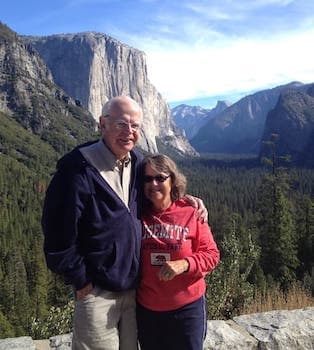
Curated with aloha by
Ted Mooney, P.E. RET
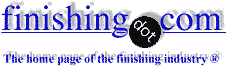
The authoritative public forum
for Metal Finishing 1989-2025
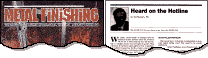
-----
Corrosion of 302 vs. 303
We are currently manufacturing a stainless steel rivet that is used on a product line of ours. The material is type 303 CMQ from Talley Metals. We are using screw machines to manufacture it. The product gets passivated prior to installation. Once the rivet is installed it then gets staked using a mechanical press.
This product(loose by itslef without being staked) begins rusting within 8 hours in a salt spray chamber. We have similar products that are made from 302 and are not passivated that are not experiencing any corrosion after 200 hours in the same chamber. These products are manufactured by cold heading operations as opposed to screw machining. The screw machined product has a very poor surface finish with deep grooves caused by the cutting tools.
Is 302 inherently more corrosion resistant in this type of an environment than 303 or could this be caused by the poor surface finish on the screw machined part?
In the meantime I'm going to try out Carpenter Steel's project 70 type 303 and passivate it using their recomeded alkaline-acid-alkaline passivation process. I hope to achieve a better surface finish with this material. Our screw machines do not like to cut 304 or 316 so we've ruled these out as an option and we do not have enough time to produce tooling to cold head this part.
Anyone have suggestions? Any advice would be greatfully appreciated!
By the way...excellent site!
Jerry SzpakAutomotive - Cleveland, Ohio, USA
2005
Q, A, or Comment on THIS thread -or- Start a NEW Thread