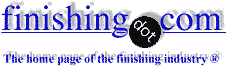
-----
Painting of Mn-Phosphated Surfaces
2005
Our company is procuring valves for water and steam piping of a boiler. Fluid temperatures are up to 300 °C.
For small forged valves (carbon steel, ASTM A105), the valve supplier proposes to use Mn-phosphating with oiling (Chemtech DW901,
100% concentration, 5 minutes dipping in bath).
Our questions:
1) Will oil provide long-term protection to the phosphated surface under such conditions? Or, will the oil get vapourised at these temperatures?
2) Can we paint the as-phosphated surface with ethyl zinc-silicate type of primers?
3) The phosphated surface will rinsed with cold water. "Dewatering" will be done in oil bath with NOXT RUST 950 oil. Finally, rust preventive oil rinse is carried out in Chemtech DW 901 oil bath. At what stage of the process can we apply the primer? Do we need to prepare the phosphated surface in any way prior to primer painting?
- Mumbai, India
2005
You have mentioned about Dewatering oil. These oils are volatile petroleum based oil, which will remove the water. After this you are using a rust preventive oil, which is again nothing but a (DW means) De watering oil.
Both these oils get evaporated at around 90°C. But DW 901 has about 15 to 20% non volatile part, which will still be available after evaporation. But this will not be sufficient to give the required properties.
Best method to asses the characteristic of the oil is
Take a watch glass ( Dish ). Pour 5 ml of fresh oil. weigh the oil with dish. Then heat it to your operating temperature ( You have mentioned 300°C). Allow it for 10 minutes. After 10 mins, take off the heat, cool and weigh it again. You will come to know the retention of oil after exposing to this temperature.
You have also mentioned about what preparations required for painting. If you are painting after phosphating, you should not dip it in oil. You need to paint the component within four to six hours immediately after phosphating. If it extends then you may have problems of patches of rust.
Alternately you may apply a rust preventive oil, and remove the oil before the painting operation, which is a costlier affair you won't like it.
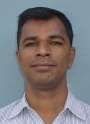
V. G. Rajendran
- Trichy, Tamilnadu, India
Q, A, or Comment on THIS thread -or- Start a NEW Thread