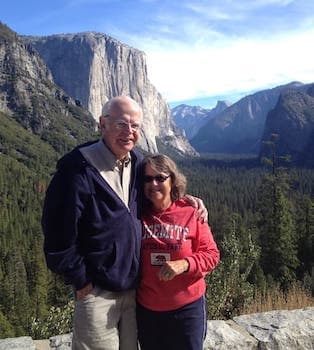
Curated with aloha by
Ted Mooney, P.E. RET
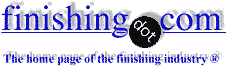
The authoritative public forum
for Metal Finishing 1989-2025
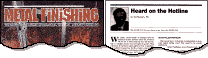
-----
Hard Chrome Plating is Peeling
Q. I am having an Industrial hard chrome peeling problem from a carbon steel pump liner in an Crude Oil service. I believe it is due to corrosion originating from the H2S or water in the crude. From the online research I conducted, it appears the best solution would be to nickel plate, then apply the chrome. As I do not have any experience in this area, I have the following questions that I hope someone may be able to answer:
1. What type of nickel plate, and how thick?
2. Are there any chrome thickness limitations? We currently use 0.015-0.020".
3. Has anyone heard of chrome corrosion problems in H2S.
Thank you !
Pumps - Warren, Massachusetts
2005
A. 1- I would go for 0.002-0.003" min. conventional watts nickel w/o brighteners, or an all-sulphate nickel. Sulfamate would be a much better option.
2- Your chrome thickness, though not impossible at all, seems high. Is it due to dimensional restoration? If it is intended for wear life increase only, it may be wise to reconsider a thiner plate with less internal stress. It would tend to wear out instead of peeling.
3- Corrosion problems will arise in most aggressive environments unless the steel substrate is protected, which cannot be done with conventional hard chrome due to the constant presence of micro cracks that sometimes penetrate the whole plate in certain areas.
Monterrey, NL, Mexico
2005
A. There should be zero sulphate in a Nickel Sulfamate Plating Solution ! If sulphate is there, then the sulfamate has broken down and you also have ammonia
⇦ this on
eBay or
Amazon [affil links] which causes brittleness.
Does your pump alloy contain lead? Is it "leaded steel"? If so, come back and let us tell you how to get adhesion on leaded steel.
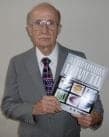
Robert H Probert
Robert H Probert Technical Services

Garner, North Carolina
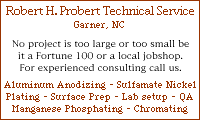
2005
by Robert K. Guffie
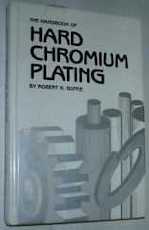
on AbeBooks
(rarely)
or eBay
(rarely)
or Amazon
(affil links)
Q. Thanks for the responses, here's some additional information:
The chrome is this thick for two reasons:
1. We are using the surface as a journal bearing, and it therefore needs to be finish ground to size and finish.
2. Our experience with "thin" platings has shown abrasive particles getting under/through the chrome and grinding it away. Thicker platings appear to better resist this.
3. We are seeing not only micro cracks, but pitting as well.
4. The base material is not a leaded steel. It's a cast carbon steel, grade WCB.
Thanks again,
pumps - Warren, Massachusetts
A. Chrome 0.015-0.020" thick is OK for conventional restoration jobs, but in this case you mention excessive abrasion and I assume by very large and hard particles (they have to be to cut through the chrome). You also mention pitting. This suggests that there might be chlorides present (you know they are the chrome nemesis). A nickel underplate might help but I think that this application is getting beyond chrome's limit. Maybe you should review other restoration techniques like HVOF or plasma spraying. These processes are capable of such thicknesses and more very easily. They can also be tailored to resist extreme corrosion and abrasion.
Guillermo MarrufoMonterrey, NL, Mexico
2005
Multiple threads merged: please forgive chronology errors and repetition 🙂
March 19, 2010
Tip: Readers want to learn from Your Situation 🙂
(little can be learned from abstract questions, so many readers skip them)
Q. What should be thickness of hard chrome for 60-66 HRc.
And what should be minimum thickness of the same in general to avoid pull-off of the same.
Thanks
- Pune, India
A. Pull-off has little to do with thickness.
Bond strength, which depends on substrate material and preparation procedure, as well as internal stress, which depends on chemistry and plating parameters are the important variables.
Hard chrome is always stressed in tension and has less than 1% ductility. So, thick layers always exhibit cracks. If care is not taken to avoid crack penetration through the plate, underneath corrosion of the substrate will destroy adhesion.
Monterrey, NL, Mexico
March 19, 2010
? Hi, cousin Dattatraya. Please tell us the details of your own situation, i.e., what is the substrate material (steel, C.I., stainless, copper), the general type of component (rotogravure cylinder, mold, etc.), the solution you are using (Sergeant, HEEF, self-regulating), and something about the issues you are experiencing rather than casting the question in the abstract. Thanks!
Regards,
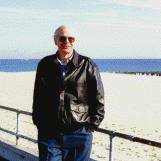
Ted Mooney, P.E.
Striving to live Aloha
finishing.com - Pine Beach, New Jersey
March 2010
Is defect from chrome plating or from casting?
February 3, 2015Q. I am Melda Helena as Supplier Quality Engineer in Indonesia. I'm fresh graduated from Chemical engineering background and I am a new employee in this manufacture. I received a defect returned from our customer "customer defect". The part is peeling, meaning the one side of chrome flake of the part is wrap.
I have taken the time to go to my supplier and sit down with them. The end goal for both of us is getting quality parts out of the door, but we need to figure out the root cause of this defect. Has anyone seen anything similar to this? And could you advise what kinds of evaluations we should take?
Are there any other evaluations?
Thank you,
:)
monitoring quality of supplier plating product - Batam, Indonesia
by Weiner & Walmsley
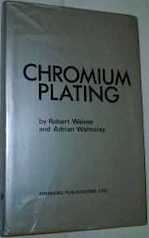
on AbeBooks
(rarely)
or eBay
(sometimes)
or Amazon
(sometimes)
(affil links)
Hi Melda. At first glance this appears to be a plating problem of the plating not adhering to the substrate, and it is generally the platers responsibility to prepare the substrate so that the plating will adhere. But is this a brand new part or has it been in service? -- because if it was in service, is it possible that the substrate is too soft and was moving underneath the plating.
Some facts you'll need to assemble as a first step include:
1 what is the substrate supposed to be, and is it in compliance?
2 what is the specification for the plating, and is it in compliance?
Then you'll face the tougher work of analyzing a lot of different things ranging from the design of the component to a detailed evaluation of the adhesion force. Many different evaluations are possible, but it has to start with whether the components are in compliance with the existing specification. If you can get back to us with what the substrate is, and the plating specification, we hopefully can help further. Good luck.
Regards,
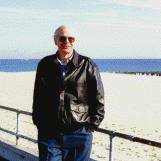
Ted Mooney, P.E.
Striving to live Aloha
finishing.com - Pine Beach, New Jersey
Q, A, or Comment on THIS thread -or- Start a NEW Thread