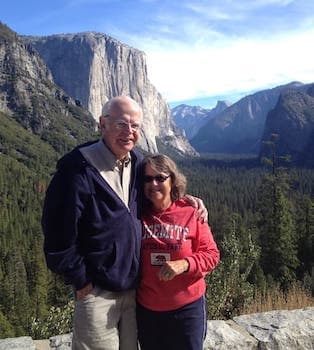
Curated with aloha by
Ted Mooney, P.E. RET
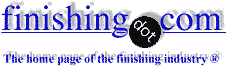
The authoritative public forum
for Metal Finishing 1989-2025
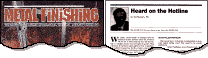
-----
Differences between chloride (acid) and alkaline zinc plating
Q. I am a Metallurgical Engineer.
I want to know - is alkaline zinc plating not recommended for high carbon, high hardness, hardened & tempered steel parts?
If not, why? What are the reasons?
- Jalgaon, Maharashtra India
September 16, 2021
September 2021
A. Hi Pawar. Alkaline zinc plating is not for those substrates for a reason which I can "sort of" explain ... but I don't claim to have a deep theoretical understanding of it :-)
Zinc is fairly close to hydrogen on the electromotive scale, i.e., there is not much difference between the voltage you need to electrodeposit zinc and the voltage which electrolyzes water into hydrogen gas and oxygen (or hydroxyl ions). And this carbon-rich substrate reduces the 'hydrogen over-voltage' to the point where an excessive amount of hydrogen will be released instead of zinc ions being reduced to zinc metal.
This causes very little & very slow plating (or no plating at all); and efforts to overcome the problem by raising the voltage only worsen the issue. Compounding the problem is the fact that high carbon hardened steels are prone to hydrogen embrittlement, and the release of so much hydrogen during the plating can embrittle it.
It is possible to do an acid zinc 'strike' and then move on to alkaline zinc for the bulk of the plating if it makes sense to do so. In the old days platers would sometimes do a cadmium plating 'strike' before cyanide zinc plating of such substrates
![]() | P.S.: This possible cadmium plating strike is one example of why we urge people not to use unknown old scrap materials for questionable uses like food service! You may think a piece to be zinc plated, even test it to be zinc plated and the surface free of toxins, then put it on a Bar-B-Q and release cadmium metal onto food. |
Luck & Regards,
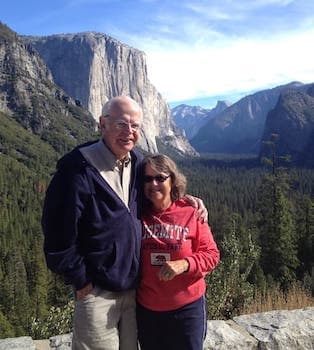
Ted Mooney, P.E. RET
Striving to live Aloha
finishing.com - Pine Beach, New Jersey
⇩ Related postings, oldest first ⇩
Q. I AM READING A SPEC THAT WILL ALLOW ALKALINE ZINC PLATING OR CHLORINE ZINC PLATING - WE ARE TRYING TO FIGURE OUT THE DIFFERENCES. PLEASE HELP IF YOU HAVE INFORMATION ON THIS.
JOHN CRAVERO- Sugarland, Texas
2005
A. First, I presume a typo and you mean "chloride" zinc (not "chlorine"). Deposits from the acidic chloride and those from alkaline baths exhibit different traits in terms of ductility, speed of deposition, ability to be post treated, etc. You need to do a little research since what you are asking for is too difficult for me to answer in this forum.
Gene Packman- Great Neck, New York
2005
A. John
Unless you mention which components are intended to be plated, a choice or suggestion is difficult.
Stay with alkaline for good distribution and excellent ductility. Slightly lower costs.
Stay with chloride zinc for good productivity and if the materials are hardened or High carbon steel.
There are more points but we need know what you are plating first.
Regards
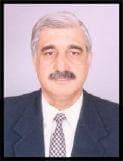
Asif Nurie [deceased]
- New Delhi, India
With deep regret we sadly advise that Asif passed away on Jan 24, 2016
2005
Q. My first question may sound very simple but I am trying to establish exactly what the difference is between Acid Zinc plating and Zinc Cyanide plating. Is there a difference in the corrosion resistance (especially in salt fog) or plating thickness range or maybe one is suited to yellow passivate and the other to clear, etc.
Secondly I have been asked to quote for a product which is to be DIN 50962 FE/ZnCo 12 //C plated. I would like to know what type of plating this and what would be the cost difference between it and more standard plating processes such as those mentioned above.
Roy Devitt- Gort, Galway, Ireland
2005
A. For practical purposes there should usually be little difference to the end user between a zinc plated part that was successfully plated in acid zinc vs. cyanide zinc. But please review the previous discussion on this thread. The shop applying the coating will make a choice of which process to implement based on a number of factors involving cost, waste treatment and disposal, required covering power, brightness, etc.
Zinc-Cobalt is an alloy plating and is a different matter. I can't quote prices since I am not a plating shop, but the alloy plating is more expensive for the shop and more difficult to run; so it will cost more, but probably not outrageously more. Wild guess 10% to 50% more depending on whether the plating shop would rather do alloy plating or would rather not :-)
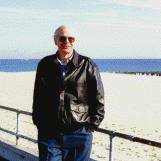
Ted Mooney, P.E.
Striving to live Aloha
finishing.com - Pine Beach, New Jersey
Q. Why and How does Alkaline Zinc Plating improve the Ductility over Acid Zinc Plating Process?
ARIJIT DAS- Jamshedpur, Jharkhand, India
April 17, 2012
A. Hi, Arijit.
It's very complicated, but the metal crystals are growing from a very different solution, and actually grow differently. Alkaline zinc crystals are smaller, and have less tensile stress.
Regards,
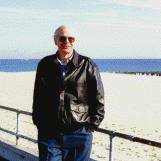
Ted Mooney, P.E.
Striving to live Aloha
finishing.com - Pine Beach, New Jersey
April 17, 2012
Q. Without using a Sealer during Plating Process, how can we increase the White and Red rust corrosion life of Zn plated components in a vehicle? What type of Air drying product should we apply on plated components having Scratch and damage marks?
Second Question is: We are getting Red Rust first on Bent portion of the Zinc Plated parts, is it because of plating film cracking? Plating Thickness is only between 8 to 13 micron.
Can we consider Trivalent Chrome passivation over Zn plating as having better corrosion resistance than Hexavalent Chrome Passivation? What is the reason behind that? Trivalent Chrome has no self-healing properties.
ARIJIT DAS- Jamshedpur, Jharkhand, India
April 20, 2012
A. Hi Arijit.
Trivalent chromate is a highly proprietary process. Some vendors' processes include a sealer, others don't. If you want to skip the sealer, you must pick a vendor who offers a system that doesn't use a sealer -- you can't just leave out a step. The plating thickness sounds reasonable, but alloy plating would offer more corrosion resistance than plain zinc plating.
Plating can crack at bends if it isn't ductile enough, but it shouldn't; an alloy plating like tin-zinc might be more ductile. You are correct that trivalent chromates are not self-healing. Trivalent chromating complies with RoHS requirements, which is vital, but it is not superior to hexavalent in corrosion resistance.
Regards,
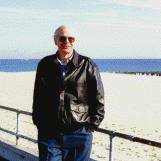
Ted Mooney, P.E.
Striving to live Aloha
finishing.com - Pine Beach, New Jersey
April 22, 2012
Q. We are plating for some parts in Rack.
we need to know which is best and what is difference between Non-cyanide and Chloride for rack plating.
Which one we can be recommended for rack plating?
Buyer - Tamilnadu, India
November 18, 2014
A. Hi Siva. We appended your inquiry to a thread on the subject which should offer you some insights. Acid zinc is brighter, but alkaline zinc offers measurably better throwing power, which can be important for rack plated work. Acid zinc holds some disadvantages for the plating shop, like being very corrosive, while alkaline zinc has its requirements and quirks as well. Alkaline zinc is probably growing in popularity while acid zinc is waning.
If it doesn't matter to you, don't specify either, so you can keep your options open. If you feel you need to specify one over the other for reliability and duplicability, make sure you have available suppliers for the process before limiting yourself.
Luck and Regards,
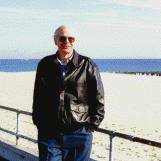
Ted Mooney, P.E.
Striving to live Aloha
finishing.com - Pine Beach, New Jersey
November 2014
A. Alkaline zinc's efficiency is approx. 50%. Acidic's zinc efficiency is close to 100%.
BUT metal distribution is much better in an alkaline plating solution.
Cast iron MUST be coated in an acidic zinc plating solution.


Sara Michaeli
Tel-Aviv-Yafo, Israel
January 18, 2015
Q. Hi all,
Can anyone suggest which plating process (acid vs. Alkaline) gives better results in welding (Spot welding of studs)?
engineered fastening - Chennai,Tamilnadu, India
April 13, 2015
A. Alkaline zinc plating is more suitable for fasteners.
Karthikeyan Ponnusamy- Bangalore, Karnataka
May 1, 2015
May 2015
Hi Karthikeyan. I am not disagreeing with you, but I ask what property of alkaline zinc plating makes it more suitable for fasteners in your mind? Especially since it seems less suitable for hardened parts and many fasteners are hardened. Thanks.
Regards,
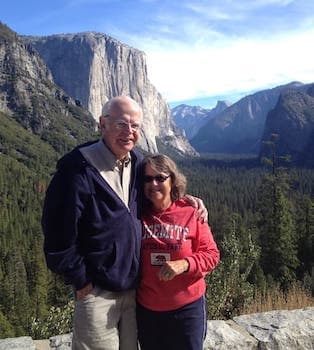
Ted Mooney, P.E. RET
Striving to live Aloha
finishing.com - Pine Beach, New Jersey
Q. There isn't much difference between acid and alkaline plating in terms of corrosion resistance as far as fasteners are considered. The shapes are simple. No such requirement of throwing power.
Acid plating gives better aesthetics and efficiency.
Pantnagar - Rudrapur, Uttarakhand, India
January 10, 2016
Q. Which process is cheaper? NC Alkaline Zinc or Acid Zinc?
Vishal Dalvi- Goa, India
January 28, 2018
A. Hi Vishal,
Usually acid zinc plating is cheaper, as it has more efficiency and lower maintenance costs. But alkaline zinc plating has improved its efficiency and costs lately, so it's difficult if you don't have the part to decide.
For fasteners, acid zinc plating is more versatile and universal. For hardened parts it's the only way to deposit zinc in less than three hours.
For sheets and large parts, alkaline zinc plating is the only way to achieve homogeneous thickness.
So, it depends on how and what you plate :)
Best regards,
TEL - N FERRARIS - Cañuelas, Buenos Aires, Argentina
February 5, 2018
Q, A, or Comment on THIS thread -or- Start a NEW Thread