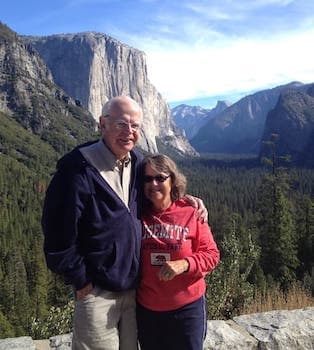
Curated with aloha by
Ted Mooney, P.E. RET
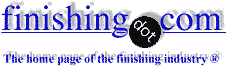
The authoritative public forum
for Metal Finishing 1989-2025
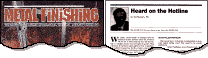
Thread 350/82
Acid based electrolytic cleaning
Q. I'm in the process of learning more about surface cleaning, finishing, and coating. I'm using the ASM Volume 5 for reference. I was wondering if anyone ever used acid for cathodic electro cleaning of carbon steel. Cathodic cleaning uses hydrogen ions for the scrubbing action instead of hydroxyl ions, so I was wondering why a basic solution is recommended for both anodic and cathodic cleaning.
Keith Davisfuel cells - Danbury, Connecticut, USA
2005
publicly reply to Keith Davis
2005
![]() |
A. Bases or alkalies are preferred because they are effective in dissolving greases and oils. Acids are not, also some unwanted metallic species may be present dissolved in the cleaning baths. Cleaning in forward polarity may result in their reduction and consequent deposition over the surface of the part instead of leaving the bare metal clean. For that and other reasons, like the brittleness of high strength steels, acid cleaning is preferred as a mid or final step after alkaline cleaning and mostly used on reverse. G. Marrufo-Mexico Guillermo MarrufoMonterrey, NL, Mexico publicly reply to Guillermo Marrufo A. In addition to the scrubbing action of the generated gasses, alkaline cleaners are able to saponify oils and greases. Acids generally have no effect on oils and greases. ![]() Jeffrey Holmes, CEF Spartanburg, South Carolina 2005 publicly reply to Jeffrey Holmes, CEF
"Practical Guide to Industrial Metal Cleaning"
by David S. Peterson ![]() on AbeBooks or eBay or Amazon (affil links) A. The scrubbing action is only one aspect of the cleaning process. All things being equal, it's a lot easier to remove organic soils with alkaline cleaner formulations than with acidic products. An acidic product also has the potential of attacking the steel surface, while you can pack the caustic into an alkaline cleaner and not do any harm to the surface. George Gorecki- Naperville, Illinois 2005 publicly reply to George Gorecki |
Q. My particular application for electrolytic cleaning is to remove rust and scale, therefore the breaking down of soils with an alkaline solution isn't paramount. Acid dipping is another method for attacking the oxides and I was wondering if acid in either an anodic or cathodic environment would be most effective.
Keith Davis [returning]fuel cells - Danbury, Connecticut, USA
2005
publicly reply to Keith Davis
![]() |
2005 A. US patent 6294072 seems to be relevant to your enquiry. ![]() Bill Reynolds [deceased] consultant metallurgist - Ballarat, Victoria, Australia We sadly relate the news that Bill passed away on Jan. 29, 2010. publicly reply to Bill Reynolds A. Not enough information and far too many variables for a finite answer. Anodic acid might work great for a while and then the amount of iron or copper or chloride ions reach a magic point and the parts would be pitted beyond use. Temperature is a factor as is the voltage applied. In acid cathodic, you reach a point where crud will plate out on the part which can be difficult to get off. - Navarre, Florida 2005 publicly reply to James Watts |
Q. The reason I was contemplating using electrolytic cleaning in conjunction with the acid is to get the benefit of the scrubbing action of hydrogen/oxygen. I can't use abrasive blasting because it will not reach internal cavities. These internal cavities have rust (cast iron manifolds, pump housings). Normal passivation does not actively remove the scale, and I've had good luck doing both acid cleaning, and alkaline electrolytic cleaning, and I was just wondering if the combination would add some benefit. Maybe I'll check out that patent.
Keith Davis [returning]- Danbury, Connecticut USA
2005
publicly reply to Keith Davis
A. In Cathodic Electrolytic Cleaning a current impressed on the cathode. This impressed current reduces the hydrogen cations to H2 gas, which then causes a mechanical scrubbing action on the surface of a material. This mechanical scrubbing has the potential to remove scale, but has an assortment of problems associated with it. The biggest problem is contamination from other metal cations. These cations will plate on the surface of the cathode. Make sure your anode is anodically inert. Graphite should be used. Because of contamination issues many references recommend an alternating current. However, my company has used cathodic electrolytic treatment successfully on the pilot scale. Hope this helps.
Luke Autryelectroplating - Ellington, Connecticut
2005
publicly reply to Luke Autry
Neutral pH Electrolytic Cleaning
November 14, 2015Q. Hi
Is anyone aware of a pH neutral chemical that can be used in lieu of acid or alkali to take advantage of the scrubbing action alone?
Not a silly question - I am copper plating ceramic coated steel (plating areas not covered by ceramic) the ceramic is resistant to acids but not resistant to strong alkalis and attacked more vigorously when the solution is hot as you would expect.
It is not possible to apply the after the plating operation on account of the temperatures involved in applying the ceramic materials.
Desirable qualities should include non-toxic gases so sodium chloride is out, I looked into sodium carbonate
⇦ this on
eBay or
Amazon]
(soda crystals) not sure about that - it does apparently dissociate into sodium hydroxide and carbolic acid in water but manufacturers don't use this as a method of producing sodium hydroxide so it may be a weak effect and not a concern.
I already have a cleaning routine that is effective for situations where I do not need to apply the ceramic but when I am working with the ceramic I cannot use the strong alkali electrolysis to clean hence this question.
Grease is not a major issue as the steel has been heated to 850 °C (red heat) so I figure all being equal I will get some of the benefits I seek with a pH neutral scrub.
I do have degree of smut to deal with - it seems to come from the silicon carbide sand blast, I suspect minute particles get lodged in pores.
Whilst waiting hopefully for an answer I figure I will just try a very small quantity of sulfuric - just enough to get a reasonable conduction going.
- Saltum Denmark
publicly reply to Jon Light
![]() |
November 15, 2015 Q. Just an update to my previous posting regards pH neutral scrubbing. - Saltum Denmark publicly reply to Jon Light Jon - Colorado Springs, Colorado November 16, 2015 publicly reply to Willie Alexander |
Hi Jon. You seem to have come up with a very clever idea!
Regards,
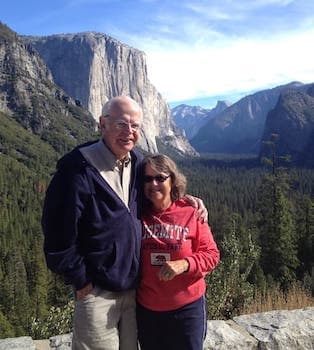
Ted Mooney, P.E. RET
Striving to live Aloha
finishing.com - Pine Beach, New Jersey
publicly reply to Ted Mooney
November 22, 2015
A. Hi Jon
Your aim appears to be simply copper plating on steel with a partial ceramic coating.
Presumably you degreased the steel before heating to 850 "C (well above red heat) otherwise you would have carbon baked onto the surface - and a major cleaning problem. And by that I mean degreased to plating standards i.e. a water break free surface.
So, assuming the steel has only light heat scale to remove, I cannot understand your choice of an alkaline cleaner which will have no effect on oxides - unless you use a cyanide based process. Simple soak cleaning is sufficient, no need for current and no mist formed.
If you are then using a sulphate plating bath, sulfuric acid cleaning would be the obvious choice.
But that brings us to the next problem. Acid copper sulphate
⇦ this on
eBay or
Amazon [affil links] plating on a steel substrate is rarely successful due to the poorly adherent immersion deposit that forms as soon as it enters the bath. Normal practice would use a copper cyanide process at least for the initial strike coat possibly followed by acid copper to build up thickness although the greatly improved throwing power of the cyanide bath would help with thickness distribution. As an alternative copper pyrophosphate could replace cyanide but the chemistry is much more difficult to control.
Your idea for plotting current distribution was commonly used in the 1960s using a potentiostat method. In the late 70s a small coil was used and if I had to do the job today a miniature Hall effect device would probably be the way to go.
Depending on the tensile strength of the steel and the processes chosen and the final use, you may have to consider a final de-embrittlement stage.
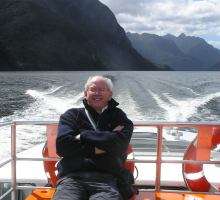
Geoff Smith
Hampshire, England
publicly reply to Geoff Smith
November 24, 2015
Hi Geoff, thanks for the reply.
Yes the steel is de-greased before heating to 850, like with electroplating the ceramic adhesion is dependent on cleanliness. I have not experimented to see which is more "fussy" I simply apply the best cleaning methods available to me throughout. A waterbreak free test is part of my visual inspection routine.
The hot alkaline bath is part of my steel degrease routine, first a solvent then hot alkali with electrolytic cleaning; the texts I have on the subject seem to recommend a double barreled approach here. Being artisan level I don't have access to specialist solvents and vapour equipment -- the double barrel approach works for me well and adhesion tests on flat non-ceramic samples (no heat stage) show that the plate is slowly worn away with no lift or peel. I am confident in saying that all complications for me arise out of shape (covered in other postings) and the aftermath and processes involved in applying the ceramic whilst protecting the metal destined for plating.
Yes I understand that conventional acid plating onto steel will result in immersion deposition I use a flash plate first although I do not use cyanide.
In an ideal world I would simply use the alkali cleaner before the ceramic taking advantage of both its grease removing and physical scrubbing action. I would then use the same process after the ceramic is applied (pre-plate) taking advantage of its scrubbing action but regarding its grease removing properties as being hopefully redundant. The reason I cannot adopt this simple re-use of an existing process is the fact that the ceramic does not stand up particularly well to hot alkalis so I am looking for the same scrub action but without the alkali.
What am I trying to scrub off ?
===============================
The steel that requires plating has been protected from gross oxidation by a paste which is a ball milled mixture of sand (safety note below), specialist clays, wood ash and so on. The anti scale mixture is very good but it is not perfect, there are still thin oxide films in places (blue haze not hard black crust). Even though the anti-scale is doing a very good job and leaves shiny steel in places it is not perfect and I watch out for particles hiding in pores and pits, the steel is used as supplied (cold rolled) and magnification at only 40x shows within the apparently smooth surface there are plenty of places for particles to hide. I could resort to full on blasting but I consider that a last resort as it brings along its own issues and complications, my judgement is that an acid pickle, electrolytic scrub and a very light hand applied abrasion should be sufficient - at least thats the direction I am trying to pursue before resorting to blasting indeed the effort gone into the anti-scale reflects the wish to sidestep blasting as a process.
Jon
Postnotes
=========
Safety Note: Since I mention ball milling of sand. For the unaware experimenter please make sure you are familiar with the dangers of ball milling, sand and silicosis. Ball mills can/do produce ultra fine powders. There are substances which are considered benign in larger grain size which are potentially hazardous to health when milled ultra fine - glass for instance, freshly WASHED large grain frit is not usually considered hazardous but ball milled ultra fine glass frit can easily go airborne.
Anti-scale Note: The anti-scale mix I have experimentally developed is based on what westerners "think" Japanese sword makers are/were doing - by this I mean that master craftsmen tend to be a bit cagey about whats in their mix. I avoid certain anti-scale products sold in the west because they tend to cause pitting (borax and so on) so I use only specialist clays, ash and sand. The effectiveness of these pastes is highly dependent on particle size - clay is already composed of very fine particles but sand is not - in addition ultra thorough mixing is required (stirring paste with a spoon does not cut it here).
- Salum, Denmark
publicly reply to Jon Light
Sorry Geoff, I can see my previous wording very reasonably led you to question if I was relying on red heat to remove grease. The answer is no -- I am afraid coming from a scientific background I have a kind of "Doubting Thomas" approach that tends towards belt and braces. I betray my doubting mind by lining up three processes (solvent, alkali, heat) and then suggesting that the third would be a safety net for the first two - its more of the "no such thing as 100% only 99.99999%" if you catch my drift :-) Either way from your response I see that you think that heat treatment would only convert one problem (grease) into another (hard to remove carbon) - makes me think of my first plain steel wok so my take on that is "don't lean on the third process as a catch all" - thanks.
Sorry Ted, if I had been more on the ball I would have sensed my previous mis-direction to Geoff and got it all in one posting instead I have posted twice today.
- Saltum Denmark
November 24, 2015
publicly reply to Jon Light
Q, A, or Comment on THIS thread -or- Start a NEW Thread