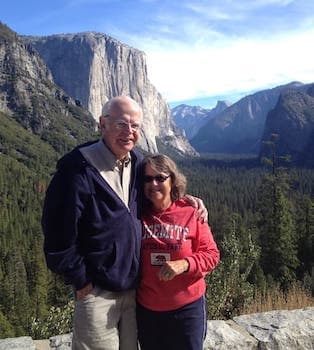
Curated with aloha by
Ted Mooney, P.E. RET
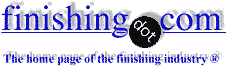
The authoritative public forum
for Metal Finishing 1989-2025
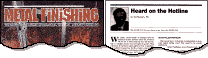
-----
Blisters on Copper Nickel Chrome (Cu-Ni-Cr) plated zamak#3 die castings
2005
We are having some problem with plating blisters on plated zinc die casting (Zamak#3). We plating it with 0.003" copper 0.003" nickel and 0.00001" chromium. but after max 1 day some blisters like bubbles appear on surface.
Our available Zamak have about %0.05 Pb (it must be less than 0.003%)and we think this is the cause of the bubbles.
How we can omit Pb from of our alloy, or is there any way in plating to decrease influence of the Pb? any ideas would be greatly appreciated
Amir Khosravipajeh - Pishavar, Aser, Pakistan
Hi there, firstly check the activation dip( powdered hf acid) after your soak cleaning , and also don't use any cathodic cleaning, secondly build good copper cyanide or alkaline base electrolytes , with a minimum current approx. 0.1 - 0.2 amp/dm sr ... hope this will help.
Regards
Praveen [last name deleted for privacy by Editor]- Mumbai, India
2005
ZINC IS A REACTIVE METAL AND ALL PRE-PLATING TREATMENTS SHOULD BE AS SHORT AS POSSIBLE.
POOR DEPOSITION OCCURS EITHER OVER CLEANED OR INSUFFICIENTLY CLEANED.
PROPERLY WASHED AFTER CLEANING IN RUNNING WATER AND THEN DIPPED IN HYDROFLUORIC ACID OR sulfurIC ACID ABOUT 5% MOMENTARILY UNTIL GAS EVOLUTION IS OBSERVED,OXIDE FILMS ARE TO BE REMOVED.
WASH AGAIN PROPERLY THEN COPPER PLATE.
CHROMIUM CONTAMINATION ALSO CAUSES BLISTERING,CHROMIUM ENTERS USUALLY BY BEING CARRIED ON PLATING RACKS.
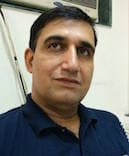
Ajay Raina
Ludhiana, Punjab, India
2005
Dear Amir,
If you do metal pretreatment as suggested by Mr Praveen and still get blisters I doubt gas entrapment during casting. Bake parts in oven at 200 °C for 2-3 hours and check , if you see some gas escaping marks (white grey dots) on surface , then you have to work out in your casting or otherwise you have to do degassing prior to plating.
Best of luck
Qutub Saify- Ajman, UAE
2005
December 30, 2009
Blisters can come from many sources, and it is sometimes very difficult to diagnose, unless you do a microscopic analysis to determine the root cause of the blisters.
Often, blisters are due to surface cold shuts on the casting surface. These are very shallow crack like defects that can seep in cleaning fluids during pretreatments. During the plating process these fluids evaporate, leaving blister like defects in the plating.
There are many other possibilities, but a thorough examination is required to accurately diagnose the defect first.
- maybrook, New York, USA

Q, A, or Comment on THIS thread -or- Start a NEW Thread