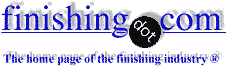
-----
Keeping Copper Bright
2005I was reviewing questions/answers posted on Finishing.com and have a question concerning copper. We are fusing glass between 1300 and
1500F (depending upon the glass) and will place copper foil between glass sheets. Our goal is to have a bright copper rather than a tarnished copper at the end of the fusing process and we are meeting with limited success. We have retained some bright areas when we minimize the oxygen around the copper (we build a dam around the copper using glass frit) and we have seen occasional bright areas when the copper is in contact with aluminum mesh (which appears to become the sacrificial element which consumes oxygen earlier in the temperature ramp). Have you seen anyone clean, then passivate copper, to maintain its bright appearance ? If so, what chemistry might you suggest ?
Thanks
lighting - Casa Grande, Arizona, USA
Robert
Exposed Copper can be run thru a brightening dip and then after rinsing twice , thru an anti tarnish.
The US has a number of compnies that provide such products.
Regards
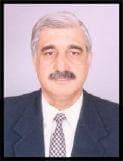
Asif Nurie [deceased]
- New Delhi, India
With deep regret we sadly advise that Asif passed away on Jan 24, 2016
2005
2005
At that high temperature, there is no barrier you can put on a copper surface that can stop the oxidation potentials from having their way. The thickness of your melted glass is the only available impediment or partial barrier. So you can only get bright copper sealed in glass, if the glass and/or the atmosphere is reducing. Though not so reducing as to precipitate something in the glass or change it's color. Since you can use aluminum, your glass is very difficult to over-reduce.
I'd guess you really need to seal up your fusing oven and flow nitrogen thru it to keep out air in additon to building those dams. And then if that almost works, add 1% hydrogen or forming gas. A poor man's hydrogen would be adding 1% natural gas, but then there would probably be 1% concentration of toxic CO (carbon monoxide) in the exhaust stream and leaking out all oven seams. Very dangerous.
Suppose you use a combination of a closed volume inside a flowing gas. The glass & copper go in a tightly closeable ceramic dish & lid, with a modest piece of graphite. The graphite will convert in-leaking traces of O2 (an oxidizer), to CO (a reducer for copper). The tight fit of the dish and the low-oxygen gas outside it minimize the total amount of CO generated and released. To know these safety features were working right you'd need monoxide monitors beside the oven and by the exhaust outlet outside. But usually it would work fine. The graphite will pit and evaporate slowly. You could infer the total amount of monixide generated by weighing the graphite after each run. If you use thin graphite sheet, you'll have large oxygen-reacting area with relatively small worst-case monoxide generation. All fairly tidy.
I have annealed copper in inert gas at >800C, in the presence of high-purity graphite it doesn't darken, perhaps even brightens a little. I expect the redox potential inside many molten clear glasses would be changed by the ambient atmosphere, and immersed copper would stay bright.
- Los Angeles, California, USA
Q, A, or Comment on THIS thread -or- Start a NEW Thread