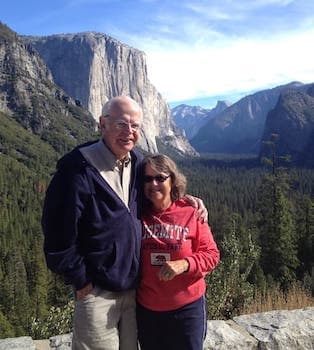
Curated with aloha by
Ted Mooney, P.E. RET
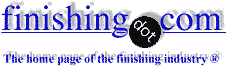
The authoritative public forum
for Metal Finishing 1989-2025
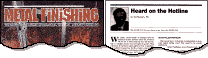
-----
EN plating thickness / Mechanical tumble media
2005
In researching Electroless Nickel plating specifically the thickness of the plating. I've found that the thicker the plating, the more brittle it becomes. I've heard that plating over .001" thick will lead to potential problems with adhesion. I've also heard the same thing for plating over .002" thick and so on. Does anyone have any information as to how thick EN can be applied before breakdown of the coating. This pertains to a High Phosphorous nickel coating per AMS2404.
Also, is there any information available on using a tumbler (not sure what media yet) to mechanically activate substrate material for plating. This would take the place of a glass bead blast. The substrate material is silicon iron, the parts are about 1" diameter by 1.75" in length with a blind hole of about 3/8".
Thanks
Jerry CalahanEngineering - CT
2005
The ductility of high phos EN does not change significantly with thickness. Adhesion is not a property of the coating, but rather of how well a part has been cleaned. If adhesion is not adequate, thicker coatings will tend to peel or blister because of their internal stress and not their ductility. The ductility of high phos coatings is only about 1 1.5% at best.
Three mil (0.003 ) EN coatings are commonly applied for equipment in oil and chemical applications. Coatings of 10 mils and more are often used to savage worn or mis-machined parts. I have personally seen one repair job in the aerospace industry where the final thickness was 125 mils.
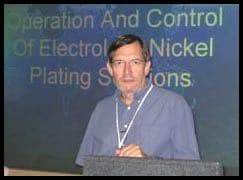
Ron Duncan [deceased]
- LaVergne, Tennessee
It is our sad duty to note Ron's passing on Dec. 15, 2006. A brief obituary opens Episode 13 of our Podcast.
Q, A, or Comment on THIS thread -or- Start a NEW Thread