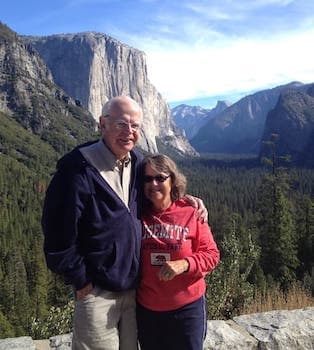
Sound technical content, curated with aloha by
Ted Mooney, P.E. RET
Pine Beach, NJ
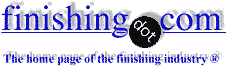
The authoritative public forum
for Metal Finishing 1989-2025
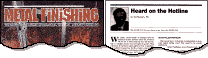
-----
Hardcoat anodizing coloration problem
We have been having a problem with hardcoat anodizing of 7075-T651 aluminum. We're specifying type III hardcoat, clear/undyed. I know the vendor has been sealing our parts but I'm not sure by which method. Our print does not specify.
The problem we're having is blotchy color. Our parts used to be greenish/gold that is common with hardcoated parts. At some point we asked the vendor to make the coating thicker, from 2 mils to 3 mils total. (We grind our parts flat after anodizing and were breaking through at 2 mils.) The color of the parts changed to light gray with the thicker coating.
Our most recent batch of parts came out gray, as usual. They were gray after grinding. At some point after we shipped the product they became mottled with the grey/gold finish in places. Rubbing them with isopropyl alcohol seems to worsen the effect. We ship our products with a plastic wrapper. Could there be some interaction? The surface appears to be sealed in both the gray and green/gold areas (marker comes off easily). The vendor looked at the parts and had no explanation. Also, he said the coating was up to 4 mils.
Cosmetics of our products are critical to us. Any ideas on what is going on and how to get consistent coloration?
Thank you.
- Minneapolis, Minnesota
1999
Dear Jon,
It sounds to me like your grinding process may be removing the seal provided by your finisher. The hot aqueous sealing process on anodized aluminum works by converting the small aluminum oxides at the surface to a much larger hydrated aluminum molecule. This
"swelling" of the surface molecules effectively closes the porosity resulting in a seal.
If you remove the surface molecules, you remove the seal leaving the porosity open to take-up contaminants. Thus the appearance of the finish will continue to change over time.
You might try one of the impregnation processes. These seal the entire depth of the pore with an organic. Loctite comes to mind.
- North Dakota
1999
Hardcoat anodize is not normally sealed, as this reduces its wear resistance. However, 7075 alloy results in a coating which is highly absorptive. It actually feels sticky as it pulls water and oils from your hands. Thicker hardcoatings increase this effect. You could be absorbing oils from your grinding and/or packaging. A good seal eliminates this problem. Thicker coatings require longer seal times. The MIL-Spec states Type III hardcoatings shall not be sealed unless specified. Your hardcoater should not be sealing without your knowledge and approval. So as to not violate the spec, he may be "drying" the parts in hot water to help with your spotting problem. This is not the same as a full sealing process.
Chris Jurey, Past-President IHAALuke Engineering & Mfg. Co. Inc.

Wadsworth, Ohio
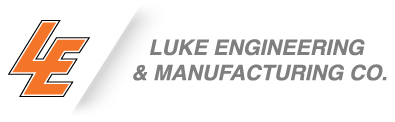
1999
I wasn't going to comment on this because Chris gave some very appropriate comments. For sure, if you are working to a normal hardcoat spec., the coating should not be sealed. I could add to his comments that in going from a 2-mil to 3-mil coating you have made the anodizer's job much harder in delivering uniform coatings. Beyond 2 mils the anodizing voltage climbs very rapidly and climbs to much higher voltages than going from 0 to 2 mils, making racking more critical, and making it more difficult to maintain the tank temperature and part temperature, hence more difficult to deliver a good hard, uniform coating and subsequent uniform color. But the major comment I wanted to make is, have you ever considered grinding your parts flat BEFORE anodize? As you have found, I'm sure, hardcoat is a very hard, very wear-resistant coating ("file-hard" is a commonly used term) and very difficult to grind down. (That is usually why aluminum is hardcoated in the first place.) Aluminum is often selected as the metal of choice because it is a soft metal and relatively easy to machine. If at all possible, at least do the majority of grinding on the bare metal. I have heard of lapping or honing hardcoat to improve the RMS finish or to get an exact thickness, but grinding through 2 mils of hardcoat must wear out a lot of grinding tools.
Phil Johnson
- Madison Heights, Michigan
1999
1999
Thank you all for your comments. I not mentioned that we grind our part flat before hardcoat anodizing and the remaining grinding is a touchup to maintain our flatness spec.
The problem isn't 100% solved yet, but we're making successful parts. The long-term plan is to use a black coloration. The marketing guys haven't yet blessed the new look. In the meantime, we determined that the blotchy grey/green or all grey parts had a much thicker hardcoat layer than we specified. The vendor is controlling thickness more carefully so we have enough thickness to grind flat without breaking through the hardcoat yet not so thick that the hardcoat transitions to the grey color.
Thanks for the help.
Minneapolis, Minnesota
Q, A, or Comment on THIS thread -or- Start a NEW Thread