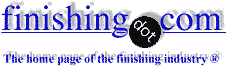
-----
Cadmium plating
Does anyone in the industry know where the typical 96 hour salt spray corrosion resistance for cadmium plating, or other similar types of plating, came from. Within the aerospace industry this seems to be a fairly typical process control test. Normally, cadmium, or other plated finishes such as zinc-nickel plating, can withstand much longer than 96 hours.
Also, has anyone seen anything which attempts to equate salt spray corrosion resistance for plated parts to in-service corrosion resistance ?
Engineer - Belfast, N.Ireland, UK
2005
Hello David. I think the 96 hours refers to the formation of white rust, not the whole life of the coating before red rust. I think you would find that older clear chromates or leached yellow chromates might not last even the 96 hours.
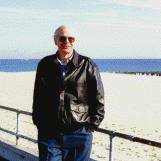
Ted Mooney, P.E.
Striving to live Aloha
finishing.com - Pine Beach, New Jersey
2005
Thanks Ted. In fact the 96 hours relates to the formation of white corrosion products on the cadmium plating (or other plating) rather than red corrosion of the base material. What I'm really trying to find out is, why 96 hours ? Typically all aerospace specifications use this number but the coating is capable of lasting much longer.
David BahraniEngineer - Belfast
2005
Again, your process, and some other processes are capable of lasting much longer but there are and have been cadmium plating processes (well, actually chromating processes) not capable of that. To know where "the" specification came from would require knowing exactly what spec you refer to, but typically a group of experts sit on a committee for each spec, meet to put their heads together and relate their experiences, and develop a spec. Most such specs have a revision history as subsequent groups reiterate the process.
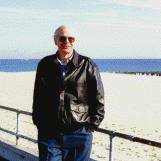
Ted Mooney, P.E.
Striving to live Aloha
finishing.com - Pine Beach, New Jersey
2005
Q, A, or Comment on THIS thread -or- Start a NEW Thread