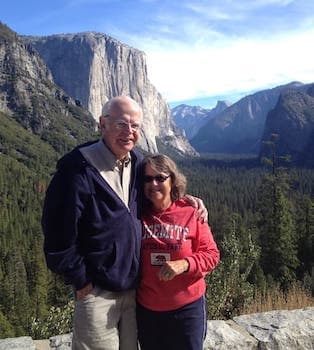
Curated with aloha by
Ted Mooney, P.E. RET
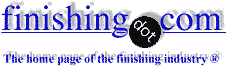
The authoritative public forum
for Metal Finishing 1989-2025
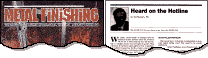
-----
Powder Coating Rusting Dispute
Q. I am involved in a dispute with a powder coating contractor. We took him some decorative metal work which we had sandblasted. He rinsed it in phosphate and then coated it with Dupont Aliphatic - Urethane Powder. He states he cured it at 400 degrees for 25 minutes. It was installed on a building outside about 50 miles from the Gulf Coast in Texas. The metal began rusting only after a few months. Does anyone have a guess as to why this may have happened and what the possible cause or causes may have been? He claims the metal had rust on it when he got it. I believe it was applied improperly. I would appreciate any information.
Doug ThomasFabricator - Victoria, Texas
2005
by Society of Manufacturing Engineers
on AbeBooks
or Amazon
(affil links)
A. Rust failure near coastal areas is usually due to moisture penetration through pinhole openings in your coating.
Is your metal structure one solid piece with minimal angular edges? Or is it possible that the powder coating did not sufficiently coat non visible areas or your steel?
(i.e mesh steel, screen steel)
Near coastal areas, one tiny (nearly invisible) pin prick hole will promote rust failure.
Jono Chae- Los Angeles, California, USA
A. Hi Doug,
This is a problem that many people have, and in my experience the coater does not usually have a leg to stand on.
There are a many reasons for this problem. When the items were sandblasted some particulates could have been embedded in to the workpiece, which would interfere with the adhesion of the powder; hence water can get in and start rusting. However this should have been eliminated at the coaters shop when the parts were washed and phosphated. The argument that it was rusting when he or she coated it, is absurd. No powder coater in his or her right mind would knowingly coat rusty metal, let alone pre-treat it. The main causes are incorrect surface preparation of the substrate, incorrect pretreatment of the substrate and incorrect application/cure/type of powder.
Jono, I think that 50 miles is far enough away from the coast for the sea breezes to have little effect. However I do agree with you that pin hole will promote rusting, but again this is the coater s problem, either using the incorrect powder, incorrect surface preparation or incorrect application. No matter how difficult the object is to coat, the person who agrees to coat it has the responsibility to prepare and coat it correctly.
Hope this helps.
Drew Devlin- Lincolnshire
2005
A. After you informed the coater of the harsh conditions that this job would be placed in, he should have steered you in the direction of a better pretreatment as a condition to accepting this job. He's in the powder coating business and should be well aware that the paint basically becomes a cosmetic addition under these circumstances, and the proper pretreatment would have given you the weatherability that you were looking for.
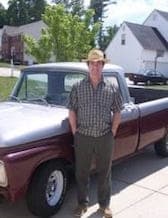
Sheldon Taylor
supply chain electronics
Wake Forest, North Carolina
2005
A. Did you give a standard and specification to the coater?, did you specify what type of phosphate it should be? (Iron or Zinc) did you specify how many stages the phosphate should have and was the final rinse demin with a low conductivity reading, did you specify how many hot salt spray hrs you expect their process should be able to pass. Why was it shot blasted? To stop steel from rusting and to ensure it remains looking good for a number of years, there are lots of factors for the coating and pretreatment to consider before even constructing the object. Unless you gave all this info to your coater I don,t think you have much to stand on. Sorry.
Anthony Wagstaff- U.K.
2005
2005
on AbeBooks
or Amazon
(affil links)
Hey Tony,
Good answer, and to some extent I agree. However I disagree with your stance on telling the coater what kind of pretreatment, how many stages, etc. It is the coater that is the expert in this field not the person who wants it coated. All this person should have to do is to tell the coater the location that the object being coated is going to be placed. Sure if you want a guarantee with the coating you should quote a specification, (All major powder coating manufacturers can provide guarantees if the process is correct and approved.). But again, if the coater accepts the job, and is told were the object is being placed, he has a responsibility to do the job correctly.
e.g. when you get your garage door re-painted do you ask the guy to take the door off and coat it to qualicoat standards? No? However you would still be unhappy if the paint started falling off after a couple of months.
Hope this helps
Drew Devlin- Lincolnshire, U.K.
A. I'm a little surprised that so much emphasis has been placed on the fabricator to specify the right coating for the job. It should be reasonable to assume that any reputable coater who is given the service conditions which the product will be exposed to would be able to recommend the proper coating. After all, they do have the resources of their suppliers that can provide them with any pretreatment, application, and post-treatment needed.
Fifty miles from the coast in Texas is plenty far enough to be away from the salt air, but the normal humidity is always an issue. I have been involved in the hot dip galvanizing industry for many years, and have done a lot of galvanizing on parts like the ones mentioned here that have been powder coated afterwards. Done correctly, it is expensive, but gives incredibly durable results. But again, the coater has to have both the knowledge and expertise to apply the right coating over galvanizing.
To think the part being blasted or surface rusted (which takes all of about an hour in typical Texas weather) gives the coater an out for a lousy job is ridiculous. It's always up to the applicator to see that surface is properly prepped for coating. Good luck! Try HDG first next time.
David JayeHouston, Texas
2005
A. I'd like to pay attention to surface profile after sandblasting? It should be at least 50 mkm so in this case just one proper 60 - 80 mkm powder layer is not enough.I think rusting of details is result of oxygen through pinholes. Two layer system could helps a lot in this case to my opinion.
reg gvido
- Riga, Latvia
2005
A. Having been on both sides - both buying and selling metal finishing, I'd like to add my two cents. Certainly the first obligation rests on the purchaser to tell, i.e. specify, clearly what he needs. He can do this by specifying such things as coating chemistry, minimum thickness, pretreatments, accelerated testing; by providing samples to be matched; by descriptions as to how the parts should look and perform.
Some purchasers may not have enough knowledge to write detailed specifications, but they can take a little time to educate themselves, and there are existing commercial and military specifications which can be used.
The purchaser should also talk to the finisher, and tell him what the service conditions are to be, and what life expectancy is desired. The finisher may well be able to help the purchaser write some sort of specification, or to direct him to an existing specification, or at least to develop a mutual understanding as to what is required.
The problem which often happens is that a purchaser sends out a request for quotation which asks for nothing more than "powder coat", and makes his purchase decision based on lowest bid. He then complains when the product does not meet his expectations, although he never told the coater what his expectations are.
To me it's a bit like going into a restaurant, asking for "steak, quote your best price", not telling the waitress how you prefer it cooked, and then complaining that you were served a well done ribeye when you had hoped for rare filet mignon.
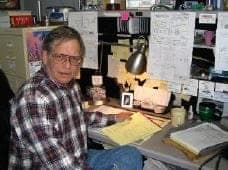
Jeffrey Holmes, CEF
Spartanburg, South Carolina
2005
2005
A. I guess there will always be a dispute about exactly how much information you should or shouldn't have to give to a supplier to get the job done the way you want it. If Mr. Thomas didn't give the coater some idea about the end use of these parts and told him "just coat it as cheap as possible", the coater wins the lawsuit because he did what he was asked to do. But if he DID warn the coater, and the coater still just painted the job rust and all, the coater loses the lawsuit(like I said before, I would have refused to paint over the rusted material). And since the steak analogy was brought up and got me all hungry, I have been in steak houses where they sit you down and the waiter(without being prompted by me) explained what each cut was and the best way to prepare it. That was the expensive steak house and they took pride in their work and reputation. The cheaper steak houses just ask "and how do you want that cooked".Period. They just figure you know what you want. Ya get whats ya pay for.
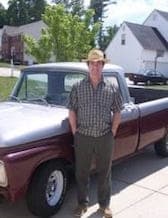
Sheldon Taylor
supply chain electronics
Wake Forest, North Carolina
A. My own experience is that a metal finisher is rarely too busy to explain things to the customer, but the customer usually doesn't want to hear it because he wants it at the lowest possible price and doesn't want to be disabused of the blinders he is deliberately wearing, and certainly doesn't want to be "upsold". But every vendor everywhere wants to upsell. Still a shop must never offer unmerchantable product regardless ... and to powder coat on material and claim it was rusty? Get outta here -- that's malpractice.
The way things are "ideally" done is the engineer or architect specifies everything based on the whole set of conditions. If the engineer or architect doesn't know enough about finishing, and can't educate himself sufficiently or in time, he retains a consultant himself who is an expert on finishing. This procedure is actually followed in aerospace and automotive for example. Boeing and GM tell the paint shop exactly what to do; the paint shop certainly doesn't tell Boeing or GM. For this reason the buyer or prime contractor may bear some responsibility.
But at the other end of the scale, homeowners don't retain architects to have replacement garage door custom finished; they simply buy one and it's supposed to be useable. To me, the question becomes whether the scale of this project was such that is was closer to a 'catalog purchase' where the item is simply supposed to work, or a 'design project' where the architect should have specified a proper finish. Always plenty of blame to spread around when things don't work, huh?
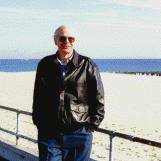
Ted Mooney, P.E.
Striving to live Aloha
finishing.com - Pine Beach, New Jersey
A. Years ago, I was involved in a similar case in which a farm implement manufacturer had very premature rusting of a product as it was introduced into the farm fields. You would not believe the blame that went around concerning who was at fault for the pinhole rust. They too sandblasted their parts prior to pretreatment. In the end, it was found that someone in their very own plant had decided to increase the size of their blasting abrasives so they could blast faster. This size change made their surface profile much different than the original product, thus the pretreatment did not get all the soils off the part before it was topcoated and after the powder went through the curing process, the soil/oil would off-gas and reveal small pinholes to the surface. It was only a matter of time before the weather took its toll.
I believe that when one brings forth a part to a paint shop, it is the paint shops obligation to notify the customer of all situations regarding pretreatment and paint performance. As Ted mentioned, many do not want to hear about this, because they feel they are being took to the bank. Some simply feel the job should be done right anyways as if all paint jobs are the same. I have always said that the best thing a shop can do for it's own quality and to prevent customer problems is to monitor and control its pretreatment system. I have been in many different paint shops and there are great differences between them. Some virtually never change pretreatment chemicals and only add chemical when it "looks" like it needs an addition. Other shops titrate every hour and keep exacting perimeters on their chemicals.
In the situation described here, communications plays a huge part between both parties. What was said, we don't really know. The truth is, proper pretreatment and high quality powder coatings will withstand many years of harsh weather. As for painting over rusted material, it happens, not especially because a company doesn't care, but because they may not see the rust without a sufficient microscope. How many times have we seen companies that shut off the conveyor lines at breaks, lunch or whatever. It only takes a few extra seconds in certain condition to start the rust process. Remember, once the parts have been cleaned of their soils, there is nothing left to prevent rust from starting. I have seen this over and over again. We can't see the rust, but the paint can.
I remember discussing this topic with Mike Cravens one time. Mike told me about how he discusses pretreatment with his customers. I couldn't believe how much time he would take to find out about his customers parts, needs, and what they were looking for in a finished product. We all need to take this same approach. If the customer doesn't understand, inform them. If they don't want to understand, take the appropriate measures to insure an adequate finished product or simply don't take the job.
![]() Bob Utech Benson, Minnesota |
![]() Ed. note: Bob is the author of: "High Performance powder Coating" on eBay or AbeBooks or Amazon [affil links] |
![]() |
A. If I get the inquiry before fabrication I always ask can it be made in aluminum? In my area you are never more than a mile or two from the seacoast and with hi UV at 25 deg N to boot. I always explain the virtues of pretreatment and the two-coat process. Most powder coating consumers have no idea of specification for salt-spray, etc., so are driven mostly by price. ![]() Larry Johnson - Key West, Florida 2005 Mr. Johnson, ![]() Sheldon Taylor supply chain electronics Wake Forest, North Carolina 2005 Larry Johnson hit the nail on the head. It was no surprise to me that he hails from a coastal town. Born and raised in Galveston, I know something about corrosion...it always prevails...it's only a matter of WHEN. For example, houses were constructed of cypress, like boats, and were intended never to be painted. Cypress doesn't like coatings and buyers of Victorian homes best bring their pocketbooks. The best paint I heard of for these has a rubber-base. But nothing works for long. - League City, Texas 2006 ![]()
Regards, ![]() Ted Mooney, P.E. Striving to live Aloha finishing.com - Pine Beach, New Jersey |
A. Based upon what I've learned through experience and discussing this topic with Mike Cravens, I can honestly say there isn't enough information in the question to answer it. There are many issues that need to be addressed before the question can be answered. From the outset the coater indicated he had blasted and phosphated the part(s). If that's true, how did parts come to have rust on them when he coated them? If he phosphated them, what chemical concentration did he use? What type of powder was used? Most importantly, how was the part constructed? Were all the pieces seal welded? For example, were the butt joints welded around the circumference? Were there areas that could not be penetrated with the powder? Were there areas that trapped water because of bad design. All of these factors play into the performance of the coatings.
After discussing this topic with Mike Cravens I now inspect all the pieces before accepting for work. Any vulnerable areas are discussed with the customer right up front. If the customer elects to proceed in light of my warning they are asked to sign a waiver of responsibility.
Additionally, the customer is advised on the type of coating that is best for the anticipated conditions.
Bottom line, there are some configurations that will corrode in short order no matter what is done . There are some configurations I simply will not do.
- San Clemente, California
2005
A. Well basically he was not well educated in this application.
He should have spent more time with the information you gave him personally if it was my self powdercoating I would have recommended galvanizing shot blast whipping to give a smoother finish and if not applicable as I don't know your application I would have powdered high zinc powder coating then to have powdercoated a good quality powder coat. I must say you only get what you paid for and if there is a fact is that you went to a coater with out this experience and you were looking at a saline environment then I'm sorry if he assured you he knew what he was doing sue him as he should have not wasted time effort and monetary finances as now it s going to cost a lot more to rectify if I was located in Texas then I would be able to inspect your property and give you a better idea of the applications you wish to apply.
- Melbourne, Victoria, Australia
2007
A. I have a coating shop in Houston. It sounds like they simply shopped price and got the service they paid for. The distance from the coast is not a factor when having your work done by a top rate shop. The reason for the problem is prep prep prep, we do a lot of work for custom home builders in Galveston. Steel shows visible flash rust in under 2 min because of the high salt. Go to a better shop and don't shop price. Shop quality. If you want good quality in any location first check out who the custom car builders or motorcycle builders use in the area. The reason is they will be more knowledgeable because of the reaction with different alloys. Not saying they are always better. For the gentleman with the problems on alum., lower your phosphate and raise your fluoride to 5ph @145 and that should solve your issues. Take care all!
Roc Taylor- Houston, Texas
March 25, 2008
A. After sandblasting the substrate, the surface would need to be blown off with 100 p.s.i. blow off gun , to insure all sand particles are removed, then a good cleaner/phosphate to insure cleaning and promote adhesion. The I would apply a zinc enriched primer to the substrate , and to make sure a corners and recessed areas are coated, next your color coat, preferably t.g.i.c. polyester.A good solid cure, making sure metal temperature reaches 380 degrees for 12 minutes.
Dean Companiopowdercoating Tampa, Florida
April 22, 2008
![]() |
August 2, 2011 "Powder Coating"... it sounded like the best thing since sliced bread. - Wooster, Ohio, USA Hi Merle. It sounds like you are talking about thermoplastic powder coatings like nylon, plastisol, or teflon rather than the typical thermoset epoxies and polyesters that most powder coaters apply; they're pretty hard to tell from paint and are generally paintable. Regards, ![]() Ted Mooney, P.E. Striving to live Aloha finishing.com - Pine Beach, New Jersey |
Re. Powder Coating. I DETEST this finish and where possible I will burn it off and get stuff galvanized. Alternatively, good quality paint works better as it does not lift and form a rust poultice. I live in Bude Cornwall UK near the Atlantic Ocean and some areas are subject to Severe Marine Corrosion. If one goes outdoors at night with a flashlight one may notice what looks like fog or mist in the beam. This is actually salt-spray that gets blown off the tops of the waves.
There is a company in Cattedown Plymouth that makes wrought iron garden furniture. It is expensive but unlike the plastic rubbish it will not blow-over in the wind. The standard finish is shot-blasting followed by hot dip galvanizing. They will only do Epoxy Powder Coating if the items are galvanized first. I think that that says it all!
Best regards from David.
- Bude, Cornwall, UK
April 19, 2017
! It seems the biggest problem with powder coating (and this thread) is that too many people claim knowledge of powder coating and the process without the one piece of information that separates the pros from ... You guys. Lol.
Every part. Every rack. Every bake. Every powder. Every day, is different. Looking for the cheapest is your first problem! Odds are you caveman that powder onto the part and believe that because it is covered it is coated! No no no! I promise that 9 out of 10 times the "problems" incurred here are due to a caveman! Lazy and grunting while throwing powder until it sticks with no adhesion or technical knowledge. When will people realize that just because you spent a summer painting houses with your pal, you're not nor will you ever be a powder coater! Poor performance is not due to phosphate zinc or iron. Lmao. It's due to a painter doing powder coating.
- Merrill Wisconsin USA!
July 9, 2017
July 2017
Thanks Cory. There is a lot of truth in there. Still, simple robotic spray guns are capable of applying robust powder coated finishes in many cases; and corrosion testing conclusively proves the importance of pretreatment (zinc phosphate).
Regards,
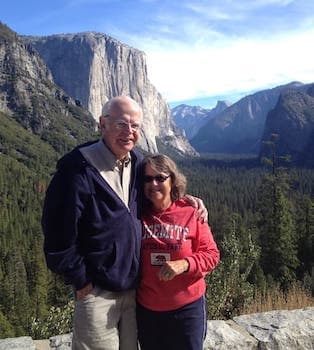
Ted Mooney, P.E. RET
Striving to live Aloha
finishing.com - Pine Beach, New Jersey
!! OK to "no off topic abstracts, babble hazards and non dialectic cultural dysfunctions". We cavemen need capital and usually act like an invasive species whether we realize we are or not. It's what we do.
I noticed two types of powder and a limited amount of metadata in regards to their properties (mentioned). But. There may be a third? What of the high temp applique? Is this "ceramic?" I had a professional do my Pan Head cylinders with what Jenn-Air Stoves applied on their dual coil element inserts. This is intensely sealed and bulletproof on my old stove as well as these cast iron engine jugs. (Forward)
I assume that this could be "high heat or marine grade epoxy" but then again there is this issue with said abstract semantics that is oh so resistant to proactive insight or comprehensive foresight! What gives in the I-P department here ... America?
I too took time to prep the begeejuhs out of some wheel hubs and frame parts and asked for a gloss black finish suitable for a show bike, only to get off the shelf* reserve poly* used for Caterpillar parts, Peoria, IL. When I assembled the hubs I used aerosol brake clean to prep the hubs and the black finish ran off like magic marker ink.
I rubbed gas on the rims with a towel and the gloss went to flat black in twenty rubs. I took the jugs to him and showed the quality I expected and got most of my money back since my parts were highly prepped, but were not hermetically sealed for the duration of a show bikes pampered existence. Now I am tooth, fan and claw to get back where I started.
The man who did the jugs was treated to the shitty corporate (dysfunctional) end of the rod, disappeared taking his skill sets with him. Hurray for "Combative Capitalism" in the economy, markets and work place. Non Combative Capitalists deserve due respect & are weeded out by the idiot factor and profit margin.
Field Engineer, Artist, Author - Henderson, Illinois, USA
August 13, 2017
A. Thanks for an informative and fun posting, Ryan.
However, the finish you are describing on Jenn-Air stoves and your "jugs" seems to be "porcelain coating" ether than powder coating. Although porcelain coating is indeed done with a 'powdered' ceramic grit, that is not what anyone else means by powder coating.
In "powder coating" an organic material like epoxy or polyester is ground up into powder, and sprayed on the parts with electrostatic attraction holding it there. The parts are then baked at temperatures generally in the 400-500 °F range to melt the powder into a continuous coating.
In "ceramic coating" a glass-like powder is heated to thousands of degrees (molten glass range) before spraying it onto the metal and forming a coating not too dissimilar to glass. It's a very robust coating, and very temperature resistant, but far more expensive than organic powder coating and done with very different equipment as well as the different coating material.
Luck & Regards,
Ted Mooney, P.E. RET
Striving to live Aloha
finishing.com - Pine Beach, New Jersey
Q, A, or Comment on THIS thread -or- Start a NEW Thread