here again it changes the properties of the resulting plate. Unless you absolutely need the specific plate for these two metals, I feel that you will be far better off using a considerably less expensive straight DC. A fact of life is that any one who has developed a window for a specific result on these two baths, is not very prone to share that information. The folks that sell pulse equipment in the past did not provide specific windows for these two baths and windows provided were only a starting point. The best window for your specific application had to be developed. If you did not have a rather complete lab, it was impossible or very very expensive of blind dumb lucky.
James Watts- Navarre, Florida
1999
Q. Dear Sir,
I wish to know what parameter actually effects the coating behaviour when using Pulse plating for Hard Chrome plating. I.e., duty cycle, frequency, etc., and what is the most favourable setting for hard chrome plating using pulse plating apart from amperes which depend upon the size and shape of the part.
Thanking you in advance and looking forward to your earliest reply.
With best wishes and regards
- Pakistan
2005
A. Hi Tayyab. You might try to find a copy of "Theory and Practice of Pulse Plating" by Jean-Claude Puippe & Frank Leaman.
Still, I haven't yet heard of generic or universal answers to the question of good pulse plating parameters. Pulse plating adds yet another variable to a process which is already replete with a multitude of only partially tamed variables, and I haven't yet seen an article that says anything like: "For chrome plating you will find a duration of x and duty cycle of y useful". But do remember that chrome plating doesn't tolerate current breaks or reverse currents well without going passive.
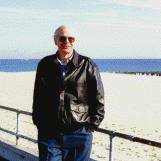
Ted Mooney, P.E.
Striving to live Aloha
finishing.com - Pine Beach, New Jersey
2005
A. As far as I know, there is no universal condition for pulse plating of hard chromium. There is an increasing amount of work being done with pulse plating and chromium, but the major interests is in trivalent chromium; however, some work is being done with hexavalent. What is clear, especially with hexavalent, is that controlled charge modulation is essential. Furthermore, it must be remembered that hexavalent chromium is very unhappy having the current supply turned off - it will passivate and subsequent layers delaminate. I would therefore suggest that the cathodic current is pulsed, but whilst continuously keeping it significantly polarised in the negative. There are reports that crack-free hard chromium can be put down by pulse plating, so there is clearly work being done with the idea. The optimum conditions will depend on the type of bath used and its conditions. I suggest you may want to do some fundamental work and find the optimum conditions for your system.
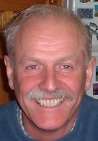
Trevor Crichton
R&D practical scientist
Chesham, Bucks, UK
2005
Q. Hi Members,
I am doing research on chrome plating with trivalent chromium for engineering applications.
Is it possible to use plating with pulse current?
University of Wolverhampton - UK
2006
A. Hi, Enam. At this point I believe it is not considered commercially feasible to do trivalent hard chrome plating. So, is it possible to do trivalent hard chrome plating while adding pulse plating to the mix? Maybe you will find pulse plating to be the answer to trivalent hard chrome plating. Good luck.
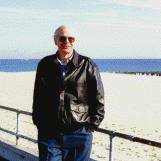
Ted Mooney, P.E.
Striving to live Aloha
finishing.com - Pine Beach, New Jersey
2006
Q. Hi,
I'm searching for a company in USA who is using pulse plating in the hard chrome process. I'd like to come in contact with them.
Thanks for helping.
Regards,
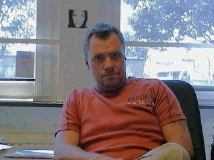
Anders Sundman
4th Generation Surface Engineering
Consultant - Arvika,
Sweden
June 23, 2008
I have done a complete pulse plating deposit with hard chromium deposit with excellent adhesion and corrosion testing in salt cabinet for over 600 hours without corrosion. The chromium deposit looks like regular hard chrome but no cracks to the bottom, it's intact. Here are photos of it if anyone would like to see.
The pictures show the deposit thickness inside the chrome as a sandwich.
Best regards
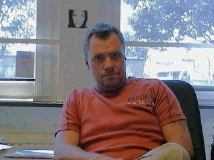
Anders Sundman
4th Generation Surface Engineering
Consultant - Arvika,
Sweden
A. In hard chrome use duty cycle 95% frequency 800 Hz. And reduce the concentration of catalyst less 1/3 or nothing.
Jonas ZAZULLArectifier factory - São Paulo - SP - Brazil
March 12, 2013
Anode for pulse reverse plating of chromium
Q. While trying to plate chromium on steel using pulse-reverse current, I found several times that deposition was not occurring and that even more, Fe from steel was getting into solution. I'm using a lead anode. I did some research and found out that one of the problems was the relation of Qa/Qc I was using, which would explain the no deposition. However, I was wondering, wether during the current reversal period if PbO2 could be reducing to PbSO4. I haven't been able to check the bath composition to analyze if there is Pb2+ or if PbSO4 deposition could be on the cathode.
Is lead the best anode for chromium pulse reverse deposition process?
The papers I have found relating this process use an anode of platinized titanium, lead or doesn't mention. What would you recommend that isn't as expensive as platinum?
- Buenos Aires, Argentina
October 31, 2016
A. Hi Maria,
Just for starters, because potential causes are multiple, have you checked the chromic acid concentration with a Baumé stick or another method and what are your readings? Low power could be an issue if concentration is correct.
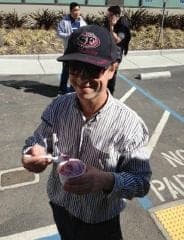
Blake Kneedler
Feather Hollow Eng. - Stockton, California
January 1, 2017
![]() |
A. "Pulse reverse" means, to me, that for part of the cycle, the part is made the anode. It's not surprising that it is attacked. ![]() Dave Wichern Consultant - The Bronx, New York January 4, 2017
- Buenos Aires January 5, 2017 |
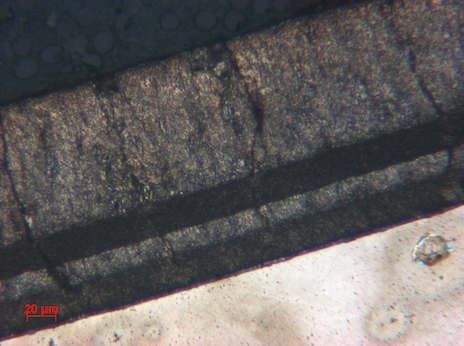
A. Hi,
I use normal anodes when I pulse plate chrome. But it is important to start with normal plating first -- that means the part should be the cathode.
Regards,
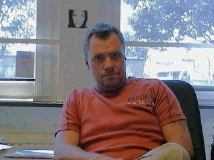
Anders Sundman
4th Generation Surface Engineering
Consultant - Arvika,
Sweden
January 26, 2017
Q, A, or Comment on THIS thread -or- Start a NEW Thread