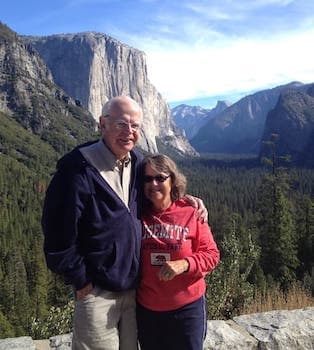
Curated with aloha by
Ted Mooney, P.E. RET
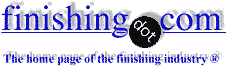
The authoritative public forum
for Metal Finishing 1989-2025
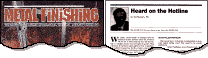
Thread 352/65
Poor adhesion of Tin Plating on copper strip
Q. We are in the metal stamping area trying to develop reel-to-reel plating. Our requirement is pure tin plating on copper strip in reel form. For some reason the plating tends to form blisters on application of heat at the users' end. Plating is not our specialization and our plater is on the verge of giving up. Can someone give a lead on what's going wrong?
Ramachandranmetal stamping Industry - Indonesia
2005
publicly reply to Ramachandran
A. It could be a cleaning problem, but without knowing what process you are using, no-one can tell you what is wrong and how to solve it.
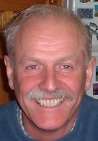
Trevor Crichton
R&D practical scientist
Chesham, Bucks, UK
2005
publicly reply to Trevor Crichton
A. You did not say what kind of tin or what kind of copper. If it is Tellurium or Beryllium bearing copper, then flash it with Acid sulphate copper or acid fluoborate copper before the tin plating. Then enter the tin bath "hot" (make electrical connection so that current flows immediately upon entry into the tank.) Do not use cyanide copper as Te and Be form insolubles with cyanide.
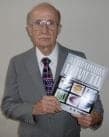
Robert H Probert
Robert H Probert Technical Services

Garner, North Carolina
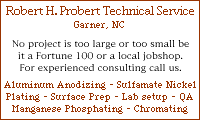
2005
publicly reply to Robert H Probert
A. Since you have not provided details, I may assume that the problem is similar to what I faced for RoHS compatible reflow soldering. The melting point of Sn is 232 °C and reflow temperature is 250 °C (for RoHS). Pure tin plating tends to decolourise or form defects like blisters if kept at reflow temperature for longer durations.
Jackson Saludes- Bangalore, India
2005
publicly reply to Jackson Saludes
Q. I encountered blisters on Sn plating after post plate bake. Suspect iron contamination from stainless steel support plate in the predip solution. Could it be possible, and what is the mechanism?
Tan YanPlating shop employee - Melaka, Malaysia
November 18, 2010
publicly reply to Tan Yan
A. The primary cause of blisters is the part is not activated properly. Get your plating chemical vendors tech service involved. If this is a home brew, good luck.
James Watts- Navarre, Florida
November 18, 2010
publicly reply to James Watts
Matte Tin on Beryllium Copper raw material chipping off at corner
November 2, 2015Q. I'm William Chan from Malaysia, this is the first time I'm posting on this forum. I have learnt so much from the contributors and subject matter expert like you! I'm a supplier quality engineer where I monitor my plating sub-contractors that are doing sheet metal plating. The problem I faced now is my sub-contractor is not able to solve the matte tin problem. The raw material of my part is Beryllium Copper C17200 alloy 25, TD02 (without heat treatment). After the sheet metal forming of Beryllium Copper material, it will go through matte tin process by wire jigging them. I have close to 60% reject rate where the matte tin is chipping off at the edges where I can see the raw material Bronze color by naked eye. The chipping only occurs at the edges but not at other places or flat surfaces.
I tried to use a normal double-sided adhesive tape to perform tape test but the adhesion is good where I can't see any peel off. My parts are shipped to me where those parts are arranged in a tray side by side. I'm wondering could it be due to the "collision" or "rubbing" between two matte tin parts during transportation where the edge or corner collided with each other that have caused plating chipped off? Could it be the plating peel off during the rubbing between 2 parts at the edges when the plating is still wet and not completely dry?
I do not have the chemical composition used at plating bath as my supplier does not share that info to me. Please help to share your opinion or post more questions to me.
Thank you!
- Singapore
publicly reply to Chan William
![]() |
A. What is the preparation cycle, what kind of tin solution? Try a plain copper flash with an acid copper sulphate ⇦ this on eBay or Amazon [affil links] solution, then plate on the tin. ![]() Robert H Probert Robert H Probert Technical Services ![]() Garner, North Carolina ![]() November 2, 2015 publicly reply to Robert H Probert A. One thing that might help is to put a radius or champers on the edge that is chipping. If it is from banging together it will help. Also, it will reduce the high current density of that area during plating which will possibly lower the brittleness of that area. James Watts- Navarre, Florida November 3, 2015 publicly reply to James Watts A. Your photos do not show mechanical damage. What they do show is poor adhesion of the tin plate. Something is wrong in the cleaning, pickling or rinsing in the process. ![]() Jeffrey Holmes, CEF Spartanburg, South Carolina November 4, 2015 publicly reply to Jeffrey Holmes, CEF |
How to clean corroded copper before tin plating
Q. I am working as inward quality engineer. I have received a copper strip shipment with corrosion. Could you tell us how to remove the corrosion in copper strip? This copper strip going to be tin plated around 5 micron in our plant.
Also we have electroplating plant.
Thanks
abdul
from KSA
- Riyadh, SAUDI ARABIA
April 6, 2017
publicly reply to ABDUL rahuman
A. Hi Abdul. Sulfuric acid may remove the corrosion; if not, then hydrochloric acid probably will. If the corrosion is deep enough to have pits, it may not be possible to repair it without mechanical treatment (sanding / vibratory finishing) though. But as I'm sure you know, there can be a lot involved in getting a copper substrate properly pretreated for tin plating. Can you tell us what sequence you normally perform, and why you think that sequence will be inadequate for this shipment? Thanks.
Regards,
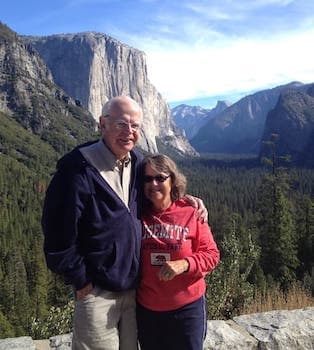
Ted Mooney, P.E. RET
Striving to live Aloha
finishing.com - Pine Beach, New Jersey
April 2017
publicly reply to Ted Mooney
A. Hi Abdul,
Further to Ted's advice, you may also apply copper descaler (e.g. persulphate or hydrogen peroxide base) to mildly etch copper strip for several microinches to remove oxidation/soil/residue as well as create a micro roughened copper surface to enhance tin deposit adhesion/appearance.
Regards,
David
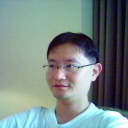
David Shiu
- Singapore
April 17, 2017
publicly reply to David Shiu

this text gets replaced with bannerText
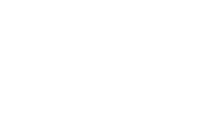
Q, A, or Comment on THIS thread -or- Start a NEW Thread