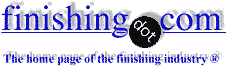
-----
Powder Coating Porosity Related to Metal Pretreatment
2005
Q. We utilize a five stage washer (1.clean, 2.rinse, 3.phosphate, 4.rinse, 5.seal) for metal pretreatment prior to powder coating. We have been having problems with tiny bubbles and porosity appearing in the cured coatings due to something related to our pretreatment. We primarily coat HRPO material and painting these substrates without pretreating does not result in the distinct bubbling. The areas on the parts where the bubbles first appeared were on rough areas created by 80 grit alumina-zirconia disk abrasives and areas around welds. Most recently the bubbling is occasionally covering the entire surface of the substrates.
We have had two SEM and EDX analyses performed on the defects by our chemical supplier and the root cause of the defects were not determined in either. The defects are more pronounced in our black and grey powders than in our chromatics. I have determined that our pretreatment is the culprit, what I would like to know is what in our pretreatment process is causing the defects. The parts are water break free and show a clean surface with the white cloth test. Our washer specifications are as follows,
Stage 1 (125 F, 20 psig for 1 min)
KOH base multi-metal phosphated Alkaline cleaner, (5.5%, pH=11.8, FA=30 mL TA=62 ml 1N^0.1N HCl)
Stage 2 (15 psig for 30 sec)
Softened city water rinse, (T=90 F, 2400 uS Conductivity, pH=8.7)
Incoming water is 1400-1800 uS, pH=7.3-8.2
cascading to Stage 1 for makeup
Stage 3 (125 F, 10 psig for 1 min)
Cleaner/Coater, organic accelerated phosphate with a borate rust inhibitor to prevent flash rusting, (4%, pH=5.5 TA=7.2 mL 1N^0.1N NaOH)
Stage 4 (6 psig for 30 sec)
Softened city water rinse, (T=85 F, 1900 uS Conductivity, pH=7.9)
cascading to Stage 3 for makeup
Stage 5 (8 psig for 30 sec)
DIP Seal rinse, fluorozirconic acid, (T=80 F, 3-4% product in city water, pH=4-4.5)
If any other information would be helpful in determining the cause of the defects I will gladly supply it. (geochem on the water,products being used etc.)
Any help would be greatly appreciated.
Thank You,
- West Fargo, North Dakota, USA
A. Hi Brad,
Good job on giving this much detail about your pretreatment system. It makes it easier to solve the problem.
What do you mean by bubbling of the powder coating? Do you see areas of tiny pitting in the coating?
You say that the pretreatment is the culprit. How did you arrive at that conclusion? Have you run standard test panels through the system? If you got the same result, then I would agree with your conclusion. But you say the problem is most prominent in the welded areas, which in parts like yours, are notoriously difficult to get completely clean. Did you perform a water-break test to determine cleanliness of the surface?
I would also verify that the powder is being cured properly. I have encountered many customers who were not aware that the temperature of their cure oven was too low and were not properly curing the coating.
- Naperville, Illinois
2005
A. When did the problem start, or has it been their since the wash line was put into use? I know this answer doesn't follow with some of the description of your problem, like the fact that you don't have the problem if you don't pretreat, but our weld engineer was able to solve a problem that sounds almost identical to yours. He found that the welders were running their gas at different pressures. It doesn't do much for process control when each welder would change the settings as he pleased. The welders that ran the pressure low caused this pinholeing at the welds in varying degrees. I still don't know if something about the gas(or lack of) was reacting to something in the wash system, and that was what was causing the problem, all we could determine is that when the process was fixed(the gas properly set and remaining the same at all the weld stations), the problem virtually went away. Every once in a while I'll see a little bit of the problem and the first thing I think is that a welder was running their gas low again.
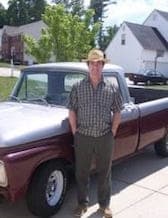
Sheldon Taylor
supply chain electronics
Wake Forest, North Carolina
2005
Q. I have one correction to make. The concentration of the titrating solutions were 0.1N and the sample being titrated was 10 mL. As far as cure goes, I ran numerous temperature profiles on the oven with probes on bare parts that showed adequate cure. The bubbles sometimes appear in streaks which points to me a rinse issue, but what is causing the bubbles? I did mention that the parts are leaving the washer, water break free and the white cloth test proves cleanliness. If we increase our alkaline cleaner concentration, the bubbles get worse. If the part is just alkaline cleaned (no rinse), dried, and painted the bubbles show up. Like I was saying though, an uncleaned, untreated shop steel panel will not have the bubbling and porosity. Strange. Hopefully when we put in a reverse osmosis system in a couple of weeks the problem will disappear. Thank you for replying.
P.S. The weld gas thing is interesting and I will put that on my black list.
- West Fargo, North Dakota, USA
2005
A. I think you have way too much chemical going on. What's your phosphate coating weight? I've never run the phosphate over 2.5% or the cleaner over 3%, even with heavy soils. Besides, all of the cleaning should be taking place in your 1st stage, so you don't need the cleaner in the phosphate. If your chemicals are running too high they can ride the conveyor and then drip onto the parts between the washer and dry-off oven causing the parts to look like you have a rinse problem.
An R/O isn't going to help because you already know the problem is tied to the first stage. If the problem was a complete unknown and you were going to try and fix it with the final stage, D/I would be the better way to go because D/I water is aggressive, and R/O water is just filtered.
Try running your chemical concentrations lower and maybe change your phosphate out for something that doesn't have a cleaner in it. Looks like the temp could be a little high too, try 120 F or less in the phosphate(keep the cleaner 125 F).
Since you have a cleaner in your phosphate have you tried to run samples through just the last 3 stages to see what they look like? Might come up with some interesting results.
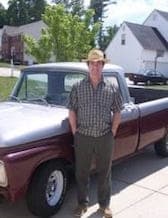
Sheldon Taylor
supply chain electronics
Wake Forest, North Carolina
2005
A. If your water break test & white cloth test are ok then I suggest that you check if your compressed air line is free from oil/water contamination. If need be install a dryer just before point of delivery. I faced a similar problem of heavy pitting esp. near the weld.
Let me know what happens.
- Mumbai, India
2005
A. In general, it would seem that your pretreatment is satisfactory, however, I agree that your chemical concentration level appears to be high.
Too little chemical makeup and your substrate will not be properly cleansed and too much will be a waste of chemical and it will be much more difficult for the rinse to achieve a clean surface for the iron phosphate to conduct its business.
The problem you said occurred where you are grinding with 80 grit. My question would be, why are you grinding this surface and with 80 grit? Is the HRPO leaving flaking metal, embrittled metal or scale coming from poor quality metal? If this is true, the grinding may not be adequately cleaning the surface and sandblasting may be required. I say this because you stated it shows up where you were grinding. If any of the scale remains on the surface and you powder over it, the air will be trapped under it and try to work its way through the powder causing defects similar to what your describing. Maybe try blasting one and see what occurs.
As far as the difference between R/O and DI water is concerned, DI water is generally only more aggressive than R/O water when it is in a more pure state than R/O. DI water that has been run through cation and anion exchangers work more efficiently than anion exchangers do. This means DI water contains a small percentage of excess anions and, therefor, can be slightly acidic which give the term aggressive. Powdercoat in general likes a slightly acidic surface and so DI works well with powder.
![]() Bob Utech Benson, Minnesota |
![]() Ed. note: Bob is the author of: "High Performance powder Coating" on eBay or AbeBooks or Amazon [affil links] |
A. Seems to me that your rinses are very dirty.
We stop pretreatment if our final rinse gets over 100uS/cm conductivity, but you are operating at 20 times that.
So without a clean rinse, your work must be covered in all manner of unrinsed stuff?
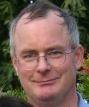
Geoff Crowley
Crithwood Ltd.
Westfield, Scotland, UK
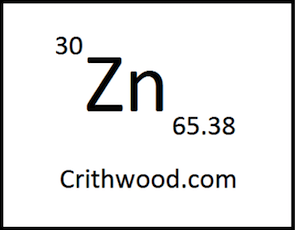
March 30, 2011
Q. Do you have pictures available concerning this matter? It sounds very similar to a situation we have on CRS enclosures, but pitting appears along formed edges as well as weld areas.
Kara Snider- Spokane, Washington USA
March 28, 2011
March 28, 2011
Hi, Kara. Please e-mail any photos to if you would like them included here. Brad's situation remains on line because of its continuing usefulness to other readers, but he is unlikely to be monitoring this old thread.
Regards,
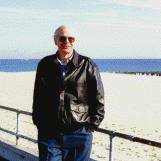
Ted Mooney, P.E.
Striving to live Aloha
finishing.com - Pine Beach, New Jersey
March 29, 2011
Q. I don't have pictures of the pitting issue along formed edges, however those pictures show the issue around welds and punched holes.
As I mentioned, this issue appears on painted CRS and a few aluminum painted parts as well, though not as frequently. And because occurrence is so inconsistent, it really hard to pin-point the root cause.
I'd be happy to provide more information to assist in resolving this matter. Any input you can provide would be greatly appreciated.
Best regards -
Kara Snider- Spokane, Washington USA
----
Ed. note: Aww, and your nemesis looks so friendly, Kara :-)
March 29, 2011
A. This looks very much like a case of surplus anti-spatter from the weld process.
Take two identical components and wipe one thoroughly with MEK.
Run both through your system together and see what I expect to be a remarkable difference.
Hope this helps,
Regards,
Bill
Trainer - Salamander Bay, Australia
A. After seeing the photos, I would try putting a few drops of phenolphthalein ⇦ on eBay & Amazon [affil links] on the areas to see if your getting bleedout from the bracket. If there is oil or any alkalinity remaining on the surface, the phenolphthalein should turn it pinkish.
![]() Bob Utech Benson, Minnesota |
![]() Ed. note: Bob is the author of: "High Performance powder Coating" on eBay or AbeBooks or Amazon [affil links] |
A. I would go along with Williams analysis. The defect seems to indicate droplets are in a pattern of a sprayed on substance... in this case anti-spatter aerosol fluid.
Terry HicklingBirmingham, United Kingdom
March 30, 2011
Q. Bill and Terry - Thank you both for your replies. Our welder informed me anti-splatter is not used for TIG welding. Furthermore, this "pitting" appears where no welding occurs, as in the case of these pictures (around the half-shears, and plugged threads). And though I don't have pictures to illustrate, I have also seen it occur on formed corners of parts containing no weld at all, thus indicating this issue pertains to our wash line or paint process.
Bob - I'm not familiar with phenolphthalein
⇦ on
eBay &
Amazon [affil links]
. Should this chemical be applied on the surface of the painted part after "pitting" becomes apparent?
If you have any other ideas as to the cause, I'd appreciate that input as well.
Best regards - Kara
- Spokane, Washington, USA
April 4, 2011
A. Phenolphthalein is an indicator used in titrating pretreatment chemistries. Almost all chemical companies have this readily and you can purchase it at any of the online chemical distribution websites. Generally speaking, it will turn pinkish in color when it is placed on alkaline organics. Phenolphthalein alkalinity is present only when free carbon dioxide (CO2) is absent and therefore exists only when the pH exceeds 8.3.
Most alkaline residues are caused by poor rinsing after washing with an alkaline detergent, but sometimes they are caused by alkaline water supplies. The latter case can easily be verified by checking the pH of the raw water. If it is over 9, the cause may very well be the water.
Many organics (oils, cutting fluids, etcetera)and soils that are being cleaned off in the pretreatment system are alkaline. So, if you put a few drops of phenolphthalein
⇦ on
eBay &
Amazon [affil links]
on this area AFTER it has been washed and BEFORE it is painted, you might be able to see whether the wash is cleaning the substrate properly. No color should show if it has been cleaned properly. If it turns pink, there has been a reaction and there's still an alkaline substance on the part. This type of test is not science and should be merely used as a starting point in finding the problem but sometimes you get lucky.
![]() Bob Utech Benson, Minnesota |
![]() Ed. note: Bob is the author of: "High Performance powder Coating" on eBay or AbeBooks or Amazon [affil links] |
April 16, 2011
A. Well,
I can only state with certainty from observing the pictures that you have a problem with organic contaminants (oil, grease et al)
Your rinses are acting as contaminating bodies.
Perhaps they are carrying forward organic contaminants?
A reasonable fresh water rinse might be about 100 micro siemens .
An acceptable final rinse would be zero micro siemens resulting in a tested water run off of final rinse at about 25 or less.
So there is definitely a rinse problem.
An earlier reply suggested looking at your air supply quality.
That is also very valid.
I guess you have to investigate where the oil & or grease is entering your system.
There is no doubt that is the problem.
Hope this helps.
Regards,
Bill
Trainer - Salamander Bay, Australia
A. This problem is common to powdercoating and galvanizing, and in my opinion is what's sometimes called acid weep.
In both pictured cases you have an unwelded joint where one piece of metal overlaps the other, forming a small cavity.
This traps pretreatment chemical and is not easily rinsed.
The chemical boils out in curing oven, staining the work.
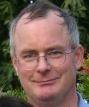
Geoff Crowley
Crithwood Ltd.
Westfield, Scotland, UK
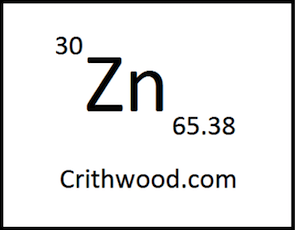
April 19, 2011
Powder coating pinholes: cast aluminum horses
October 1, 2014Q. I do restoration work on a lot of old items for a local museum. I am now restoring an old coin operated horse of the type found in front of stores for the little kids. The horse is cast aluminum. I just had the horse out for powder coating and when it was returned to me it had many, many small pits all over it.
The powder coater told me it was boil out from when it was heated to cure the coating. He told me they first sand blast the horse and then powder coated it. What can I do to correct this problem?
Ted Lohry- Oceanside, California U.S.A.
October 3, 2014
A. Boil out?
I think not!
It would be good to have a description of the objects condition before "restoration".
It would be also helpful to know exactly what the Coaters processes were.
I observe you are from Oceanside California.
I presume that means the object could have suffered from salt based corrosion?
I would like to know what the pre-treatment processes were undertaken before abrasive blasting (presumably garnet?).
If you could give a very detailed description of what actually happened during this (restoration) process it would be easier to advise you.
Best Regards,
Bill
Trainer - Newcastle, NSW Australia
A. There are two levels of pitting here, categorised by size.
The biggest are likely not caused by "outgassing", or "gassing" as its variously called, but are casting defects. (Its not possible to say this definitively just from a photo or two, but likely). These defects need to be filled with something that will withstand the powder curing temp (about 200 °C).
The smaller holes could be gassing, and there are multiple causes for this, the most common is actual moisture in micropits in the surface of the casting. Other causes include surface contamination (not necessarily visible), metallurgical inconsistency on the surface, moisture in the powder applied, and so on.
Similar issues occur with ferrous castings, and with hot dip galvanized steel.
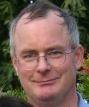
Geoff Crowley
Crithwood Ltd.
Westfield, Scotland, UK
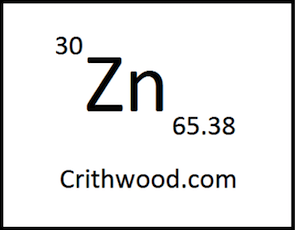
October 3, 2014
Q. When I received the horse for restoration it was in very poor condition. The steel frame was badly rusted beyond repair. I made a new frame. Most of the original paint was still intact with a couple of areas where the paint had peeled and there was corrosion on the aluminum. The powder coating company said that was not a problem as once it was blasted all the corrosion would be gone along with all the paint. As the photos show, the finished job was a total mess. The company has picked up the horse and will try to correct the problems. If they can not make it right, I asked that they blast all the powder coat off and return the horse to me with bare aluminum. I can use filler and primer to smooth the surface and spray it with an epoxy paint. They did say it was a gas blowout that happened when heated to cure the coating. They are going to try using a lower temperature this time around. I appreciate the responses and will post results when the horse is returned to me.
Ted Lohry [returning]- Oceanside, California U.S.A.
October 4, 2014
October 6, 2014
A. I would be very wary of a low temp powder solution.
Typically Powder requires a cure schedule of ~200 °C metal temperature for 10 minutes to achieve total cross -linking and thus cure.
Time & Temperature are flexible to a degree, i.e., (slightly ) lower temp for longer time but not very low Temperatures.
I suspect that the corrosion on the object has possibly been blasted into the relatively soft Al metal rather than off it.
My advice would be to blast it clean again then inspect and if necessary fill any voids then apply an epoxy primer and a two pack epoxy finish coat.
I would also ensure that any connection to Steel support mechanisms be insulated, e.g., Nylon fasteners.
I am a passionate advocate of Powder but sometimes there are better alternatives.
Hope this helps.
Regards,
Bill
Trainer - Newcastle, NSW Australia
October 7, 2014
Bill,
I am waiting for the return of the horse to see if the powder coater has it right this time. If not, I will paint it in the conventional way as stated. I'll post the results as soon as I have the horse again.
Thank you everyone for the input.
- Oceanside, California U.S.A.
So we'll temporarily bid adieu to you and the horse you rode in on :-)
Thanks for the interesting question!
Regards,
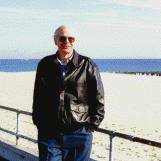
Ted Mooney, P.E.
Striving to live Aloha
finishing.com - Pine Beach, New Jersey
October 2014
Q. We powder coat Stainless, Magnesium and Aluminum parts. We apply color, run through a small cure oven then apply a clear coat then run it through a finishing oven. This past week we have been experiencing small pits on the aluminum parts that only become noticeable after the clear is applied and cured. These pits are not clustered (1-4 pits on a part and are never together in the same area). Trying to trace the cause for this anomaly is difficult because it is only happening on our Aluminum.
Will RomagerOrthopedic Device Manufacturer - Grand Prairie, Texas USA
October 11, 2014
A. What pre-treatments do you use?
Is your initial coat cure a full cure?
I ask if you have achieved a full metal temperature cure schedule before clear coat?
Please advise as then I may be able to assist you.
Regards,
Bill
Trainer - Newcastle, NSW Australia
October 14, 2014
!! An update to my post concerning the powdered coated horse. I still have not received the horse back and when I talked to the powder coater he told me they have garnet blasted it and recoated it 4 times already and it still ends up the same as before. They are trying everything they can with no good results. He thinks it is something in the cast aluminum itself causing the problem.
I am ready to have it returned to me and I will paint it with primer and epoxy paint.
- Oceanside, California USA
October 26, 2014
A. Ted, try this ... After you have heated the casting, apply the powder when the piece is still hot! You will have to decide the temp. I have found that the powder will be sucked into these porosities. The drawback is that you have very little control on how much powder is applied to your piece but it does seem to fill in the voids well.
![]() Bob Utech Benson, Minnesota |
![]() Ed. note: Bob is the author of: "High Performance powder Coating" on eBay or AbeBooks or Amazon [affil links] |
Bob,
Thanks for the advice. I will pass it along to the powder coating shop. I have not seen how they are trying to do the job, so can not say if they have already tried that idea, but will talk to them tomorrow.
- Oceanside, California USA
October 29, 2014
A. Just get it stripped.
Apply an epoxy primer / filler and do a two pack finish coat.
Once a corrosive element is introduced or blasted into an Aluminium substrate, Powder has no chance.
Hope this helps both you and the tenacious Powdercoater.
Regards,
Bill
Trainer - Newcastle, NSW Australia
October 28, 2014
After 5 tries at powder coating, the powder coater gave up on it. I applied an epoxy primer/filler, patched the pits with Bondo
⇦ on
eBay
or
Amazon [affil links]
, sanded the horse and painted it with a polyurethane paint and finished it with 6 coats of clear.
I think it came out looking good. Thanks to all of you for your comments.
Ted Lohry [returning]- oceanside, California USA
November 22, 2014
November 2014
"Good" is an understatement. Wow, it's beautiful.
Regards,
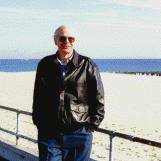
Ted Mooney, P.E.
Striving to live Aloha
finishing.com - Pine Beach, New Jersey
Q. Hi I'm doing powder coating and these days I'm coating some metal switches. After coating 75% of rejections because small pin holes appear.
Please advise best way to avoid this.
- Negombo Sri Lanka
September 30, 2018
A. Hi Umesh. We appended your inquiry to one of a dozen threads on pinholes in powder coating. It's a broad problem such that you'll probably have to provide a lot of info before anyone will be able to add to what has already been said, and pictures of the defects would doubtless be helpful.
From your postings on another thread (15733), you were powder coating on aluminum. May we assume these "metal switches" are aluminum? May we assume they are not diecastings?
Regards,
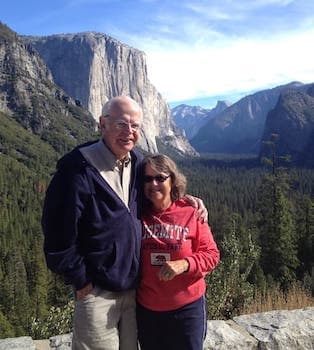
Ted Mooney, P.E. RET
Striving to live Aloha
finishing.com - Pine Beach, New Jersey
October 2018
Q, A, or Comment on THIS thread -or- Start a NEW Thread