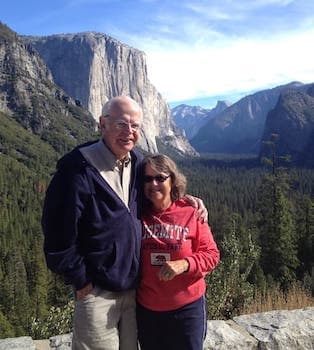
Curated with aloha by
Ted Mooney, P.E. RET
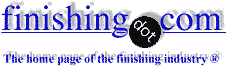
The authoritative public forum
for Metal Finishing 1989-2025
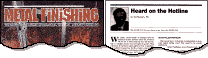
-----
Deep pitting when chrome plating crankshafts
My company is new to the crankshaft plating business, 50+ years of plating experience. We added 2 new tanks, 2 5000 amp rectifiers, and a new scrubber system about 1 year ago. We are receiving refurbished railroad locomotive crankshafts from a firm that does the grinding. The first 9 months we had little to no problems, but lately we have had a pitting problem. These pits are very deep(to base metal?) Even if shafts are reground until pits are not visible, they reappear after plating. Our tanks have been tested and seem to be fine. Plating thickness is .010 to .060. Plating temperature is between 125 degrees and 132 degrees. We are plating horizontally using conforming anodes. We have varied the plating voltage between 5 and 6 volts. Thanks for any help.
Todd Davischrome plating - Pittsburgh, Pennsylvania, U.S.A.
2005
First of two simultaneous responses
I like chrome, but 0.060 per side is grossly impractical. Under plating it with sulfamate nickel and single point machining that back to smooth and level and then a few thou of chrome would seem like a much better option.At that level, I would much rather be looking at a HVOF deposition of an appropriate alloy. Probably better, quicker, cheaper and less waste disposal.But, since you are doing chrome, with a ten power loop, look in the bottom of each pit. You will very probably see what looks like a tree stump cut off level to the ground. You formed a tree and it eventually broke off, leaving the void where there was no plate due to robbing by the tree.Initial cause is possibly from a very tiny burr left from the grinding step. It could also be from the abrasive that you cleaned the surface with. If it is always on the top of the part as it is plated, then it is shelf roughness.
James Watts- Navarre, Florida
2005
Second of two simultaneous responses
Some possibilities: excessively rough grind prior to plating. Surface not completely cleaned. Organic contamination of plating solution. Excess fume supressant. Insufficient agitation (most crankshaft platers rotate the shafts at 10-20 rpm during plating). Good luck.
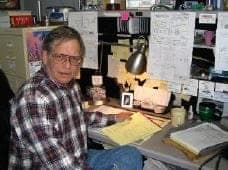
Jeffrey Holmes, CEF
Spartanburg, South Carolina
2005
This technique of crankshaft repair is commonplace, and has been used for years. The chrome thickness of .030/side is the max allowed, and is seen only occasionally. Typical deposits are between .010 and .020 per side. We are using a horizontally rotating system which should be agitating the solution. Pits do not appear to have resulted from trees because they are deep and rounded at the bottom, not spiked as if a tree broke off, and with the rotation it would be difficult for trees to form.Thanks for input so far, any more ideas.
Todd Davischrome plating - Pittsburgh, Pennsylvania, U.S.A.
2005
The best way to make sure that you will not get pits is to check the crankshafts with dye ink penetrant to see if the are not to heavy passes of the grinding.
Please let me know your views.
- Buenos Aires, Argentina
2005
2005
The problem of recurring "pinholes" in crankshaft plating has plagued the industry for many years with many suggested, but few proven, cures. First and most important, the chemical balance of your solution(s) is critical. I'm assuming you are using standard catalyst bath. Incorporating some form of purification system, such as R/O or porous pots, is essential to reduce trivalent chrome, heavy metals and other contaminants. This is very important if you are reverse current etching in the chrome tank.
Your plating process results in a very low anode-to-cathode ratio. This leads to build up of trivalent chrome and reduced current efficiency. This may account for the initial success with subsequent problems.
The hardness of the journal surface receiving the chrome impacts the quality of plating. Most railroad shafts are induction heat treated and usually present problems if not correctly ground. They are easily burned during pregrinding and should receive magnetic particle inspection prior to plating.
Every major crankshaft plater in North America has established guidelines that permit some number of pinholes, based on hole size and density. Obviously, the goal is flaw free chrome, but crankshaft plating presents many unique challenges that are difficult to overcome.
- Littleton, Colorado, USA
I am thinking of using Electroless NIckel Diamond Composite or electroforming (nickel cobalt) for tractor crankshaft repair work.
I would like to find out whether anyone has any prior experience in this matter?
- Indonesia
2007
June 5, 2008
Dear sir
I recommend you not to use any additives and only contents of your bath will be Merck 1.84 gr/lit H2SO4 and chromic acid,the temperature not vary during plating and keep it on 130 F,and current density be 1 amp/sq inch .
The distance between anode and job should not be more than 10 cm and not less than 5 cm the agitation by air should be done
- Tabriz, Azarbayjan, Iran
Q, A, or Comment on THIS thread -or- Start a NEW Thread