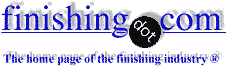
-----
Sulphate Removal, Wastewater Treatment, Recycling in Anodizing & Plating
Q. Dears,
We have anodizing plating company in Iran; we have 2000 lit/day waste water. We treat this with below :
pH: 2
Add FeCl2, then add NaOH or lime to get the pH:10, then add barium carbonate and floc (pristol), but until we have 2000 ppm sulphate. Please guide us.
Thanks
- Iran tehran
September 14, 2021
A. Hi Saeed. I don't personally agree with the barium carbonate treatment -- I don't think it's a reasonable way, and maybe not even a safe way to reduce sulphate in waste water.
I think source reduction, plus always using lime rather than NaOH, are better approaches. But if you are going to use barium carbonate anyway, then always precipitate with lime, never NaOH.
A very good summary of all the ways to reduce sulphate in waste water can be found at
https://www.wateronline.com/doc/sulphate-removal-technologies-a-review-0001
Luck & Regards,
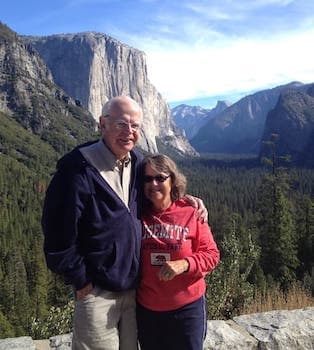
Ted Mooney, P.E. RET
Striving to live Aloha
finishing.com - Pine Beach, New Jersey
September 2021
⇩ Related postings, oldest first ⇩
Q. What is the maximum concentration of Sulphate (SO4) permitted in the aluminum anodizing effluent in your country?
Here we have a limit of 1200 ppm. Despite the availability of H2SO4 recycling (purification) system which works well, SO4 conc. is between 1500-1700 ppm after waste water treatment. (We do not use Ba additive).
aluminum extrusions & finishing - Istanbul, Turkey
1998
A. In Australia the limit of sulphate as SO4 is usually allowed to be as high as the saturation point of Calcium sulphate in water, which runs out to be in the order you have quoted. Using Barium would, I suspect, be prohibitively expensive.
Regards

John Tenison - Woods
- Victoria Australia
1998
A. Timur: you should probably use lime for your wastewater treatment, which should reduce the sulphate at point of treatment to about 2400 ppm (based on the solubility of calcium sulphate in water). If you then end up diluting it by mixing this treatment stream with other streams, you will hopefully reach your 1200 ppm.
John: Kudos to Australia for a well-reasoned approach!
Regards,
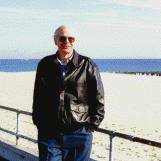
Ted Mooney, P.E.
Striving to live Aloha
finishing.com - Pine Beach, New Jersey
Postscript added a few years later ...
opinion! It drives me loony when regulators pick discharge limits slightly lower than a sound approach to wastewater treatment can reliably deliver, necessitating foolish ideas like Barium additions, where the cure is far worse than the disease. It's just so irresponsible. Consider the White River fish kill [Indiana, 1999]:
The worst fish kill in the history of the plating industry wasn't caused by untreated waste nor poorly treated plating waste nor by a midnight dumper ... but by discharge of DTC, a WASTEWATER TREATMENT CHEMICAL that no plating shop wishes to buy, no plating shop wants to use, no plating shop wants on hand -- horrible dangerous crap which is required to remove an extra fraction of a milligram, because of beyond-the-point-of-diminishing-returns STUPID effluent standards :-)
When a regulation requires the use of exotic and extremely dangerous chemicals, it really needs to be examined so we don't continue to legislate disasters like the White River fish kill into existence. But instead of the regulators taking 10% or even 2% of the responsibility and questioning their approach, they circled the wagons; it looks like no one in this country learned anything whatsoever from the disaster. I certainly hope other countries will follow Australia's lead, not America's.
Recycling of Anodizing Plant Wastewater
Q. We are currently treating and dumping to drain our waste rinse water from an anodise plant. Being mainly deionized water from the rinse tank overflow with the occasional regen waste from the deionizing plant, the quality of the waste water is excellent and we are never anywhere close to our outflow limits.
The water costs are pretty huge. For this reason we are looking at returning the effluent back as feed water to our deionizing plant.
Has anyone any experience with this and can they give me some pointers as to things to avoid or do?
Thanks
- Great Britain
2002
A. We have installed many successful water recycling systems in anodising and other plating and finishing applications. In nearly all cases, however, we segregate the rinses that are both chemically compatible, and low enough in Total dissolved solids for the system to operate economically. This usually means that we recycle the rinses before they go to conventional treatment.
The reasons for this are that any chemicals that you add cost money to remove, and also you need to have some place to send the concentrated regenerates. Thirdly, it is also expensive to operate a wastewater treatment system, so by recycling the water before treatment, you save the treatment cost as well as the cost of the water. While your wastewater may be very low in regulated metals, it may not be so low in total dissolved solids. Typically, a DI system is not economical at a TDS concentration of > 600 mg/l; at > 600 mg/l a membrane system becomes more economical.
If you still want to proceed with recycling after treatment, please install a conductivity control and diverter valve in front of the recycling system to divert any high TDS flows away from it. If you monitor the conductivity or TDS of your wastewater for a while, this will tell you the normal range and variability.
I think that you will find that segregated rinse streams are a lot more consistent in chemical composition and TDS concentration than your treated water, and would be a better place to begin recycling.
Good Luck!
consultant - Cleveland Heights, Ohio
2002
A. My experience in Southern California, where water is always at a premium, is that it's cheaper to buy water than to try and recycle it through a treatment system. It's also a lot less hassle. Obviously, you have to buy a system that will match your flow rate. If you have problems and need to reduce your flow rate, your TDS will go up and cause more problems in your IO or RO system. Watch out about reducing your flow rate because if you do, your local enforcement agency will accuse you of treating by dilution if you decide to turn it back up. If you are nowhere near your discharge limits and don't have a TDS limitation, just discharge it and count your blessings.
Guy Lesterplating co. - Ontario, California, USA
2002
A. We have put together dozens of water recycling systems for metal finishing plants, including anodizing facilities, and there is always justification for recycling the resource. Unless your water comes from the tap as DI, your product quality improves dramatically with it, and recycled water can easily be reconverted back to DI if the streams are segregated and care is taken in the process line operation. At an average cost to make DI water of $2.15/1000 gallons, and a treatment cost of $8.50/1000 gallons, the positive payback is easily realized when you can make recycle water for less than $1.50/gallon.
System design, good maintenance procedures, and a vendor familiar in your facility operations and the finishing process make all the difference in the world to integrate the system into your fluid management process seamlessly. If you're trying to do it yourself and do not know how, or the impact or good design for the equipment, you're going to reap a bitter harvest.
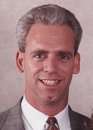
Tom Baker
wastewater treatment specialist - Warminster, Pennsylvania
2002
A. In the UK we have found that the best use of this overflow is to cascade to other washes, but you need to know impurity tolerances of your process tanks. We have a fairly good handle on these for most aluminium treatments.
Richard HutchinsonYork, England
2002
Wastewater constituents resulting from color anodizing
Q. I will do my paper in university about anodizing wastewater. I want to know what components are in color anodizing? Is copper in there? I had read in handbooks that components of anodizing color (red satin) are copper sulphate, ammonia and water. Is it right? Thank you for your answer.
Ajeng Arum SariEnvironmental Engineering, Dipoegoro University - Semarang, Central Java, Indonesia
2005
A. Hi Ajeng. The most obvious potential pollutants are the caustic in the cleaner and etch tank, the desmut chemical which might be nitric acid but might also be something else depending on the alloy of aluminum that is being processed, and the sulfuric acid from the anodizing tank. The dye tanks are usually simple organic dyes that are not much of a problem. After the dye, the component must be sealed, which will usually involve nickel acetate.
The other source of contamination is the dissolved aluminum alloy which, yes, will often introduce copper. I'm personally not aware of ammonia being in anodizing wastewater.
Regards,
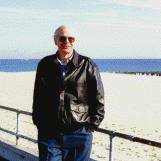
Ted Mooney, P.E.
Striving to live Aloha
finishing.com - Pine Beach, New Jersey
2005
Multiple threads merged: please forgive chronology errors and repetition 🙂
Q. I have been struggling with different aspects of a small type II anodizing line which I am building. Most of the equipment in regards to the production is in place, however, before I go ahead and get ready to start running I have some concerns that have been in the back of my mind from day one. I wish to touch on the environmental issues and questions. My concerns are as follows :
1. Concerning air pollution, is a fume scrubber required in regards to the anodizing (electrolyte) tank? Note that I am NOT utilizing a bright dip process where a fume scrubber is obviously a requirement.
2. Regarding the ultra fine acid based mist that is produced while anodizing, is a simple bath additive sufficient in order to reduce/eliminate environmental corrosion? What I mean is, if an additive such as "Ekaline F Liquid" that Clariant sells (or an additive of this type - foam forming) is utilized in a processing tank, would the environment contamination (corrosion of the work place and nearby machinery) be reduced/eliminated?
3. With regards to waste rinse waters and their disposal, is it correct to believe that simply boiling these waste waters (accumulated throughout the entire line) away would be a bad idea? By boiling waste water to 100% evaporation, what negative impact would this have on the environment?
4. What is the best method of waste water disposal?
As always I would like to thank everyone who responds in advance. Your aid is greatly appreciated. Though my line is near completion, I want to make certain that my operation leaves no negative impact on the environment. I realize that rules and regulations change from state to state and country to country and I also realize that being able to comment on such rules and regulations may be difficult unless you are from the area in which I work. Quotes on rules and regulations are not what I seek today. Thanks everyone!
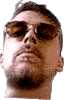
Daniel DeGueldre
anodizing shop entrepreneur - Ste. Anne, Manitoba, Canada
2005
A. I am not familiar with the laws and regulations in Canada, but I believe they are similar to those in the USA. I'll try to answer some of your questions as the laws and regs here would apply, but you'll have to see what the differences are as applies in Canada.
For a small shop such as yours it may not be necessary to have an exhaust system per se. I'm not familiar with the Clariant product, but there are fume supressants which greatly reduce fume/spray from anodizing. You will still have some fume, and you'll have steam from the heated tanks, but general room ventilation may suffice. The problem here, and I expect there too is this: There are limits as to what quantities you can release to air. A small operation may not violate these limits, even without fume scrubbers or other devices, but the burden is on you to prove that this is so. This can be done by engineering calculations rather than actual measurements. You will need someone who is qualified (and in the USA is a Registered Professional Engineer) to do this work and file the necessary paperwork. If the engineering calculations indicate that you will violate the air regulations, then you will need an exhaust system with fume scrubber. Again, this will have to be designed by a recognized professional.
You will have waste water to discharge. I assume you will discharge to a POTW. If so, then that POTW will have sewer use ordinance which limits the character of discharges. It will certainly limit pH, metals, COD, total solids, and maybe some others. This means that you will need a discharge permit from the POTW before you discharge the first gallon, and you will have some monitoring and reporting requirements. You may also have to install some sort of pretreatment system to bring your discharge into compliance with the POTW limits. Again, this will have to be designed by a recognized professional. I think it is essential that you establish a relationship with the POTW. There is nothing which will get you in trouble more quickly than discharging without their knowledge and permission. They will help you work through the regs, although you will almost certainly need the help of a consultant. Doing the actual work of anodizing ids the fun part. In many ways it is also the easiest part, and it may even be the cheapest part.
Environmental compliance is not much fun, is very consuming, and can be expensive. Metal finishing shops go out of business every day. Almost none of them go under because they don't know how to do the work, but many are put under by environmental violations. Please get an experienced consultant to help you through all of this. It will be money very well spent.
Just to follow up a bit more. Evaporation of waste water is probably not going to be the best approach. Evaporation of a significant quantity of water will require a lot of energy and cost. Even if you evaporate all of the water, you will still have the chemical residue left, and will have to dispose of that, and pay for the disposal. Probably better to get a discharge permit and dispose to POTW. The other choices are to dispose to a septic system, which is probably illegal, or to a stream, which will require more pretreatment and expense than discharge to a POTW, and, if you have a problem, could result in a fish kill...bad thing.
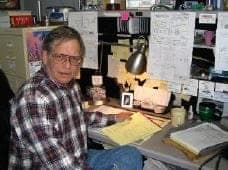
Jeffrey Holmes, CEF
Spartanburg, South Carolina
2005
A. Three things you might want to consider:
1) You will probably want to be set up for chromating, or "Alodine." Some of these products contain iron cyanides as catalysts. These are not amenable to chlorination and are quite difficult to remove. I would avoid using such products if possible.
2) Here in the USA, we have a special solid waste category, F019, for chromium bearing sludges resulting from the chromating of aluminum. If it is possible to segregate such wastes, you may find that it is possible to dispose of your other solid residuals at a much lower cost.
3) Traditionally, the solution used to seal the anodized surface contains nickel and/or cobalt. However, there are seal formulations that do not contain regulated metals. You might want to look at those.
Good luck!
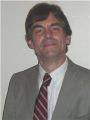
Dave Wichern
Consultant - The Bronx, New York
2005
Recovery of aluminium anodizing sludge
Q. Hi.
I am just wondering what would be the easiest method to reuse aluminum anodize sludge as a flocculant or any other simple procedure that can be used to reuse anodizing waste?
student - New Zealand
2007
A. Typically there is no "sludge" from the anodizing tanks. Baths are typically decanted on a regular basis to keep the Al content at an acceptable level. Al is not a regulated material, so the decanted solution is normally ph adjusted, and discharged to sewer.
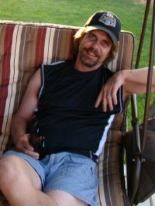
Marc Green
anodizer - Boise, Idaho
2007
A. If you anodize a fair amount of 2000 or 7000 series aluminum alloy, you very probably will exceed the amount of copper that you are allowed to go to the sanitary sewer with.
James Watts- Navarre, Florida
2007
A. Luckily, for me, I deal almost exclusively with 6061, and 5052 alloys for the semiconductor industry. But you are correct, James, without some type of filtering, it's very possible to exceed Cu limits in the bath.
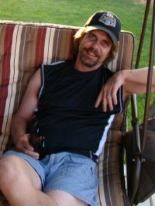
Marc Green
anodizer - Boise, Idaho
2007
Sulphate removal from effluent
2007Q. I am a master-student and I am trying to make a thesis about sulphate removal, I am working on a wastewater with 30,000 mg/L COD and 8,000 mg/L SO4 concentrations, the full-scale treatment plant is not working which contains an UASB, aerobic ponds and chemical treatment, I have pilot reactors for UASB and Aerobic treatment phases. In full-scale the UASB reactor was not working so I am trying to make it work in UASB, but I am not sure of it so I need some help about getting rid of those sulphate except using BaCl2. I hope someone could help me.
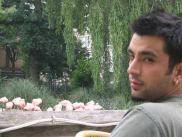
Serkan YUKSEL
Student - Istanbul, TURKEY
A. Hi. Treating the waste with lime first should cut the sulphate down to about 2400 ppm. Good luck.
Regards,
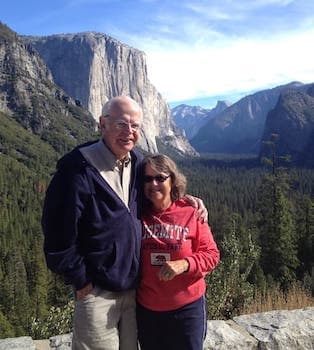
Ted Mooney, P.E. RET
Striving to live Aloha
finishing.com - Pine Beach, New Jersey
2007
Q. Hi, any help with this long-winded inquiry would be gratefully received!
I'm a process engineer who has been called in to provide advice to a company that chrome plates metal components for aircraft manufacture. My inorganic chemistry is very rusty and help would really be appreciated with this one.
The company in question has small effluent plant consisting of reduction with sodium bisulphite, precipitation with sodium hydroxide, clarification and sludge dewatering via a filter press. ferrous sulfate
⇦ on
eBay or
Amazon [affil links] and a number of polyelectrolytes are also added.
The effluent plant was installed in 1989 and has had little work (including calibration of instruments, pump maintenance etc) carried out since.
The treated effluent from this plant passes to a public sewer and is conveyed to a local wastewater treatment works. The local water company enforces a consent (permit) on the treated chromium effluent and one of the parameters of concern is sulphate. Several breaches of the maximum sulphate level have occurred recently. The company's record-keeping is poor and it has proved difficult to tie-in the sulphate problems with production at the site. Interestingly they have never exceeded their chromium consent level. The maximum sulphate concentration they are allowed to discharge is 1,400 mg/l.
The question is: could poor reaction conditions be a cause of the excess sulphate in the effluent? I'd like to present, if possible, a well-founded theoretical argument to the customer showing how the excess sulphate could appear in the effluent.Any other opinions?
Many thanks!
Process engineering consultant (wastewater treatment) - Peterborough, UK
A. Although sulphate is precipitated with barium carbonate in chrome plating tanks, and it is probably theoretically possible end-of-pipe, it doesn't sound remotely practical and nobody would do it to my knowledge. Rather, sulphate is considered a soluble radical that must be limited in the influent rather than removed by wastewater treatment. The source is more likely a sulfuric acid treatment tank than the chrome plating tank itself. Just my guess based on limited data, and second opinions are welcome.
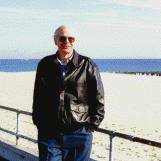
Ted Mooney, P.E.
Striving to live Aloha
finishing.com - Pine Beach, New Jersey
2007
A. Since sulphates are extremely soluble, they must come from either your process chemistries or from the chemicals that you are using for treatment.
You mentioned sodium bisulfite, which is oxidized to sulphate, and ferrous sulfate
⇦ on
eBay or
Amazon [affil links] being added. If there are no sulphates from other process chemistries, like a sulfuric acid dip, then you may need to reduce the amount of ferrous sulfate
⇦ on
eBay or
Amazon [affil links] added as a coagulant, or change coagulants to something without sulphates, like ferrous chloride, polyaluminum chloride, etc.
It is unlikely that there are significant sulphates in your chrome plating solution since the ratio of chromic acid to sulphate is usually > 100:1.
consultant - Cleveland Heights, Ohio
2007
A. My approach to this problem would be to try to reclaim some of the chromic acid.
Using an evaporator, concentrate the first rinse until it is at least 25% of the bath strength. Now, run a "porous pot purifier" in it to re-oxidixe trivalent Cr, and remove tramp nickel, copper, iron, etc. Then, use it as make up for the production tank.
Chromate could also be removed with an ion exchange resin, but to reclaim chromic acid would require a second ion exchange column, to exchange the Na+ or K+ from the regenerant for H+.
Another approach would be to try a reducing agent that does not generate sulphate. One could use ferrous chloride, at the expense of a vast increase in solids generation. Hydrazine has been used, but it is quite toxic. Lastly, there is electrolytic reduction with sacrificial iron cathodes. That might work, but it'd also be a big solids generator.
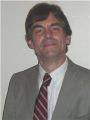
Dave Wichern
Consultant - The Bronx, New York
2007
A. Calcium sulphate is fairly insoluble, so use lime as the neutralizer or add Calcium chloride to ppt. the sulphate.
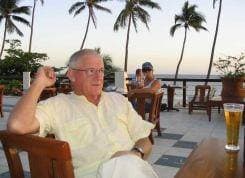
Geoffrey Whitelaw
- Port Melbourne, Australia
2007
Many thanks for your responses. I think my rusty chemistry was along the right lines and I'm very grateful for the replies, they've been very helpful. Any other replies would also be gratefully received.
Many thanks again.
- Peterborough, UK
2007
It is not possible to give a definitive answer without in-depth knowledge of the process, available plant etc.
On the evidence you have given, I would suggest simply replacing the sodium hydroxide with lime. It offers a significant cost saving and removes sulphate.
Your other comments suggests that the client needs to tighten up their act in other areas as well.
Barium salts are both expensive and toxic.
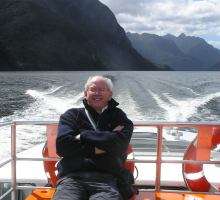
Geoff Smith
Hampshire, England
2007
Q. I am trying to set up a large (300+ gallons) anodizing facility for the first time. I was wondering if there are any laws that I need to know about. I have seen people mention the F019 Hazardous Waste laws. Are there any more?
Thanks in Advance,
- Albany, New York, USA
August 20, 2012
A. Hi Max.
It's a highly regulated industry; in fact plating and anodizing were our nation's first categorically regulated industry. Before the EPA existed, the Department of the Interior decided that plating and anodizing needed regulating, so implementing the proposed effluent standards was one of EPA's first jobs. EPA 40CFR413 might be a good starting point, but it would be worthwhile to consider retaining an anodizing consultant.
You might also contact the National Association For Surface Finishing (www.nasf.org) which sold an NAMF "Compliance Manual" -- not sure if they still have it, but some plating/anodizing shop in your area will have it if not, and I'm sure it would be helpful. Good luck.
Regards,
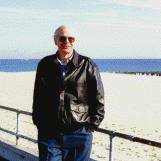
Ted Mooney, P.E.
Striving to live Aloha
finishing.com - Pine Beach, New Jersey
August 20, 2012
A. You'll also need to contact your P.O.T.W. and obtain a discharge permit. They will also require you to test your effluent for certain metals, and have other regulations you must adhere to outside of the EPA regs. Typically these guys enforce the rules/laws enacted by the D.E.Q.
You'll need to do this prior to anodizing any parts.
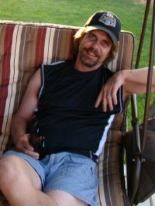
Marc Green
anodizer - Boise, Idaho
August 21, 2012
Q. Hi friends,
My question is am dealing with hard anodizing using Sulfuric acid, and I have both alkali and acidic collection, so is it necessary to collect acidic and alkali separately? Can we not collect both acidic and alkali in one tank instead of collecting separately?
- Abu Dhabi, UAE
February 24, 2014
A. Hi Aijazullah,
It really comes down to the concentration of your acids and alkalis.
If the solutions are sufficiently dilute the exotherm from reaction will be small and the reaction should not be violent. If the acids and alkalis are concentrated or of a high enough concentration you will have a very vigorous exothermic reaction, which may well cause you all sorts of problems.
Before you do anything I would trial in the lab before I decided to do anything, that way the reaction can be done with very small quantities of your waste products in a controlled environment.
Aerospace - Yeovil, Somerset, UK
February 25, 2014
Wastewater issues in type 2 anodizing
December 20, 2014Q. Hi I been lurking in this forum for some time now. We operate a small type 2 anodizing line and do small production and custom work. It started as a hobby and has since grown into a decent business. As we grow I have a lot of questions coming up that I think about daily.
1. Our shop has a septic system. What can I do with my rinse water without having to install a very expensive treatment system?
2. If I were to move to a commercial property with a sewer system, where do I learn about regulations involved with waste water disposal in public water system?
Just to be clear I don't expect anyone to answer all the rules but mostly where I can learn about them.
3. With our custom work we use a lot of masking and use mineral spirits
⇦ on
eBay
or
Amazon [affil links]
to remove it. Will a mid temp/cool sealer seal properly after having been through masking and removal?
4. We have a heck of a time properly cleaning parts well. We have tried a hobbyist degreaser which sucks. We tried sonic cleaning with limited success. We currently have to scrub each part by hand and then sonic clean which is very time consuming and we still have issues from time to time.
5. Recommendations on where I can learn about being a proper commercial anodizing shop?
I feel we are at a tipping point and need to become a really proper shop and have no idea where to turn for info.
archery supply - Machesney Park Illinois
Hi Travis. This site has been online for two decades, and despite talking about such issues many times, I've never heard of the EPA or local authorities lowering the boom on a hobbyist, an artist/sculptor, or a custom jewelry seller who plates jewelry or flowers. But if you're in business, you're theoretically subject to the regulations, so it's a matter of deciding to do things right before you get big enough to attract the attention of the regulators.
1. Most of the wastewater from anodizing contains large amounts of dissolved aluminum, which is usually not regulated per se, and not too much other stuff as long as you adjust the pH to neutral so you're not discharging acids or alkalis. But there are some other troublesome things in it like copper, so the discharge of wastewater from anodizing shops is "categorically" regulated -- meaning it's regulated because it's from a plating or anodizing shop regardless of whether the discharge is harmless or toxic.
2. Usually your local POTW is who you need to talk to. They are familiar with the federal laws and charged by the feds with enforcing the effluent standards for the industries discharging to them. Find out who your local POTW is, and ask to talk to someone about your plan to move to a commercial/industrial property and ask them what you need to do to comply.
3. I'll defer to an experienced anodizer on your sealing after masking removal question.
4. Cleaning is the hardest part of most metal finishing operations. There is nothing wrong with scrubbing with pumice and detergent, or using ultrasonic cleaning, but it is possible than a company specializing in anodizing chemistry can find you a better cleaner so you don't have to.
Regards,
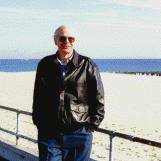
Ted Mooney, P.E.
Striving to live Aloha
finishing.com - Pine Beach, New Jersey
Q. Hi,
Is there any easy way to remove sulphates from effluents to get a concentration below 1,000 ppm?
Other contaminants in the stream are chrome, nickel and copper. They are currently removed by precipitation as hydroxides - but the stream containing sulphates could be separated to an alternative treatment system if needed.
- Manchester, UK
July 3, 2014
A. Hi Tomas. We appended your inquiry to a thread where this is discussed, and which seems to indicate that the best strategy is to isolate the source of sulphate (as you say you can do), treat with lime (to get to about 2400 ppm), and then mix it back in to dilute it to below 1000 ppm. Good luck.
Regards,
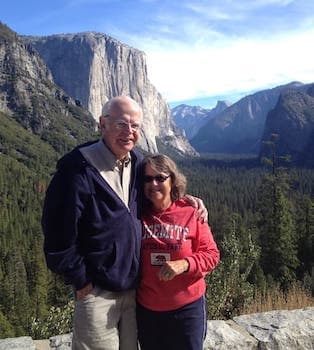
Ted Mooney, P.E. RET
Striving to live Aloha
finishing.com - Pine Beach, New Jersey
Q. I work in an anodizing plant as an engineer. We have a sulphate problem in waste water treatment. When we analysed discharge water's (effluent) for sulphate, we find sometimes higher than the 1700 ppm municipality effluent discharge limit. How can we get rid of this problem?
Alaattin tuna- sakarya,turkey
December 3, 2015
A. Hi Alaattin. Can you isolate the sulphate-bearing waste, treat it with lime to get it in the neighborhood of 2400 ppm, then mix it with the other waste to reduce the concentration to below 1700 ppm?
Regards,
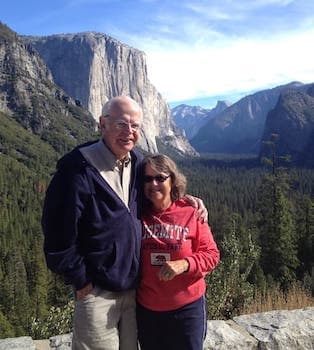
Ted Mooney, P.E. RET
Striving to live Aloha
finishing.com - Pine Beach, New Jersey
December 2015
----
Ed. note: CIE (Compagnia Italiana Ecologia) offers their Pural technology for sulphate removal which you might want to investigate. Due to the anonymous nature of these pages, and several other good reasons, we neither praise nor criticize specific proprietary approaches, we just mention their existence :-)
High sulphate in nickel-chrome plating plant wastewater
May 2, 2018Q. Hello, I have a problem to contain the sulphate level in wastewater.
the wastewater arrives from the chrome-plating plant, and comes from degreasing rinse, nickel rinse, and chromium rinse.
The water is treated with sulfuric acid to lower pH to 2,5; sodium bisulfite is used to reduce chromium from hexavalent to trivalent. Then we add ferric cloride.
Next step is add lime to increase the pH up to 11 pH.
Next step is flocculant and in the end we lower pH again with sulfuric acid to 9 pH.
I have lot of problems to keep the sulphate level under control.
Any advice?
Thanks
- Italy
A. Hi Corrado. It is usually useful to track or at least estimate where the sulphate is coming from to see if usage can be reduced and to find the most worthwhile targets.
As Lyle Kirman noted earlier, the amount of sulphate in the chromium rinses is probably not significant. However, you may be adding a lot of unnecessary sulphate in its treatment. If you're not reducing the hex chrome to trivalent before mixing the chrome waste with other waste, you are adding a lot of sulphates via sulfuric acid to unnecessarily lower the pH of the other waste because only the chrome rinses need the pH to be reduced. Further, if you have enough retention time, it may not be necessary to go all the way to pH 2.5; I have seen hex chrome reduced to tri chrome with bisulphite at a pH of 4.5 if you have enough reaction time.
A lot of sulphate comes from the nickel rinses, and since nickel operates at 140 °F (60 °C) it is usually relatively simple to get a good part of that sulphate-rich plating solution back into the tank to make good evaporation losses.
Regards,
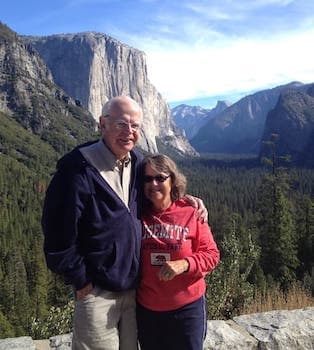
Ted Mooney, P.E. RET
Striving to live Aloha
finishing.com - Pine Beach, New Jersey
May 2018
Q. Hello Ted, yes the quantity of sulphate from the plating plant is very low (we're talking about 3-400 ppm).
So I add all those with sulfuric acid. But is it normal that no sulphate precipitates with metals and then lime?
It looks like all the sulphate I add I get then in the end of my purified effluent water.
My reaction time is about 40 minutes (1500 l/h in a tank of 1000 l).
So to be sure I work at 2.5 pH.
I also tried to increase the pH or increase the mV redox (to reduce bisulphite), but I had no significant results.
- Italy Europe
May 2, 2018
A. Hi again Corrado. I am still not understanding whether you are reducing all of your wastewater to pH 2.5, or only the 1/3 part of it which comes from the chromium rinses. Try a test beaker [beakers on eBay or Amazon [affil links] in the laboratory to see if you can reduce the hex chrome at a higher pH than 2.5 within 40 minutes. Good luck.
Regards,
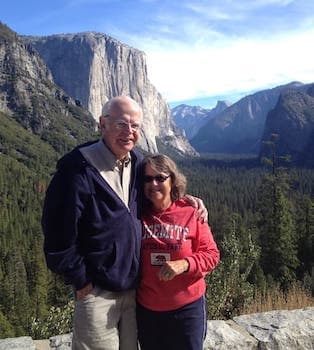
Ted Mooney, P.E. RET
Striving to live Aloha
finishing.com - Pine Beach, New Jersey
May 2018
Q, A, or Comment on THIS thread -or- Start a NEW Thread