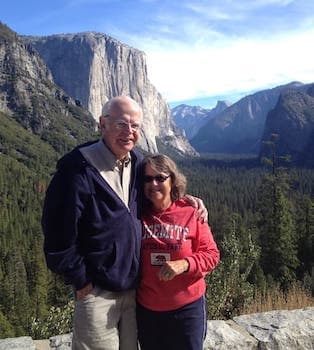
Curated with aloha by
Ted Mooney, P.E. RET
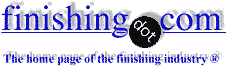
The authoritative public forum
for Metal Finishing 1989-2025
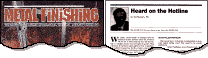
-----
Which Al alloy sheet will lapp to the best mirror finish?
Q. I am currently attempting to lapp 1.6mm (.063) 2024 T3 bare sheet on a commercial lapping machine to make optical grade mirrors. I have tried a few different combinations of different paper grits, and chemical/mechanical compound, but still end up with some haziness, orange peel and also there seems to be some surface lines witch lapp out, but come back when polished. The lines I think may be variations in the harness from the T3 cold roll process.
I am wondering if I could make my life easier by switching to a different alloy or temper for aluminum sheet. 6061-T6? 7075-T6? I suspect the harder, the better, but the hardness must also be uniform. Stainless lapps very nice to a great mirror, but the optical properties of stainless are not as good as bare aluminum.
Also, it is possible that I just am not very skilled at lapping, and am re-marring it as I try to polish.
Any suggestions are appreciated.
Thanks.
Mark SchnittkerCustom optical manufacturer - San Jose, California, USA
2005
? What type of equipment are you using? Lapping involves more than the abrasive, pressure is also involved.
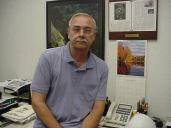
AF Kenton
retired business owner - Hatboro, Pennsylvania
![]() |
Q. The metal mirror is 31x43mm rectangular. The fixture that it is mounted to is a 0.8kg mass of stainless (Cylindrical 64mm diameter by 32mm in height). I had also tried a lighter mass which was too light and started to chatter. The machine that I am using is a Southbay Technology model 920. http://www.southbaytech.com/cgi-bin/homepage/products/view_product.cfm?ProductID=40 I am using SiC paper with a constant flow of water (not recycled from the bath). I start with 60um grit, and move to 5um grit. I basically cannot go finer than 5um as it starts to make new gouge lines. After the 5um grit paper I move to a polishing pad and believe it or not my best results are then to use Mothers Mag & Aluminum Polish ⇦ this on eBay or Amazon [affil links] on the pad instead of the polishing solution. If I take off the Al mirror and set the stainless fixture on the lapper it comes out looking great. The stainless fixture that came with the lapper had a greater mass than my fixture, so if I am off on the mass, I would guess that I am too light. I am not an experienced lapper, so if I am doing something fundamentally idiotic, please let me know. Thanks. Mark Schnittker [returning]- San Jose, California A. Mark, 6061 would likely be a better choice than 7075, as it has less second phase particles. Think of them as microscopic "rocks" that give the aluminum it's strength. Going along that path, an 1100 series aluminum would be best, as it's most nearly pure. You have to be careful not to smear or imbed lapping compound in the softer metals, but it can be done well. Or, I should say, on a small scale: my experience is with pieces of aluminum prepared metallographically. It is an art, and often less polishing is best. There is a lot of good information that can be found under the "metallography" heading on other sites. Good luck! ![]() Lee Gearhart metallurgist - E. Aurora, New York |
A. 3003 is typical aluminum alloy used in light reflectors. It reacts well to being R5 bright dipped (old Alcoa process) followed by anodize. 2024 would be one of worst to use given it's high copper content.
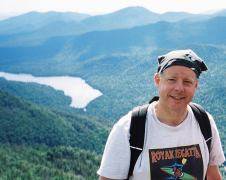
Milt Stevenson, Jr.
Syracuse, New York
Q, A, or Comment on THIS thread -or- Start a NEW Thread