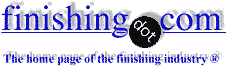
-----
What is Best Wear-Resistance Plating for Aluminum
Q. I have an application that requires a conductive, non-organic coating on complex machined parts made of aluminum (about 4" x 4" X 0.5"). The plating is intended to provide some wear resistance and to prevent aluminum from rubbing onto small ceramic pieces that are in contact with these parts. The parts will be heated to temperatures up to 125 °C.
I am thinking of using Ni plating with Cr but I can't find any specific information in reference books about plating on aluminum. Any information you can supply about appropriate plating thickness, problems with this approach or better approaches will be appreciated.
Quebec, Canada
1999
A. As soon as you said a complex geometry part, chrome is fairly close to a poor choice. Aluminum is plated by a zincating (double zincate preferred) strike, an alkaline electroless nickel is excellent and that is immediately followed by EN plating. You may partially harden the EN, but you can not use the 650 °F temp as it will destroy the mechanical properties of the aluminum.
An alternative is hard anodizing. No temp problems, but you only get one chance if it has very tight tolerances.
Another alternative is one of the vapor deposition coating processes; here again pay attention to the choice as some will exceed the max temp of the aluminum.
- Navarre, Florida
1999
A. Hi Michael,
If the parts are complex geometry then electroplating will not give you the best coating performance for either wear or corrosion protection and the chrome will probably not take in certain areas because of its poor throwing power, gas pockets, "etc.". I would suggest that you investigate Electroless Nickel with a High Phosphorous content, will give the best corrosion resistance; and wear resistance can be improved by Heat treating after plating. Regards,

John Tenison - Woods
- Victoria Australia
1999
A. Hi Michael,
I would have to agree that electroless nickel sounds like the way to go. It plates very uniformly on complex geometries and is easily plated on aluminum by the zincate method. Some shops will even co deposit sub micron particles of diamond, silicon carbide or other ceramics for added abrasion resistance. I believe anodize won't work because of the conductivity requirement.
Dayton, Ohio
1999
Mr Richardson is certainly correct about anodizing. I missed the conductive word.
James Watts- Navarre, Florida
1999
A. Nickel glycolate strike described in Metal Finishing magazine 1981 (May) also works real nice. I have tried and found it real good. Vijay
Yashawant Devalelectroplaters - Pune, Maharashtra, India
1999
There is an ASTM specification covering a neutral nickel strike. This may be the glycolate bath.
ASTM B253 "Standard Guide for Preparation of Aluminum Alloys for Electroplating".


Tom Pullizzi
Falls Township, Pennsylvania
2001
A. Use electroless Ni-Boron solution after electroless Ni-Phosphorous plating. Ni-Boron coatings have very good wear resistance.
Jaspreet gandhi- Boise, Idaho, USA
August 8, 2008
Q, A, or Comment on THIS thread -or- Start a NEW Thread