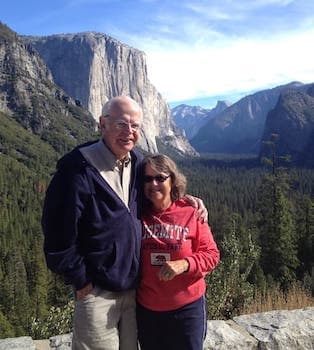
Curated with aloha by
Ted Mooney, P.E. RET
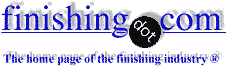
The authoritative public forum
for Metal Finishing 1989-2025
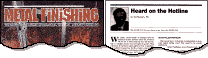
-----
Gold Plating the ID of tubing
1999
Hello All,
I have an application where I have a 10.5" piece of tubing that has a .310" ID. I have an IR light source at one end of the tube and and IR detector at the other end. I want to transmit the maximum amount of light down the tube. These are the only parameters at this point ..... well, almost. I have to be able to machine the tube on either end to hold the IR source and detector and I also need to drill 2 holes and attach a small inlet & outlet port about 0.5" from either end. Oh yes, it has to be cost effective too!
Right now I am using a stainless steel tube, electropolished (to
10Ra or better) and then gold plated (20 µin min.). I am using this technique on the advice of several sources and also on the experience of 1 prototype that we have had built.
First I would appreciate any input on if this is the best way to do it and/or what other alternatives are there I should consider.
Second, I have been given information from several sources concerning some of the details of this project and I wanted to get the opinion of many industry experts on these details.
1) I am informed that a nickel undercoat is necessary before gold plating over electropolish. I have been told this universally. I have also been informed that the gold will take the reflective characteristics of what it is plated over. Is this true?
2) Are there different types of gold to choose from for this application. Is one better than the others for passing the maximum amount of light energy down the tube?
3) There has been a lot of concern about how the good the nickel and/or gold plating will be in the middle of the tube. For some reason, some of the platers I have talked to are concerned that after you get 2" in on either end, the plating will not be as "good" as on the ends. I don't know why this is. I am not sure if they are using a
"forced flow" or simply a bath. Maybe they are just "hedging" since they have no way of inspecting the middle of the tube. Any opinions on this?
4) As a secondary process I have to attach inlet and outlet ports as I mentioned above. The tube (by design) must be thin walled
(.035") and currently the inlet port is a flat surface mating to the curved outer diameter of the tube. Because there is not much surface area, epoxy does not seem to be a good solution for attachment. We have looked at welding, but don't get very good results because of excessive heat and also penetration into the tube of the weld material. Now we are exploring a silver solder process. We are planning on doing the silver solder of the inlet and outlet ports after electropolish, but prior to the gold plating. Will any of the chemicals in the silver solder affect the gold plating process or vice versa? Will the heat involved in silver soldering mar the electropolished surface and cause problems for the gold plating
(either adherance or reflectivity)? Any comments you can give here will be appreciated.
Thanks in advance,
Newnan, GA 30263
1999
1). The nickel undercoat is a very good idea for two reasons: a) Materials like copper, which could be in some stainless steels, can diffuse into gold and spoil it. As for "taking on the reflective characteristics", what people are talking about is topography--the gold plating will follow the contour of the surface; b)Nickel can to some extent "self-level" offering a more reflective topography.
2). Gold comes in various colors and it is possible that some are better IR reflectors; I don't know.
3). If, as a kid, you ever did those experiments where you put
iron filings
[affil links] on a piece of paper and a magnet underneath and saw the flux lines, you will be able to easily appreciate that electrical flux lines are the same thing. The current follow the path of least resistance, which is definitely not into the tube except perhaps very near the ends. Electrodeposition occurs in proportion to the current density. Two solutions are: a) electroless gold; b) an anode running down the inside of the tube. I don't think 'b' is much of a problem.
4). I don't think this will be a problem, but it's not something I have much experience in.
Good luck,
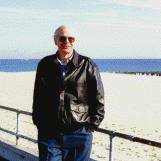
Ted Mooney, P.E.
Striving to live Aloha
finishing.com - Pine Beach, New Jersey
You can gold plate the ID of the tube using anodes to activate the surface nickel and gold plate. Nickel is needed over the stainless steel for adhesion of the gold. This process is currently being done on tubes .25" ID X 48" long stainless steel tubes with a final coating of silver.
David Crocker- Valencia, California
1999
Is it possible to prepare a solid form [mandrel] in wax or zinc, then do gold,and Nickel on top of it to the desired thickness? Gold could subsequently be burnished to full luster. I have not done it. This is just an idea
Yashawant Deval-Electroplater - Pune, Maharashtra, India
1999
The selection of gold might not be the best selection of a finish for this product. May I suggest that Silver electro-deposits are more uniformly deposited in recessed areas and can be mechanically polished to a high brightness? It can also be electro-polished. As a final finish Rhodium is the most reflective of all electro deposited metals. This is common finish used for this purpose. What is the purpose of selecting stainless as the material for the tubing? With this process electro-polishing of stainless steel would not be as important. The nickel process normally used for stainless steal is what is called "woods nickel".
Current distribution in the inside of the tubing is the problem in getting a uniform deposit inside the tubing. Without an internal electrode a reasonable distribution can not be obtained. Since the diameter of the internal electrode must be small, uniform distribution will still be a problem. A solution to this might be dual internal electrodes with separate DC power supplies.
Solution depletion will occur rapidly inside a small diameter tube and solution movement inside the tube should be provided. This can be accomplished by cathode road agitation or by pumping solution at or in the end of the tubing. If gold is used it should be 24K bright gold. Not all-gold deposits will reproduce the underling finish.
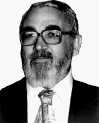
Gwynne I Edson
- Huntington Beach, California
2001
Q, A, or Comment on THIS thread -or- Start a NEW Thread