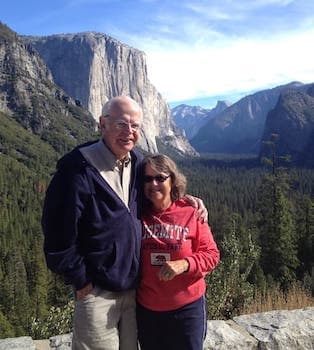
Curated with aloha by
Ted Mooney, P.E. RET
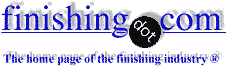
The authoritative public forum
for Metal Finishing 1989-2025
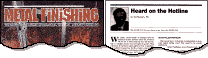
-----
Phosphating processes and hydrogen embrittlement
Q. I have a high strength steel component that may have failed by hydrogen embrittlement (indicated by an intergranular fracture mode).
The component has a black finish that I believe is from an iron phosphate process. Analysis shows high concentrations of calcium in addition to iron, phosphorus and oxygen.
Can anyone tell me what the surface coating process may be and its potential for hydrogen embrittlement. The steel is a low alloy steel heat treated to about 50 HRC, so it will not take much hydrogen to cause embrittlement. The component is not normally loaded above about 40% of the yield strength, but there is a potential to overload to near yield strength.
Thanks.
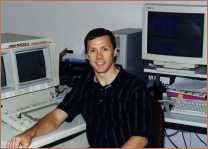
Larry Hanke
Minneapolis, Minnesota
1997
A. Get a copy of DOD-P-16232 [ed. note: replaced by MIL-DTL-16232 [from DLA] ].html" --> and read the appropriate paragraphs regarding hydrogen embrittlement. We have a couple of web sites under construction that would provide the requirements for phosphate coatings to eliminate (or dramatically reduce) the possibility of failure due to hydrogen uptake. The mil spec requires pre-stress bake and post phos-coat hydrogen embrittlement bake for all materials at or above Rc 39 (1655 MPa). Since yours if Rc 50, the possibility of failure due to embrittlement does exist. So does the possibility of thermal shock from the heat treating operation causing a microscopic crack. Were the parts fluorescent magnetic particle inspected prior to phos-coat?
Dennis JohnsonMultiple threads merged: please forgive chronology errors and repetition 🙂
Is hydrogen embrittlement a concern with Ospho finish?
Q. There is a rust surface treatment product called "Skyco Ospho" that is commonly used in automotive restoration circles, among others. I don't know the details of the composition or chemistry, but Ospho is a phosphoric acid based liquid and the label says it is "a balanced formula of phosphoric, dichromate, wetting agents and extenders". The manufacturer is listed as Skybryte Company of Cleveland, Ohio.
A typical use might be as a metal-etching primer in which the item is dipped in the room-temperature liquid, or the liquid is brushed on, is allowed to act for a short period of time (15 minutes), and then the item is wiped and/or air-blown dry.
Does anyone have any idea if use of this product on automotive steels such as fasteners, sheet metal, and springs, would create a hydrogen embrittlement problem? If there might be a problem, is there a recommended bake-out procedure that might alleviate the problem?
Thank you for your thoughts on this.
Rich Fields,coordinator- Orlando, Florida
1999
SOME UPDATES, APRIL 2015:
The 2011 MSDS for Ospho (see letter 7445, "Need Material Safety Data Sheet for Ospho") alerts us to the fact that the hazardous ingredient is 45% by volume of 75% phosphoric acid. There is no mention of 'dichromate', which would definitely be a hazardous ingredient (hexavalent chrome), so we assume that it has been reformulated in the interim if Rich's quotation was accurate.
A. Hi Rich. Any acid can contribute to hydrogen embrittlement, but phosphoric acid treatments are usually fairly gentle and this one sounds like no exception. You might check the pH of this fu-fu juice, but I doubt that it's low. But this question sounds like one that Jim Watts already knows the answer to.
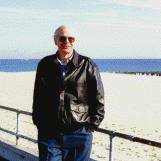
Ted Mooney, P.E.
Striving to live Aloha
finishing.com - Pine Beach, New Jersey
1999
A. Sorry Ted, all I have is opinions on this since it is not a common plating product.
The first answer is what is the metal? If it is not HARD, then a phosphoric acid based cleaner is not a problem. But, some soft metals get very hard in the weld area which is where stresses are the greatest on many parts. Therefore, positive answers cannot be given, since we do not know "the rest of the story".
I have used Ospho and always washed it off rather than letting it dry or wiping it off.
Your product is a cleaner and a poor man's phosphate coating which is similar to products that have been used by thousands of people for years with little attention to quality and thus results are varied. Most people find that it does a good job.
- Navarre, Florida
1999
Q. Thanks for the thoughts. The metal is automotive steel, and the range of types of steels covers the types in a 60s Detroit product. Carbon steels of various types from low-carbon to spring steel.
If there was a negative effect, such as in a spring steel like a hood hinge spring or front suspension coil spring, is there a suggested garage (kitchen) baking process that would drive off the hydrogen? Seems like I recall 375 °F for 2 hours as useful.
Thanks,
coordinator - Orlando, Florida
1999
A. Yes, the temperature and time you mentioned sounds appropriate for hydrogen embrittlement relief--just do it immediately after processing; don't wait a day or it will do little good. But NO processing should ever be done in a kitchen or a food oven of any sort :-(
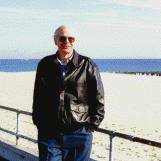
Ted Mooney, P.E.
Striving to live Aloha
finishing.com - Pine Beach, New Jersey
1999
Multiple threads merged: please forgive chronology errors and repetition 🙂
Hydrogen Embrittlement in Manganese Phosphate Finishing?
Dear Sir,
Please enlighten me on the subject matter of Manganese Phosphating of case hardened automotive gears. Does Hydrogen Embrittlement occurs while Phosphating with an accelerated type of Phosphating in which Nitrates are used as accelerators? I would like to learn from you how & what exactly are the chemical reactions taking place while Manganese Phosphating. What happens to the nascent hydrogen which is released during the process? Does this nascent hydrogen causes hydrogen embrittlement of the gear surface? Your advice will be highly appreciated. Thanks. The material of the gear components is SAE8620, En353.
Mukund Pawar- Mumbai, Maharashtra, India
2001
Q. I am interested in re-finishing a rifle with Manganese Phosphate, aka parkerizing, and was wondering if hydrogen embrittlement is of any concern with this process.
Thanks for your help,
- Santa Rosa, California, USA
2001
Q. I can't answer your question. But I would like to know where you are buying your parkerizing kit and/or supplies?
Thanks
- Redondo Beach, California
2001
A. Will -
Yes the possibility exists for hydrogen embrittlement in a parkerizing operation. Part of the equation is the hardness of the steel. The possibility grows as the hardness exceeds Rockwell 30. I would advise against a phosphate coating based on the buildup of the coating inside the barrel. Most firearms are done in black oxide, which does not promote hydrogen embrittlement and does not change the dimensions of the bore.
Hope this helps- good luck.
chemical process supplier - Gurnee, Illinois
2001
A. As a rule there will be some embrittlement, which may cause high Rockwell parts to crack under high stress loads. I've refinished several of my own guns with the manganese phosphate line at my company with great results. I baked the parts afterwards just to be safe. I wouldn't want to do it from a kit though since the process parameters are harder to control. There are quite a few professional refinishers that can do it much cheaper than a kit would cost you. The average cost for a rifle barrel is under $50 and most complete guns can be done for less than $100.
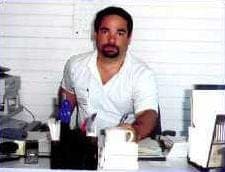
Jim Conner
Anoplex Software

Mabank, Texas USA
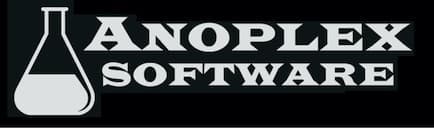
2001
What is a "stressed operation" not to be done before hydrogen embrittlement relief?
Q. Dear Sir
Phosphate coating per MIL-DTL-16232 [from
DLA]
on steel 50-60Rc.
Is grinding considered as a stressed operation which must be performed only after hydrogen embrittlement relief (120hr), or are "stress operations" due to external forces using the part only?
Thank you
Roni
product designer - Ashkelon ISRAEL
October 28, 2015
Salt spray test of baked Phosphating
Q. We have PHOSPHATED the heat treated components and kept in oven for stress releasing process for one hour to 4 hour with 150 -180 deg temperature. After that applying rust prevent oil. When we test the salt spray life for these components, we got only 12 Hrs red rust. But same components which PHOSPHATED and oiled condition we got 72 hours passed red rust (which not undergone stress release process). Whether PHOSPHATE coating is disturbed during high temp. If yes, any standard refers?
Rajarathinam SelvarajShop employee - Pondicherry, Tamil Nadu, India
July 16, 2019
A. I assume you're using zinc phosphate; the stress release process is drying out the crystals.
Ronald ZeemanCoil Coating - Brampton, Ontario, Canada
July 19, 2019
Q, A, or Comment on THIS thread -or- Start a NEW Thread