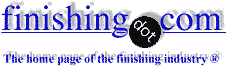
-----
Alternative to pure Ni Plating
Please provide information on the advantages and disadvantages of pure Nickel plating vs NiP plating on Base copper material with respect to semiconductors assembly.
Florante B. FenolPhilips Semiconductors - Philippines
2005
Please be a little more specific about the properties you are looking for.
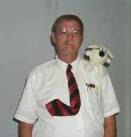
James Totter, CEF
- Tallahassee, Florida
2005
We are engaged in a semiconductor industry. We produce power transistor products for commercial and automotive application. We are introducing new supplier and different leadframe material. The leadframe coating option was either Pure Nickel or Nickel + Nickel-Phosphorous. We also use leadfree in plating and leadfinishing our product. Can you advise what leadframe coating option to use to get the best result for our device assembly and application?
Florante Fenol- Cabuyao, Philippines
2005
Why do you want to use the plating material you mention? Is it you want to switch to leadfree package? If this is the case I suggest that you use the preplated leadframe which is NiPdAu plating. This kind of leadframe don't need to undergo the plating process. Evaluation on the different kinds of packages have already done using this type of leadframe and its passed MSL2 and the solderability and wettability test.
Reliability tests in most environments require that the molding compound have good adhesion to the leadframe and the device parts it encapsulates. Two major contributors to good adhesion are the chemical affinity of the molding compound to the metal of the leadframe and the surface roughness of the leadframe. The recent general trend to avoid Pb in the electronics industry and use Pb-free solders, pushes the reflow temperature range into the neighborhood of about 260.degree. C. This higher reflow temperature range makes it more difficult to maintain the mold compound adhesion to the leadframes required to avoid device delamination during reliability testing at moisture levels. Known leadframes do not offer metallization for good adhesion combined with low cost, easy manufacturability, and avoidance of whiskers.
It has been common practice to manufacture single piece leadframes from thin (about 120 to 250 .mu.m) sheets of metal. For reasons of easy manufacturing, the commonly selected starting metals are copper, copper alloys, and iron-nickel alloys (for instance the so-called
"Alloy 42").Nickel plating of the leadframe starting metal has been shown to be desirable because nickel reduces the propensity for tin dendrite/whisker growth in devices with tin-plated leads, a generally feared failure phenomenon. Nickel, however, has poor adhesion to most molding compounds. Therefore, it is typically coated with a thin layer of palladium or gold.
There are many leadframe suppliers that offers preplated leadframe. You can choose what supplier you want based on your criteria.
Visionpak Ltd - China
2006
Ed. note: We appreciate your posting, Leo, but we need your full name and your city. Thanks.
Q, A, or Comment on THIS thread -or- Start a NEW Thread