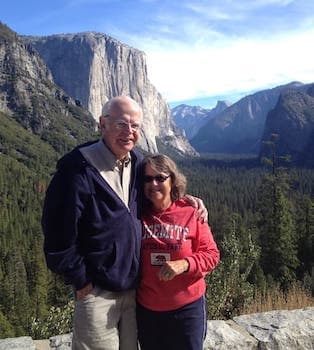
Curated with aloha by
Ted Mooney, P.E. RET
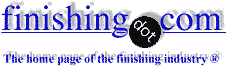
The authoritative public forum
for Metal Finishing 1989-2025
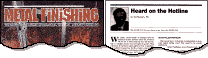
-----
How to do high gloss finish on aluminum before anodizing?

Q. Hey,
I am an OEM of a motor where certain parts of the assembly are made up of aluminium 7075 T6. I am looking for a Bright glossy Black finish on the parts but none of our vendors able to provide us the solution as per my requirement.
Kindly help us out regarding any particular process for anodizing the parts.
Environmental Conditions of the motor where the product should withstand the temp of ~ -10 to +150 °C and it will working under sun light continuously.
- Bangalore, India
December 6, 2021
A. Hi Akil. Unless there's a really, really, good reason I think you should switch to black powder coating instead of anodizing. Alloy 7075 is relatively difficult to aesthetically anodize, and type II anodizing will be marginal corrosion-wise, and even the most lightfast dyes may have trouble in this environment.
Luck & Regards,
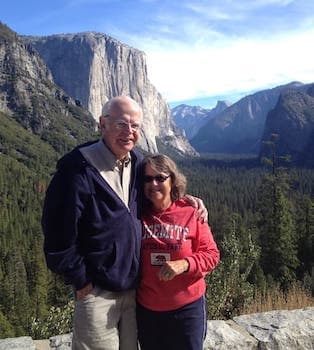
Ted Mooney, P.E. RET
Striving to live Aloha
finishing.com - Pine Beach, New Jersey
December 2021
⇩ Related postings, oldest first ⇩
Treatment &
Finishing of
Aluminium and
Its Alloys"
by Wernick, Pinner
& Sheasby
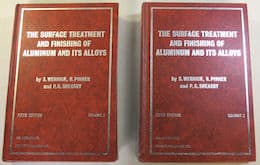
(note: this book is two volumes)
on eBay or
AbeBooks
or Amazon
(affil links)
Q. I'm trying to obtain a high gloss, polish on a prototype fly reel for fishing made from 4.5" dia 6061 bar stock before its black anodized. The machining/tooling marks are consistent and good a finish but due to handling from operation to operation there are some inconsistent markings and a dull finish. I'm looking for a tubular tumbling media that will prepare the aluminum for anodizing; I've heard that walnut shell media
⇦ this on
eBay or
Amazon [affil links]
works.
A scotch bright finish on aluminum then anodized black will leave a dull, flat looking part. I am trying to achieve a glossy black look.
I would appreciate any suggestions.
Tool and Die Maker - London, Ontario, Canada
2005
A. Have you reviewed electropolishing?
Saludos
Plating Jobshop - San Luis Potosi, Mexico
2005
Q. Will electropolishing work on aluminum die casted parts.
I am looking for a good process to chrome plate aluminum die cast parts with cooling fins. Chroming has not worked too good, so now I am looking to polish the die cast part but the cooling fins are hard to polish due to the spacings of the fins.
ENGINE ELECTRONICS - Pomona, California, USA
2005
A. Normal procedure for smooth finishes on any part is to use mass finishing equipment. Depending upon the RMS of the part it is typical to use a medium cut plastic media and either a finer plastic or a dry organic process in the same finishing equip.as a secondary step. This should get you down into the low RMS teens which is close to a lapped finsh.
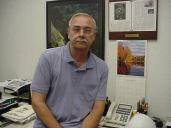
AF Kenton
retired business owner - Hatboro, Pennsylvania
2005
A. Simply buff the surface.
Bud Graybillpolishing - Anaheim, California
2005
A. THE CHEMICAL POLISHING IS RECOMMENDED USING A MIXTURE OF ACIDS (PHOSPHORIC-sulfurIC-NITRIC) WITH copper sulphate
⇦ this on
eBay or
Amazon [affil links] OR BY USING THE ELECTROPOLISHING PROCESS WHICH INCLUDES TWO WAYS
1) ALZAC PROCESS RECOMMENDED IN USA.
2) BATTELLE PROCESS RECOMMENDED IN EUROPE.
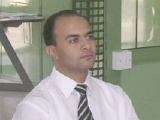
Ahmed Fouad Serag Eldin
Ein Shams - Cairo - Egypt
2005
A. Mr Renne
I've seen a machine for polishing baded disk by forcing a dough-like paste with abrasive through the part forward and backward many times to achieve the required finish .
Good luck
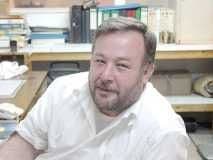
Khair Shishani
aircraft maintenance - Al Ain, UAE
2005
Multiple threads merged: please forgive chronology errors and repetition 🙂
Need to produce bright and glossy finish on aluminum
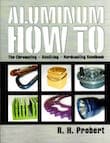
Aluminum How-To
"Chromating - Anodizing - Hardcoating"
by Robert Probert
Also available in Spanish
You'll love this book. Finishing.com has sold almost a thousand copies without a single return request :-)
Q. We are an aluminium extruder with anodizing lines. We want to produce glossy bright finish of aluminium which can withstand salt spray test for outdoor application. What is the best and most economical process to produce such finish on a mass volume scale?
Supat Ratanasirivilaialuminum extruder - Muang, Samutprakarn, Thailand
2007
A. For glossy bright; we presume you may require chemical brightening prior anodizing. This step could be considered as a part of pre-treatment. The process of chemical brightening/ bright dipping aluminium is the antithesis of etching. The purpose of this process is to "polish" the surface of the metal by smoothening the micro-roughness of the surface, not the macro-roughness. Therefore, it is always better to polish or buff the extrusion surface to eliminate any inherited extrusion problems like die lines, scratches or pits.
The result of chemical brightening is to enhance specularity and reflectivity.
A typical brightening bath consists of Phosphoric acid and Nitric acid along with other additives in small quantities that act to boost the brightening power of the bright dip bath. [There are lots of ready-mix chemicals available from chemical suppliers - you may check with your local suppliers]. The bath temperature should be maintained within a range of 85 to 110 degree C and dipping time is only few minutes depending on the bath concentration and temperature.
This could be commercially economical process but only problem is that it is not so environment friendly process. It generates significant amount of fumes. Lots of plant uses fume extraction unit with good scrubber.
Hope this answers primarily your question.
- Dubai, UAE
2007
Brushed, glossy anodizing on 70's & 80's HiFi Front Panels?
October 12, 2020Q. Hi to all,
I had bad experiences with companies when anodizing individual and prototype parts. One striking experience was meeting a representative from an anodising company who could not figure how a Nakamichi front panel I brought with me was finished. A rather coarse brushed grain but surprisingly soft to the touch and a deep glossy black.
The representative insisted was painted, even oiled until I asked him to check the surface in the lab.
It is 15 µm, of course "only" anodized.
This was times before I came to know bright dipping - and obviously this company did not have a clue about it. But this front panel could also have been from Sony, Kenwood, Denon. The finishes back in the seventies eighties were much glossier by todays standards, with deeper colors, especially blacks, the "hairlines" were coarse but soft.
Never a sign that on flake during sanding left a spot, this is what I experienced very often the last years during sampling. So how did these companies (better said their supplier) do this finish? Did they sand at all?
I have a front panel where a bead blasted area is next to a brushed one and they separate like being drawn with a ruler. Someone figured that maybe the brush lines were not sanded but milled.
It would be nice if someone could shed a light on the process back then which seem to have been lost.
Best and thanks,
Herbert
- Berlin Germany
A. Hi Herbert. Sorry that the shops couldn't identify the finish. But, yes, many shops would be unfamiliar with bright dipping as most don't offer that NOx-ious service.
Clear demarcation lines between one finish and another were probably achieved by precision masking.
While awaiting answers, please see if there is help on this thread, as well as ...
• 6326, "Problems achieving glossy anodized parts" and
• 22139, "Satin Anodized Aluminum"
Luck & Regards,
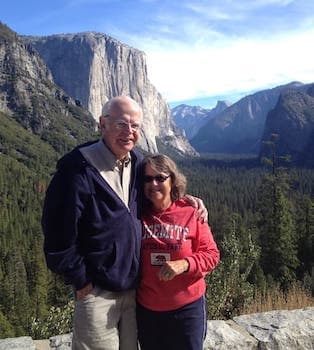
Ted Mooney, P.E. RET
Striving to live Aloha
finishing.com - Pine Beach, New Jersey
November 2020
Q, A, or Comment on THIS thread -or- Start a NEW Thread