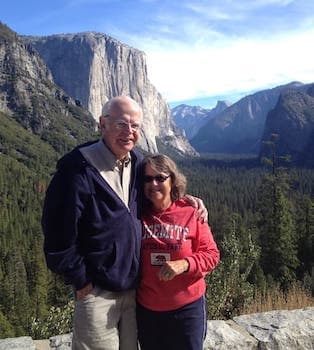
Curated with aloha by
Ted Mooney, P.E. RET
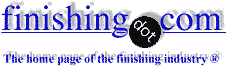
The authoritative public forum
for Metal Finishing 1989-2025
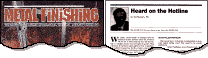
-----
Our Aluminum alloy parts are reacting after Hard Coat Anodization
2005
Help! An anodization and material handling question for aluminum alloys - - -
We sent some aluminum parts (*Aluminum alloy 7075-T6) out for hardcoat anodization per MIL. When they returned we have found that some of them have reacted - creating white spots and a different tacky finish in areas of the parts. Platers we have spoken to say that the parts must have started reacting prior to the plate operation, which only made the condition more apparent.. We have been told that it is the copper in the aluminum alloy that is reacting this way.
Has anyone else come across this condition? Is it a water or oil reaction? If so, how to avoid?
Is there a way to rework the parts -? We have considered stripping them and then doing something with the surface to make it more uniform then re-applying the hard coat.
Ryan SpauldingManufacturer - Southboro, Massachusetts
Ryan,
Aluminium alloy 7075-T6 is not a high copper alloy but a high zinc alloy (5.5% Zn, 2.5% Mg, 1.5% Cu). We have experienced problems with this material in the past and found that there was selective attack of the Zinc in the alloy. We overcame the problem by using a higher concentration of sulfuric acid (300-400 g/l) and a slightly lower temperature. This was followed by rinsing in warm (<60C) and cold water repeatedly until we had confidence that all of the acid had been removed. I can only say that this worked for us but it is always worth a try.
Reworking of hard anodised coatings is always a danger, especially on close toleranced parts. Consider that you will lose half the thickness of the coating from your original dimensions per surface and you can see that you have to be extremely careful. Is local dressing out of the soft areas and local hard anodising possible? It might be worth talking to your local brush plating/anodising supplier to see if it is.
Brian TerryWestland Helicopters Ltd - Yeovil, Somerset, UK
2005
7075 is a high Zinc alloy, not copper. The tacky feeling is normal for non-sealed hard anodize. I am not sure what you mean by white spot, if you can post a photo it would help. 7075 is a tricky material to work with, some have experienced a de-lamination or an outgassing causing the anodic coating to lift in spots. When we process this material (daily) we take certain steps to eliminate these issues. If you look around on this site you will find many postings about this alloy and issues presented.
Good luck,
Bill Grayson- San Jose, California
2005
Q, A, or Comment on THIS thread -or- Start a NEW Thread