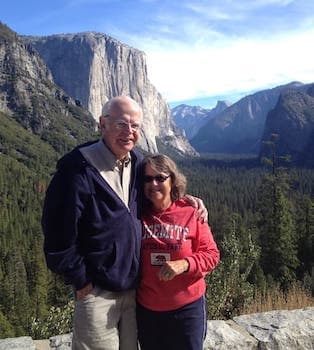
Sound technical content, curated with aloha by
Ted Mooney, P.E. RET
Pine Beach, NJ
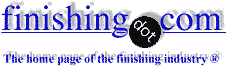
The authoritative public forum
for Metal Finishing 1989-2025
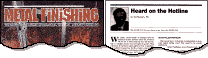
-----
How to Strip Silver Plating From Stainless Racks/Jigs
Q. Hi, I would like to know if there is a faster way to strip silver from a stainless jig than the one I presently use. At the moment I use a mix of 19:1 sulfuric/Nitric @ room Temp.
This works (slowly) but now we are finding that we have so much silver work to plate that the jigs need stripping daily (over night) otherwise the holes in the components (wide range of electrical goods) are too small to fit on the overplated hooks on the jigs. The sulfuric/nitric is not even stripping enough over night and I find myself changing of strengthening the solution weekly to keep the stripping speed up. Now even over night is not long enough. Is there another composition or temperature or even another chemical altogether that is a lot quicker to strip the silver from our stainless jigs.
Thank you for your time on this matter.
Shaun Moore- Kent, UK
2005
A. Your strip operation follows a chemical equation: 2HNO3 +2silver = H2 + 2 silver ion + 2 nitrate ion . This is a constant (K)times the nitric concentration squared times the silver concentration squared divided by the hydrogen concentration times the nitrate concentration squared times the silver ion concentration squared. Since your product is constantly growing, the reaction will slow down and eventually stop if you do not add more nitric or raise the temperature slightly. Thus, you have to periodically dump the strip.
You might try adding 1 part hydrochloric acid which will precipitate the silver as silver chloride. eventually, it will pit the stainless.
Are you up to using cyanide strip solution?
James Watts- Navarre, Florida
2005
Q. Thank-you very much for your reply. Yes I totally understand your point, We have not tried adding 1 part HCl yet, but I will give this a try. We also have the facility to add a heater to the tank, do you know of an optimum temperature or should I increase until I find a satisfactory result. We use cyanide in our silver solution so using it as a stripping chemical would not cause us any H&S problems, so this could be considered if it was a faster operation.
Thank-you once again for your time.
Shaun Moore- Kent, UK
2005
A. The sulfuric/nitric mixture is really a strip for silver off brass etc, the high sulfuric minimising attack on base metal.
For stripping off stainless steel you can just use nitric acid say 60% by Volume.This will also remove nickel and copper. It will be much faster and hold more silver in solution
I would not add chloride until the strip is exhausted when you could precipitate the silver by adding salt(sodium chloride)
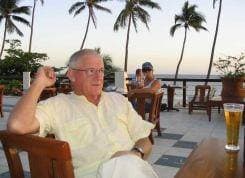
Geoffrey Whitelaw
- Port Melbourne, Australia
2005
A. Ok, for the real answer, I went to the Electroplating Engineering Handbook ⇦ this on eBay, AbeBooks, or Amazon [affil links] , fourth edition, page 234.
For stripping from stainless steel, Immersion in 95% sulfuric and 5% nitric at 80° C (175° F)- Keep covered when not in use to keep water out of it. Will absorb water out of the air and dilute it. You are going to need a good exhaust system and scrubber for this temp. Old rule of thumb, increase the temp 10C and you will double the rate of reaction.
Cyanide reverse current method is 4-8 oz of sodium cyanide, room temperature, 4-8 oz sodium hydroxide per gal and a current density of 10-20 ASF.
James Watts- Navarre, Florida
2005
Q. Well thank-you very much for all your replies. I am just going to try the 95% sulfuric and 5% nitric at 80C
Will let you know of results, thank you all very much for your time.
Shaun Moore- Kent, UK
2005
A. Even if it recommends it in the Electroplating Engineering Handbook ⇦ this on eBay, AbeBooks, or Amazon [affil links] as the "right way", I would agree agree with the method suggested by Mr. Whitelaw on this one. I have used both of these stripping methods extensively. The question was stripping silver off of stainless steel. Provided the stainless is a 300 series (or similar metallurgical make up) and the jig is not a brazed assembly, I would use a 50-60 % v/v of Nitric because of: a.) it is effective b.) it is much easier to control Can you use the 19:1 strip to strip silver off of stainless steel substrates? Absolutely. Is it the easiest way? In my humble opinion, no it is not. Lets face it, both of these acid make ups are inherently dangerous if not handled with the utmost care, but I will take a room temperature acid over the 180 degree or so make-up any day. Also, as mentioned by Mr. Watts, should you decide to use the heated 19:1 Sulfuric/Nitric be very careful about introducing water into it. If you do, you will likely end up owning some parts at some point. I'm not a chemist or a metallurgist, just a guy with 26+ years of hands on experience.
Peter Cox- North Andover, Massachusetts
2005
Q. The Jig is not a brazed Jig. We normally use 60% nitric acid at room temperature, but with a recent increase in work, the silver is now beginning to build up on the jig and hooks, added to that we are now running night shift so the amount of time we get for stripping the jigs is minimal. Also as the silver is beginning to build up on the jigs the stripping takes a lot longer than It normally would anyway, We would prefer not so heat the tank, but at the moment it is the only way I can see us getting it done quick enough...
Shaun Moore- Kent, UK
2005
A. In the long run, it might be cheaper to buy another set of jigs so that you do not have to use a heated acid strip. Safer anyway.
James Watts- Navarre, Florida
2005
A. Hi Shaun
If speed is the need then temperature is the way to go.
Dissolution in nitric is exothermic however and you need to warm to a point where the heat of reaction maintains the temperature or it can get away from you when the solution is new.
You could raise the concentration to 75% by vol of 70%w/w nitric acid but I originally suggested 60% to minimize fuming.
It will be faster at 70-80% by vol.
When the metal concentration builds up the stripping rate will slow and heat will be required to strip, say 50° C.
You may find a specialty supplier who can help with an accelerator
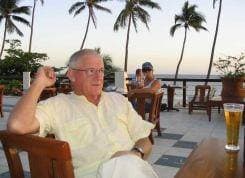
Geoffrey Whitelaw
- Port Melbourne, Australia
2005
! Thanks for the many responses on this subject. We still can not gain a satisfactory stripping solution at present, so for for the moment I have invested in some new Jigs, I have also bought a stripper from our chemical supplier which works @ 20-40 Degrees C
It requires a rectifier and works similar to an electro-cleaner and will strip @ a rate of 11 microns per minute. We are still waiting for the PVC lined mild steel tank to arrive so I cannot give any comments at present as to how well this works.
With the amount of silver we are stripping it may now be worth considering reclaiming our silver from the solution, but I will wait and see how this goes and save this for another topic.
Thanks again gentlemen for the continued support.
- Kent, UK
2005
A. You might try using Fluid bed cleaning. This will oxidise the organics and the silver will just then easily wash off. There is an outfit doing this in Birmingham.
Peter Reid- Pudsey, UK
2005
Q. We are using a sodium cyanide /caustic soda ⇦liquid caustic soda in bulk on Amazon [affil link] solution to electrolytically strip silver from scrapped parts, however the process is rather slow. How can the efficiency be increased?
Michael Attard- Zejtun, MALTA
February 6, 2012
A. That's an excellent process. Control the free cyanide at 1 to 2 oz/gallon, pH @ 10.5 to 11, current density low, > 5 ASF, and you can plate the silver out on stainless steel cathodes, peel it off, and get good value for the recovered silver, or you can use the silver plated stainless as anodes in your process and recover full value. Too slow? Let them strip during downtime, overnight/weekends.
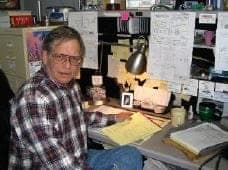
Jeffrey Holmes, CEF
Spartanburg, South Carolina
February 8, 2012
A. Jeffrey, Thanks for you advice. We need to set up this process to do 100 kgs per hour which would be equivalent to
330 sq.dm. The difficulty so far has been to strip efficiently the parts ( 20mm x 10mm x 1mm) in a barrel with an effective area of 5 sq.dm turning at 6 rev/minute.
Can we add some surfactant to improve the wetting of the electrolyte over the parts and prevent them from sticking together. What type of surfactant can we use in a sodium cyanide bath.
- Zejtun
February 18, 2012
Q. Can we use the same Sodium Cyanide/Caustic solution for silver stripping from brass components?
Puneet Malpani- Surat, Gujarat, India
February 19, 2013
Q, A, or Comment on THIS thread -or- Start a NEW Thread