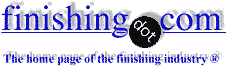
-----
Waste water recovery system
2005
DEAR SIR, GREETINGS,
WE ARE A NON FERROUS COLD ROLLING MILL INDUSTRY ROLLING COPPER AND BRASS STRIPS. DURING THE MANUFACTURING PROCESS OF THE STRIPS WE HAVE TO ACID PICKLE THE STRIPS WITH A PICKLE BATH OF sulfurIC ACID.
WE ARE LOOKING FOR A SOLUTION TO OUR WASTER WATER RECOVERY SYSTEM. AFTER THE PICKLING PROCESS THE STRIPS ARE ARE SQUEEZED THROUGH A PAIR OF RUBBER ROLL TO AVOID CARRYOVER,BUT STILL THERE IS SOME CARRYOVER WHICH HAS TO BE SPRAYED BY WATER.
THIS RINSE WATER GETS CONTAMINATED WITH FREE ACID, copper sulphate AND ZINC SULPHATE (THOUGH IN VERY MINIMAL LEVEL) THE ANALYSIS OF THIS WATER IS AS UNDER:
1. COLOUR: COLOURLESS
2. ODOUR : ODOURLESS
3. TEMPERATURE: 30 DEGREE C
4. PH5
5. CONDUCTIVITY: 2820 MICRO MHOS/CM
6. TDS : 2000 MG/L
7. SUSPENDED SOLIDS: 60 MG/L
8. BOD AT 27 DEG.C 3 DAYS: 51 MG/L
9. COD: 78 MG/L
10. COPPER: 10 MG/L
11. IRON: TRACES
12. ZINC: 20 MG/L
13. OIL: 3 MG/L
14. GREASES: TRACES
PRESENTLY THIS WATER IN TOTAL IS BEING SENT TO THE EFFLUENT TREATMENT PLANT IN WHICH WE DOSE CALCIUM HYDROXIDE IN THIS WATER AND THE copper sulphate and ZINC SULPHATE REACT WITH THE HYDROXIDE TO FORM PRECIPITATES OF COPPER HYDROXIDE AND ZINC HYDROXIDE. THIS PRODUCT IS SENT TO A CONICAL SETTLER TANK. THE BOTTOM OUTLET OF THE CONICAL TANK IS CONNECTED TO A FILTER PRESS TO COLLECT THE SLUDGE AND THE WATER IS REUSED IN THE SIMILAR FASION AGAIN AND AGAIN.
WE HAVE BEEN GIVEN TO UNDERSTAND THAT THERE ARE CERTAIN SYSTEM WHICH CAN BE INSTALLED TO AVOID 100% WATER BEING TREATED IN THE ETP.
THE FUNCTION IS THAT THE RINSE WATER WHICH IS CONTAMINATED (WITH ZINC SULPHATE + copper sulphate + FREE sulfurIC ACID) IS PASSED THROUGH A MEMBRANE OR A RESIN BED FROM WHICH TWO WATER STREAMS WOULD BE COMING OUT AS UNDER:
1. (PERMEATE) FIRST STREAM WOULD HAVE PURE WATER WHICH WOULD BE OF A QUALITY OF A RO WATER SAFE FOR REUSING IT IN THE RINSE WATER APPLICATION AGAIN AND AGAIN.
2. (REJECT) SECOND STREAM WOULD HAVE ALL THE CONTAMINANTS LIKE COPPER SULPHATE, ZINC SULPHATES AND FREE ACID. THIS STREAM WOULD BE USED TO TOP UP OUR PICKLING ACID BATH. (FROM WHICH THE METALS ARE RECOVERED THROUGH THE ELCTROWINNING PROCESS.
ARE SUCH SYSTEM AVAILABLE OR THEY ARE JUST RUMOURS IN THE MARKET ABOUT THEIR AVAILABILITY.
THANKS IN ADVANCE AND BEST REGARDS,
COPPER AND BRASS PICKLING - INDIA
2005
Dear Mr.Vidu Goyal.
There is a new method to treat these wastewaters without chemicals, and without resins or membranes.
There is electro-catalytic precipitation, using only electrical power, oxygen and lot of inteligence.
The results are solide oxides and minerals, wich can be filtered by media filters or bag filters and reuse it like you think or landfill and the water will be almost distilated water. If you need high purity water you can add a RO unit or other membrane or resin technology to filtrate it to the molecular level.
- Constanta, Romania
What you are describing sounds like a typical Reverse Osmosis (RO) water system. It works by passing the impure water through an extremely fine filter that only allows water molecules through. Any contaminants are concentrated on the input side of the filter and they are flushed away to drain after a certain concentration is reached. The resultant water is very pure, but has to be continually recirculated to prevent a build-up of dissolved gases. It also needs to be UV treated to prevent algae build-up. The system is only about 90% efficient as you need to discard the concentrated waste water. Furthermore, since the water is produced by reverse osmosis, you need a pressure pump and the rate of generation is not very fast. It is a relatively expensive way of producing pure water, but it is very good.
If I were you, I would look at de-ionising systems, but since you have oil present, you will need to have a very good prefilter bed. This is cheaper than RO and produces water faster. All you need to do is regenerate the resins with sodium hydroxide and hydrochloric acid. You can also improve your water consumption by using sophisticated rinse systems such as counterflow, where the rinsing water is used more than once. In these cases, the pure water is used as the final rinse, but once it has been used, it is re-used as the "final but one" rinse, and so on. Consequently, as the water becomes more contaminated with rinsing, it is used for less critical rinse stages until it is so dirty it needs reprocessing. It is called
"counterflow" because the water flows in the opposite direction to the production line.
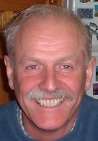
Trevor Crichton
R&D practical scientist
Chesham, Bucks, UK
2005
Mr. Dinu,
You make several of these same claims in most of the responses you enter for the ECP technology. Would you please care to explain how exactly your technology works on all of these applications so effectively? Could you provide some relevant operational data or at least some reasonably balanced chemical equations to support these claims? If you could further explain how your technology removes anion counter-ions from solutions as "minerals" it would be appreciated by many of the readership that see's your responses, including many of us that have 20+ years in the environmental business are at a loss to explain. If this is your own technology, or you are a licensee of such, could you please provide the US or European Patent numbers for the technology? I think that as you have chosen this forum to promote this technology, we should all have the ability to know more about it so we may judge relevant applicability to each of these instances in a more enlightened manner. Please direct us to any relevant web site where technical information can be readily found. Thank you in advance.
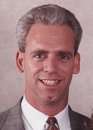
Tom Baker
wastewater treatment specialist - Warminster, Pennsylvania
2005
The one thing that your posting does not say is what the overall water flow is in the rinses from this process. I am surprised when looking at the analysis you list that the pH is at 5. Further, it is also difficult to say why with 60 mg/L of TSS, your water is "colourless" - that does not reasonably align with your application well. However... The use of ion exchange as a direct water recycling application is not, in my opinion, a good fit here. The primary issue I see is that the TDS is extremely high - too high for a water recycling approach. It should be noted that a proper review of this statement, however, should include an analysis of the water you use to feed the rinses as well, as this is also a contributary portion of the overall TDS in the effluent rinse water. In otherwords, a case could be made to use IX as a technology is the TDS was artificially high in the raw water, and not from the carry-over from the process itself.
A more reasonable approach to this may be the use of a scavenging ion exchange to remove metals first, and then consider the use of a membrane system (recycling reverse osmosis - which DOES DIFFER from potable water or brackish water RO applications. In this approach, the metals would be regenerated from the ion exchange columns and treated separately. The concentrate discharge from the RO would give you a high salt concentration stream that can be discharged, as the metals have been removed separately. You could reasonably expect to get 70-80% reclaim of the water in this approach as a relatively low TDS (<30 mg/L) return stream to the process.
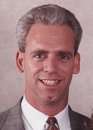
Tom Baker
wastewater treatment specialist - Warminster, Pennsylvania
2005
2005
OK. It is not a problem.
The description it is too long for this forum presentation but you can read about in my web page www.ingo-prod.ro. My company is the eastern-european dealer of the US company ECP International, LLC, which is the owner of the patent.
I can send you some analysis made to the different wastewaters using one ECP unit. The entire technology it is stated to a group(block) of the ECP units, parallels or serials, mathematically calculated, that way, the result to be the purposed one.
I must ask the permission of my principal from US, to show you this confidential data about lab analysis. The data are confidential for the base client, hope you understand it.
We have lots applications in the 4 US states, South Africa, Canada and Scotland, for different fields, like mining wastewater, hog manure wastewater, food industry, oil industry and we already have designed a wwtp for a Russian aluminium anodising plant for 90 cbm/h, and hope to be enough money to do it and to demonstrate the high quality of this technology.
We hope to help lots people with our ECP technology and save the earth's health.
I am awaiting your questions after you'll read the web presentation.
Regards.
- Constanta, Romania
2005
I looked at the information on the web site as you suggested. Please allow me to provide to you a background, if I may.
I have extensive training in electrochemistry over the last 26 years. I was privileged enough to be able to work with Dr. Leslie Lancy, who was for all intensive purposes, the "grandfather" of the use of electrolytic methods for pollution control. Our company does have a similar technology to this, however we would NEVER make the broad claims that you do on behalf of your company and your licensor. Electrochemical oxidation technology is well over 50 years old, so the approach is not unique. The fairly recent development of some catalyst coatings has resulted in the ability to create oxidation compounds at the electrode interfaces that can impart oxidation of some of the compounds in solutions. Usually, these are oxygen derivatives, such as ozone, peroxides, and other compounds that have extremely short half-lives beyond the instance of creation. New to this "technology" is the use of electrochemical oxidation that can produce "free radical hydroxyl" (FRH) ions. As the web site states, it has an extremely high oxidation potential. (By the way, the web site incorrectly states that "fluoride" has the highest oxidation potential. Fluoride has essentially none, fluorine gas is the correct compound, and actually, that is lower than FRH under most circumstances.)
Coatings that are capable of making these compounds are in almost every case, electrochemically inefficient, much more so than 'typical' platinum group metal coatings that are used. They require greater current densities to produce the compounds than these PGM coatings can operate in without severe accelerated loss of thickness. In other words, they use 100% of the electrical current to make approximately 55-65% of the theoretical equivalent amount of the compound desired. The effectiveness of the oxidation compound is further reduced by the actual oxidative efficiency of the process, including losses to atmosphere of gaseous products, and recombination of unstable products to more stable compounds that have no effect on the desired outcome. A side note that should be mentioned is that these also will make, in the presence of chloride, a fairly significant amount of not only chlorine gas, but because they use such high currents, also make chlorates - which are highly toxic. In typical metal finishing applications, there is usually a fairly high degree of chloride in the water, and as such, their use in the applications that you suggest may trade the partial removal for the creation of more toxic issues.
FRH is largely unproven, with exception of the oxidation of some organics, such as BETX, MTBE, and others. However, the cost to both manufacture the FRH in solution is typically several orders of magnitudes higher than conventional technologies. On one hand, the FRH compounds are effective at the electrode interface, however they do not last long - perhaps a matter if milliseconds in solution. this is largely unknown, as it is almost impossible to analyze for these in water, as water as a solute has no capacity to carry them as a dissolved component, and they are so unstable that they simply recombine with available hydrogen in water to reform water molecules.
Much of the information on the web site is based on organic removal and what is even stated as partial removal of some ions, such as phosphates (~60%), which is not relevant to this forum typically.
Very little information is provided to support the broad range of applications you answer to in this forum, and in fact, based on my experience using electrochemical oxidation technology over the last 2+ decades, your claims are wildly speculative at best. Many of the professionals that use this site for advice take information provided and spend countless hours of their and their employer's time and money researching technology approaches to their issues. That is why we question certain postings about technologies. As an employer, wrong information that takes up my employee's time and efforts costs me money. The "fits all" approaches that you post on here I believe are injurious to those that use the forum for this purpose. But that is my opinion.
I'm sure we all can look forward to seeing your data posting. If there is good relevant data, I'll be the first one to say so publicly. Maybe Ted can give you your own soapbox on here to initiate a more vigorous discussion. Let me assure you that I will defend your technology if I see it merited, as I have always been a proponent of electrochemical treatment that has been properly applied. Otherwise, I see it as a way that denigrates the technology broadly based on misapplication.
As we say here, show me the money.
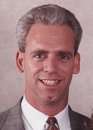
Tom Baker
wastewater treatment specialist - Warminster, Pennsylvania
2005
Getting back to the original question: This is a possible application for a nanofiltration system.
At pH 5, the membrane has a negative charge on it, and will strongly reject all divalent anions, such as , and especially, sulphates. You need to keep the reject in a recycle loop, such that the unpaired sulphates bring the pH of the concentrate down to a point, when there will be a polarity change in the membrane, which will now reject the zinc and iron as divalent cations, and allow the sulphates to go through as monovalent HSO4 ions. Tricky, but I've been there done that. If you need help designing, post the request, and I shall respond.
As far as the other argument in this string, I had given the patent # for the ECP in a string related to ammonia removal [Ed. note, see letter 33695]. I have been trying to technically qualify the technology for textile dye removal and other contaminant removal in textile and tannery wastewater plants. My data suggests no better results than using any source of chlorides for anodic oxidation. However, I was grilled for my criticism earlier
[Ed. note, letter 33977], so I will stop right here on this discussion.
- Brea, California
Vidu,
My company builds wastewater recycling systems in several technologies. It is not possible to generate an educated proposal without more information. If you will click on my link at the bottom of this response I will be glad to research this application and help you determine the most appropriate technology. Membranes have their place, and this looks like a viable application for that, and the IX idea is a good one if you need to remove the metals. Let's discuss this and see if we can come up with an efficient solution.
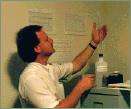
Jeff Watson
- Pearland, Texas
2005
I must say AMEN to Tom Baker's last post. As a manufacturer of electrolytic treatment systems I spend most of my time trying to overcome misinformation provided by those who claim to have found the Holy Grail by using electrolytic treatment processes. One correction -- it has been around over one hundred years.
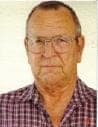
Paul Morkovsky
- Shiner, Texas, USA
2005
Ed. note: And as the editor, we say a qualified amen. We encourage everyone to challenge anything they see on these pages, but to do so in a respectful way. No slams, no ad hominem attacks, just "Sorry, but I don't think that's accurate because . . ." :-)
Q, A, or Comment on THIS thread -or- Start a NEW Thread