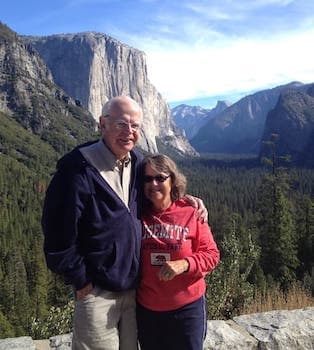
Curated with aloha by
Ted Mooney, P.E. RET
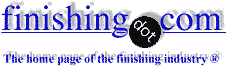
The authoritative public forum
for Metal Finishing 1989-2025
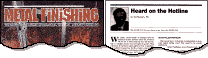
-----
What is the difference between electroplating and conversion coating?
2005
I am reviewing a WWT system design for a Zn/Cr plating line. We have a concern with disposal options of the sludge generated. We thought it was a F006 listed waste, but we have found some information that the sludge is exempt if it is a conversion process. My questions are:
1. What are the differences between electroplating and conversion coating?
2. When is conversion coating applied, versus electroplating?
3. Any suggestions on the listing of the sludge as a hazardous waste?
Any help/guidance would be greatly appreciated.
consulting - USA
by Biestek & Weber
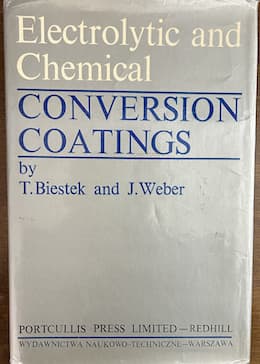
on AbeBooks
or Amazon
(affil links)
Chromate conversion coatings (also known as passivate coatings) are a chemical immersion process and are applied to electroplated zinc deposits to give protection against oxidation of the plated deposit.
The sludge produced from a WWT system treating the effluent stream from an electroplating process is generated as a result of many operations, not all of which are electrolytic.
Don't know the limits in the US but I'd be surprised if it wasn't classed as hazardous waste.
Your clients really should know this pretty basic information.
- Fife, Scotland
WWT sludge from electroplating is F006.
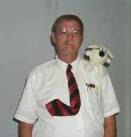
James Totter, CEF
- Tallahassee, Florida
2005
1. Electroplating is a process where metal is electrically attracted to the part and forms an electrochemical bond with the base metal with excellent adhesion and corrosion resistant properties. This coating is typically very thin and typically serves as the final coating for the part. Conversion coating, on the other hand, is almost never used as the final coating for any parts. It is a chemical process that forms a crystalline coating on the part, providing an excellent corrosion resistant base for paint, oil, or powder coatings. Which one you select is entirely based on the application. Conversion coating is much faster and cheaper and better suited to high speed production of parts that will be painted, but has nowhere near the performance of plated parts. I know I sound like a plating advocate, but my background is 16 years of selling conversion coating materials, the application will determine which is best.
2. I kind of covered that above too, basically if you want this treatment to be the stopping place you have to go with plating. If you intend to coat the parts with paint, oil, e-coat, autophoretic, or powder coatings after treatment then your best bet will be conversion coating.
3. James is right, F006, but the final answer can depend on both the chemistry you select and the waste treatment process you use. Be sure to find someone knowledgeable to help you select all this.
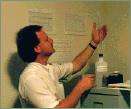
Jeff Watson
- Pearland, Texas
2005
I am concerned that many experts in the surface finishing industry are using words that confuse the public in the field of Metal deposition or plating in general.
In so far as chromate conversion coating. It is said that the process is not a plating process but a deposition of crystalline films on a surface. I tend to agree somewhat. My understanding is that coating is a deposition or Plating process. Plating include but not limited to electroplating or electrodeposition, electroless deposition or coating, brush plating, immersion deposition or coating to name a few. In a Chromate conversion coating, the part to be coated is the substrate (cathode) and the anode is the deposition active species from the conducting bath which are attracted to deposit on the substrate's crystal lattices, growing and spreading on the substrate surfaces, atomic layer by layer.
To prevent confusion and keeping it simple, let's therefore conclude that chromate conversion coating is a type of immersion plating process or deposition. To me coating or deposition means plating. Any dissent?
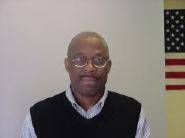
Bassey J. Udofot
Musgegon, Michigan
December 25, 2008
December 29, 2008
Hi, Bassey. I'll have to dissent a little bit. The meaning of words, however we attempt to simplify, is often context-dependent: to a soldier, a tank is an armored fighting vehicle; to a gas station attendant talking to the delivery truck, it's the underground storage vessel at the station; to the same station attendant talking to a customer, it's the gasoline container inside the automobile.
To a plater, chrome plating is the hard, shiny, wear resistant metal coating s/he electrodeposits onto the substrate and which, because it is metal, is not RoHS regulated. And also because it is metal, it doesn't matter to the end user whether it was deposited from a trivalent or hexavalent bath because, as deposited, it is neither of the two, it is simply chrome metal.
To the same plater, chromate conversion coating is a gelatinous coating that is deposited onto zinc plated parts or aluminum parts to deter corrosion, but which is without any wear resistance or much decorative value. And in this case it is crucial to the end user whether the bath was trivalent or hexavalent because parts from a hexavalent bath are not RoHS-compliant, and they leave hexavalent chromium (considered carcinogenic) on the part.
For this reason, I think it is important to maintain the term "chromate conversion coating" as distinguished from "chrome plating". The origin of the term is probably based on the fact (or belief) that some of the substrate metal is "converted" to a compound like zinc chromate that then forms a percentage of the coating; whereas in electroplating or electroless plating the substrate is not consumed as part of the process.
Back to Stan's original question, the sludge from zinc plating plus chromate conversion coating is regulated as F006, as previous respondents have said.
Thanks for your input.
Regards,
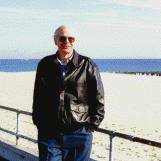
Ted Mooney, P.E.
Striving to live Aloha
finishing.com - Pine Beach, New Jersey
Q, A, or Comment on THIS thread -or- Start a NEW Thread