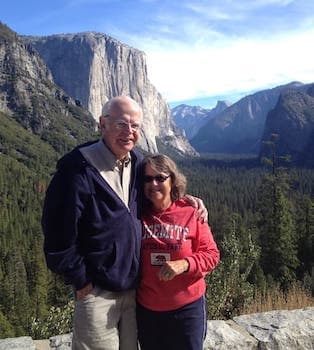
Curated with aloha by
Ted Mooney, P.E. RET
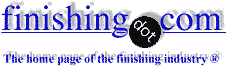
The authoritative public forum
for Metal Finishing 1989-2025
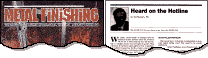
-----
Multi Color Anodizing 6061 Problem
2005
I am a mechanical engineer and was tasked with coloring one end of a part gold and the other end blue, about 50 percent each color. The part is a piece of 3/4" thick 6061 T6 plate, 10" long by 6" wide.
I went to a local large plating company and they showed me their equipment and process for anodizing. I saw that after anodizing they would normally apply a dye by submerging the entire part for a length of time and then rinsing before sealing and drying. I proposed that I build a device that would attach to their lifting fixture. The device would be made of 6061 (same as part), go through the entire process with about 50 parts, be stripped before reuse, and lay (index) on top of their dye tanks, only allowing the part to be partially submerged in the dye. It would allow them to totally submerge it in the initial cleaning and anodizing process, before the normal time to submerge the part in dye. After lifting the device off of the first dye tank, they could rinse the part and then flip the parts over in the device, allowing you to set it on the next color dye tank and dye the other half of the part. There would be a space between the two color lines on the individual parts that would keep the one dye color from touching the other and it satisfied what we needed out of the finished part. through a test run we found the correct water/dye level of the tank and scribed the level on the inside of the two color tanks.
I built it and we tested it. quite a few parts, but we tried it out on only 11 of them.
Observations:
A) after the rinse and dipping the part in the blue color, the blue wicked up the sides of the parts an inch or so, non uniformly. This is not good. I allowed the anodizer to spray water on the parts to keep the dye from creeping up too much but the blue color line on the part became spiked with blue. The part spent 4 minutes in the blue tank.
B) The gold line (10 minutes of immersion) was laser straight.
Was it just surface tension that lead the blue to raise up the sides of the part and not the gold?
Has anyone tried this two colors on one part with success using some other method? Tape off the parting line? Different dye?
The part was decent but with the gold looking so nice and the blue looking runny it is not up to our standards. Any help is appreciated from you gurus.
They physically flip over the part after the first dye and rinse.
David Petersen- Mukilteo, Washington
A person you might want to speak to is Bob Probert who is a consultant and has his listing on Finishing.com. If it can be done Bob will know how.
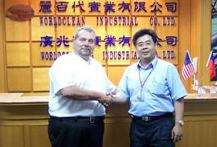
Drew Nosti, CEF
Anodize USA

Ladson, South Carolina
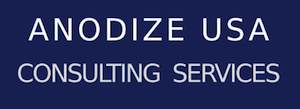
2005
Q, A, or Comment on THIS thread -or- Start a NEW Thread