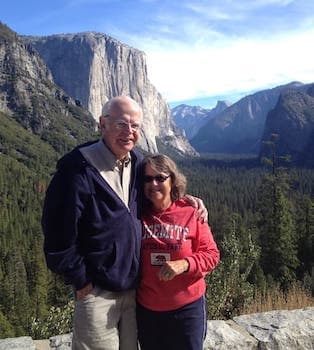
Curated with aloha by
Ted Mooney, P.E. RET
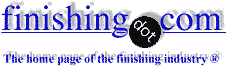
The authoritative public forum
for Metal Finishing 1989-2025
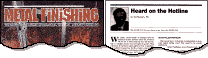
Thread 340/33
Hardness of type II vs type III anodize
What is the differance Rockwell hardness for MIL-A-8625 / MIL-PRF-8625 [⇦ this spec on DLA] Type II and Type III.
Tom Provost- Santa FE, NM, USA
2005
publicly reply to Tom Provost
Neither of these can be measured directly by the Rockwell method - the coatings are too thin for that. If they could be measured by Rockwell, they would be about Rc 70, type II, perhaps slightly less. The main difference is thickness, with type III being more than twice as thick, hence the superior wear resistance of T III.
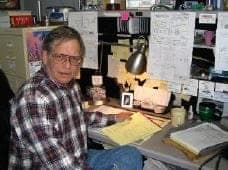
Jeffrey Holmes, CEF
Spartanburg, South Carolina
2005
publicly reply to Jeffrey Holmes, CEF
2005
You cannot measure hard aluminum oxide over soft aluminum substrate with Rockwell, it will crush through and give meaningless numbers.
Hardness on anodizing is measured on the crosssection with a Knoop diamond. Reynolds has published some hardness numbers in their MAE papers.
The Military gives no verbage to hardness, they only address thickness. "Type III" being around 0.002.
There is very little hardness difference, if any, between aluminum oxide thin as Type II versus Aluminum Oxide thick as Type III. Again "Hard Coat" really means "thick coat". It is all very hard and you cannot indent it from a perpendicular angle without crushing through to the soft substrate.
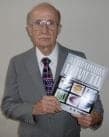
Robert H Probert
Robert H Probert Technical Services

Garner, North Carolina
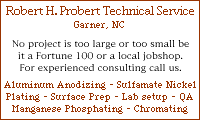
publicly reply to Robert H Probert
Actually, hardness is a misnomer. Abrasion resistance would be a more-correct term. And although type III coatings can be thicker, it is the DENSITY of the coating that offers the abrasion resistance. As far as hardness is concerned, the hardness is directly related to the material composition, such that a "harder" alloy like 7075 would be "harder" than a 6000 etc etc
Bill Grayson- San Jose, California
2005
publicly reply to Bill Grayson
Q, A, or Comment on THIS thread -or- Start a NEW Thread