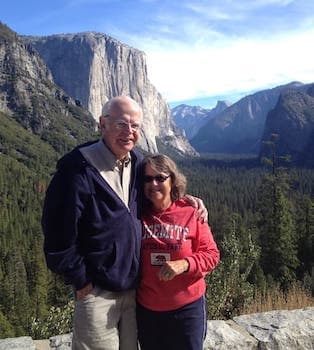
Curated with aloha by
Ted Mooney, P.E. RET
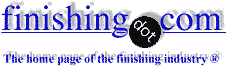
The authoritative public forum
for Metal Finishing 1989-2025
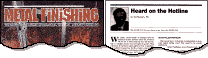
-----
Zinc Plating and Hydrogen Embrittlement
1999
I have an octagonal pin .875 in. across the flats, 17.90 inches long, and threaded at both ends.
It is made from 4140 steel hardened to Rc 40-45 and zinc plated per ASTM B633. Hydrogen embrittlement relief bake is to the minimum requirements of ASTM B633 which in my opinion is inadequate.
The pins are loaded initially in tension and see a bending load in service. I have had several pins break soon after entering service. The breaks are all near the center of the pin and all breaks originate at a corner of the octagon. The breaks appear to have stop marks indicating a progressive failure and zinc corrosion products are evident on the surface in the area of the breaks.
SEM examination of the pins points to hydrogen embrittlement and although the relief bake is certainly not adequate, the presence of corrosion raises the question of SCC or environmentally induced hydrogen embrittlement.
This pin is used in a critical application where failure can be a serious problem.
Questions:
1) Is there any way to conclusively determine if the HE is due to the plating process or if it is environmentally induced ?
2) Having determined the answer to the first question, what can be done to economically improve this design ? The catch; hardness must remain at Rc 40-45 and CAD plating is not an option.
York, Pennsylvania
Personal experience: Reduce the HE effect by having your plater reduce the time in the acid etch to the absolute minimum. Most platers over etch as an insurance that all parts, especially the rusted ones will plate. You get more HE from the etch than you do any plate cycle, including cyanide ones.
Since you want to preserve your hardness, you can not bake higher than 400F. Your present bake is probably 375F. What you can do, is insist that the parts get into the bake oven in the absolute minimum time. For high rockwell parts, I insisted on 30 min maximum! You can also bake for twice as long. This does not affect the hardness any more than the 3 hr bake does.
I am not in love with a prebake, but the book says it helps. It may make the parts harder to clean, which would require anodic electrocleaning to get it clean enough to plate.
By reducing the time in the acid (you may have to blast or tumble to clean) and baking as soon as possible (not as soon as practical) I doubt if you will see another failure.
- Navarre, Florida
1999
To determine whether hydrogen embrittlement is coming from the plating process or service environmental conditions, you would have to test sample parts from each lot for HE prior to service. If the parts can pass a test for HE, then fail in service, you probably have something other than hydrogen embrittlement due to plating.
You could test the parts full size in a simulation of the service conditions (without corrosion, of course). Or you could machine notched specimens for sustained load testing (similar to the method of Fed Spec AMSQQP416 or ASTM methods).
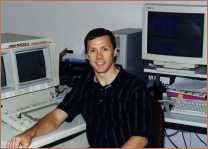
Larry Hanke
Minneapolis, Minnesota
1999
Bill, Been there - done that. Stress relieving before - during - or after plating does nothing. Consider mechanical galvanizing. Call Gord Allison at Macdermid in Waterbury Conn to explain the process.
ray delorey- cambridge, ontario, Canada
1999
Ray, you have recommended that people contact Mr. Allison about mechanical plating here many times, and it is indeed a nice process with reduced propensity for hydrogen embrittlement. But I am assuming that when you say "Stress relieving before - during - or after plating does nothing" that you mean it to be taken tongue-in-cheek because it is patently incorrect.
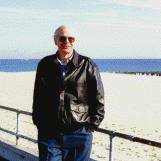
Ted Mooney, P.E.
Striving to live Aloha
finishing.com - Pine Beach, New Jersey
1999
1999
TED,
I HAVE BEEN INVOLVED WITH MANY HYDROGEN EMBRITTLEMENT STUDIES, WITH RESPECT TO ZINC PLATING
SOME OF THESE TEST HAVE INCLUDED 24 HOUR BAKE CYCLES PRIOR TO PLATING AND 24 HOURS AFTER PLATING - ALL TO NO AVAIL.
GRANTED, THE COMMENT DURING IS TONGUE AND CHEEK.
THERE IS A GROUP OF US THAT FIRMLY BELIEVE IN MECHANICAL WITH RESPECT TO THE PROCESS NOT INDUCING HYDROGEN EMBRITTLEMENT.
IN THE 15 YEARS I WORKED WITH MECHANICAL, ANY PART THAT WAS OVER A RC VALUE OF 38 TO 40 DONE IN ZINC ELECTROPLATE AND BAKED, PASSED WHEN CONVERTED TO MECHANICAL.
JUDGING BY YOUR COMMENT, I WILL BE MORE POLITICALLY CORRECT NEXT TIME
- CANADA
1999
My suggestion is: After machining,
1) 375 degree bake for 2 hrs,
2) grit blast with 230 (or better 320) grit aluminum oxide,
3) air blast to remove dust,
4) straight into zinc plating,
5) embrittlement relief.
Compare results with the problem process by splitting a lot before this procedure and running the other half in the standard process. Need about 25 parts each to get a good idea. Repeat this for at least twice to prove it is statistically significant.
- Fort Collins, Colorado
Bright plating requires higher voltages. Changing specification to Dull Plating may help. Vijay
Yashawant Devalelectroplaters - Pune, Maharashtra, India
1999
Q, A, or Comment on THIS thread -or- Start a NEW Thread