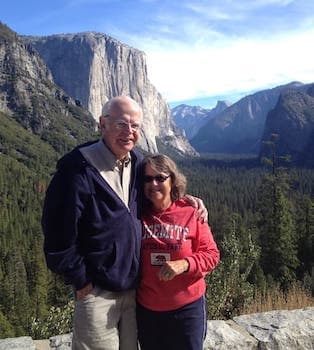
Curated with aloha by
Ted Mooney, P.E. RET
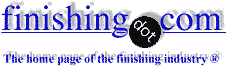
The authoritative public forum
for Metal Finishing 1989-2025
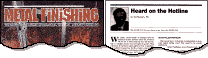
-----
Thickness/Weight of Alodine/Iridite/Chemfilm on Aluminum
Quickstart (no readers left behind):
Aluminum is often 'chromate conversion coated' as a corrosion resistant final finish or as a pretreatment for painting or powder coating. The process actually involves many steps, usually including alkaline cleaning, etching, deox/desmut, the chromate conversion step per se, and water rinses between each step.
MIL-C-5541 / MIL-DTL-5541 / MIL PRF-5541 is the most commonly cited spec. "Alodine" and "Iridite" are proprietary trade names from two suppliers of the process chemistry. "Chem film" is a slang term for the process often used in the USA.
Q. Hello all,
Our shop has been dealing with repeated salt spray failures over the last 6 months. After copious amounts of troubleshooting, we finally got all of our panels to pass, but just barely (nearly exceeded the total number of pits per 5 panels). I have been experimenting with various immersion times and checking coating weights and I am hoping someone can help me out. I know that MIL-DTL-5541F no longer specifies minimum coating weights, but what should I be aiming for, for both clear/yellow Class 1A and Class 3? I've read that 40 mg/sq ft is ideal for yellow and 12-20 mg/sq ft for clear, but that didn't specify what class. If anyone can provide any information (even if it is dated/irrelevant to the actual MIL spec) on coating weight targets, that would be greatly appreciated. We are not currently in a position to run numerous panels and salt spray all of them so I am hoping that focusing on the coating weight could be a big help. Additionally, if anyone has any other advice on passing these dang salt sprays, that would also be greatly appreciated. I have thoroughly combed through various entries on the topic and have implemented many of the suggestions (check deox, rinses, panel quality, etc) but any additional advice is always helpful. Thanks in advance to anyone who can help us out!
- Denver Colorado
December 15, 2022
A. Hi Zander.
We appended your inquiry to a thread where several readers have offered their thoughts on values for coating weights.
I'd say that since the spec used to require 40 mg/sq.ft. for Class 1A, whereas more than 40 mg/sq.ft. is problematical as several people have stated, that one is already pretty tightly defined: 40 mg/sq.ft sounds like the right target.
A couple of experts have said that less than 15 mg/sq.ft can be difficult, so why not keep the numbers simple and rounded and say 20 mg/sq.ft. for Class 3, as long as you can meet conductivity specs.
Luck & Regards,
Ted Mooney, P.E. RET
Striving to live Aloha
finishing.com - Pine Beach, New Jersey
Q. Does anybody know the optimum coating weight for chromate type conversion coating? The application is to use chromate conversion as a paint primer for aluminum. I have been told that the best coating weight is about 15 mg/ft2. Any information is very much appreciated.
S. Y. Yuen
- Hong Kong, China
1999
A. The question about coating weights is a very general question looking for a specific answer. Coating weights of chromates can vary according to the application, the alloy, and with the specific chromate you are using. We sell clear Alodines, for example, to automotive wheel manufacturers who want coating weights of 3 to 5 mg/ft2 for clear painted wheels.
Gold chromates usually run somewhat higher. 15 mg is not a bad coating weight, but one advantage of running a gold chromate is that you can see its color and can almost instantly tell whether you have a uniform coating. A range of 25-40 mg has a better gold color than 15. With accelerated chromates such as Alodine 1200S, 15 mg/ft2 might be difficult to achieve from the standpoint of requiring very short immersion times, and 40 mg would be more realistic.
It is more important to make sure the chromate is a good tight coating, never powdery or smutty. Incidentally, the trend these days is to use non-chrome treatments prior to paint. The latest generation of our non-chrome Alodines matches the performance of chromates or chrome-phosphates in most painted applications.
Phil Johnson
- Madison Heights, Michigan
-- this entry appended to this thread by editor in lieu of spawning a duplicative thread
Q. Coating thickness of Alodine 1200? We are Electroplaters in Bangalore (India) specialised in Silver Plating for Electrical and Electronic Industries. One of our customer has asked for the thickness of ALODINE 1200 chromate conversion conductive coating on Aluminium which is dipped for 4 to 5 minutes in the chromate bath.
Can you please give us the full details.
Thanking you.
MAHABHADRADAS, Director
- Bangalore, India
2000
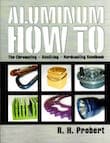
Aluminum How-To
"Chromating - Anodizing - Hardcoating"
by Robert Probert
Also available in Spanish
You'll love this book. Finishing.com has sold almost a thousand copies without a single return request :-)
A. Hi Mahabhadradas. Such coatings are conversion coatings rather than top coats. Therefore, some base metal is consumed, there may be intermediate layers of somewhat varying composition, and the surface is gel-like, and the question arises of exactly what do we mean by the thickness of the 'coating'. So people generally speak in terms of the 'weight' of the coating rather than its 'thickness'. We appended your inquiry to a thread where Phil explains typical coating weights, and there is a good deal of additional discussion of the topic on this page.
Luck & Regards,
Ted Mooney, P.E. RET
Striving to live Aloha
finishing.com - Pine Beach, New Jersey
Multiple threads merged: please forgive chronology errors and repetition 🙂
Alternate means of measuring conversion coatings
Q. Dear Sir or Ma'am, I am a quality engineer with a sheet metal manufacturing company. We have run across an issue with one of our customers regarding measuring chemical conversion coating on aluminum alloys. Their manufacturing specification is calling for the coating thickness to be between 0.00002-0.00005 inch. From the information that I have and the knowledge of the coating process which is limited to say the least I am questioning if this thickness is even possible. ASTM B449 is referring to coating mass in grams/meter square.
We have an instrument to measure paint and plating thickness (Fisher DualScope) but the ASTM spec it references to is the EDDY Current method and specifically states that chemical conversion coatings are not measurable under this standard. My questions are, is it possible to achieve a coating thickness desired by our customer spec. and can the thickness be measured without having to run test panels and weighing before and after.
Joseph M. Parker
- Smithfield, NC USA
2000
A. You are quite right; it is not possible to measure such thicknesses without very specialised equipment - electron microscope viewing prepared cross sections I think. The customer may be worried about fine tolerances (?). Chromate coating weights are measured by the strip and weigh method. If the panels are not hot air dried you can strip the coating using 30-40% nitric acid cold. Prepaint coatings are typically 0.3 - 0.8 g/sq metre (c. 30-80 mg/sq ft. R
Roger Bridger
- Croydon UK
Multiple threads merged: please forgive chronology errors and repetition 🙂
Q. What is the nominal thickness (and potential range of thicknesses) for Iridite and or Alodine type conversion coatings? Are there processing / material problems which may lead to adhesion / cohesion issues with conversion coatings?
Ralph J. LeBoeuf Jr.
aerospace mfgr - New Orleans, Louisiana
2002
by Biestek & Weber
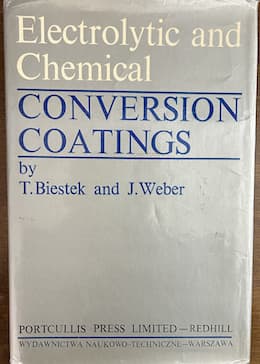
on AbeBooks
or Amazon
(affil links)
A. Since chromate conversion coatings are gels it is difficult to measure thickness directly. It is usually reported in milligrams per square foot. clear coatings will have form 12-20 mg/sq ft. Yellow chromates from 30-50 mg/sq ft. Above 40 mg/sq.ft the coatings are not as good. 40 is optimum for yellow; this equates to about .0001" or less. Generally thickness is not of interest because these coatings are too thin to have an effect on dimensions. Chromate coatings on Aluminum works well because if scratched the gel will migrate over and into the scratch and continue to protect. (168 or hrs 5% salt spray is required by most specs. They usually provide more if the solution is maintained, Impurities kept out and the finished coating is not exposed to temperatures above 150 °F for more than a few seconds. (The gel dehydrates) Chromates are excellent for promoting paint adhesion to Aluminum. Paint over chromate can be baked at the normal curing temperatures of high bake paints because the paint seals the chromate preventing dehydration. This may be more than you wanted to know.
Don Baudrand
Consultant - Poulsbo, Washington
(Don is co-author of "Plating on Plastics"
[on Amazon
or
AbeBooks
affil links]
and "Plating ABS Plastics"
[on Amazon
or eBay or
AbeBooks
affil links])
A. Ralph,
Don is for the most part correct, and as far as thickness of the Alodine, it is in fact measured in milligrams per square foot. If you would like to check the coating of any color chem treat (ex., Alodine 1200) then use three test panels so you can test the best time to use all in one shot. Run the three panels at approximately 30 seconds, 1 min and 1 1/2 minutes. Then weigh your panels and strip them in a 50% 42-baumé Nitric strip for approx. 30-60 seconds or until the panels are stripped of the coating. Then weigh the panels again, get the difference of before and after, then multiply that number by 8000 and that will give you milligrams per square foot of the coating. Now, as with any conversion coating, pre-cleaning is huge, as is temperature. Make sure that your cleaning is thorough and that your temperature is at the low end of the range, better adhesion at low temps. I have done thorough experimentation on this specific issue, if you want anymore info, post another response to this letter and I will help you out.
Have Fun Experimenting
Tony Schmaltz
- Kent, Washington
A. Tony,
That is the method I normally use, and while it works well I am looking for a method that does not have a time limit on it (the coating must be stripped within about 1 hour for full coating removal). As most small shops send the panels out for CW evaluation, there must be a method that can accurately be performed ex post facto.
Thanks!
Benjamin J. Curto
- Ponderay, Idaho, USA
Multiple threads merged: please forgive chronology errors and repetition 🙂
Weight of hex chromate
Many of our customers are asking for the "weight" of a hexavalent clear or yellow chromate. Is there a formula to calculate this?
Ed Farrer
- Lombard, Illinois, USA
2002
A. Ed,
If you are talking about an aluminum chromate coating, then yes there is a method of checking it. I really need more specifics on the product that you are using, but for an aluminum chromate coating, take test panels and run them through the bath at 3 different times, then weigh them, strip them in a 50% Nitric/Water solution and then weigh them again. Take your difference in weight and multiply it by 8000 and that will give you the coating weight in milligrams/foot squared, the units that most customers look for.
Good Luck.
Tony Schmaltz
- Kent, Washington
Q. Hi Tony,
In regards to your Alodine coating calc (by stripping/weighing difference) would you mind sharing where the "8000" figure comes from? I was looking at densities, but had assumed there was a standard test sample size (sq.ft.) I had missed somewhere.
In my case, would have a formed part with coating, that I could get the sq.ft. from CAD.
Thanks,
Dean
- New Boston, Michigan
April 27, 2023
A. Hi Dean. Tony's posting was from 20 years ago, so he may not be reachable or may not respond. But the wetted surface area of a test panel is probably about 1/8 of a square foot in area, counting both sides (10 cm long x 58 cm wetted height x 2 sides = 116 cm2 = 0.125 ft2)
So if you multiply the weight difference in g by 1000 to get it in mg, and you then multiply by 8 because the area of a test panel is only 1/8 of a ft2, you'll get the coating weight in mg/ft2.
Luck & Regards,
Ted Mooney, P.E. RET
Striving to live Aloha
finishing.com - Pine Beach, New Jersey
Thanks much Ted! Appreciate the info. Ha ha, I had not noticed the date...interesting.
Yes, makes sense, I had assumed there was a standard area in there somewhere.
Again, thanks for the quick response!
- New Boston, Michigan
April 28, 2023
Multiple threads merged: please forgive chronology errors and repetition 🙂
Q. We've recently purchased a salt spray chamber to run 168 hr tests for Alodine and 336 hr tests fur sulfuric anodize (aluminum alloys only). I'd like to bring our remaining testing in-house also, this includes the simple coating weight test. The procedure I have for coating weight is to weigh a 3x3 panel, immerse in 50 HNO3 for 1 minute, and re-weigh; Coating (in mg/sq ft) is found by the difference in weight. I know there must be a better procedure because mine is inaccurate, doesn't work on anodize, and is required to be performed 2-3 hours after processing (It's impossible for an outside laboratory to have that kind of turnaround). Does anyone have a better method?
Benjamin J. Curto
Cygnus, Inc. - Ponderay, Idaho, USA
2002
A. A method of chromate coating weight analysis that has become more popular recently is x-ray fluorescence. It provides quick results that the manufacturers claim are repeatable and accurate. It also doesn't require the use of hazardous chemicals in stripping solutions. It is doubtful that this process could be used for anodized aluminum.
Patrick Patton
Q-Panel Lab Products - Westlake, Ohio
The method you described for Alodine is very reliable.
Yours,
Moshe Yaakobv
IAI - Lod, Israel
Multiple threads merged: please forgive chronology errors and repetition 🙂
Alodine coating weight
Q. We Alodine aluminum missile parts. MIL-C-5541 differentiates a class 1A coating from a class 3 coating based on coating weight in mg/ft2. A minimum of 40 mg/ft2 is the requirement for 1A. Does this mean on your actual parts (A356 castings in this case) or on the standard 2024 T3 test coupons used to qualify the process line. Obviously the same exposure time that gives 40mg/ft2 on 2024 will yield entirely different coating weights on other alloys.
JAN SOROKA
Lockheed - DALLAS, TEXAS, US
2004
A. Hi. Although I can't answer that question, I think it has become moot :-)
Unless I'm somehow missing something, there is no longer any reference at all to coating weights in MIL-DTL-5541
[⇦ this spec on DLA] anymore :-)
Luck & Regards,
Ted Mooney, P.E. RET
Striving to live Aloha
finishing.com - Pine Beach, New Jersey
2022
Multiple threads merged: please forgive chronology errors and repetition 🙂
Q. I'm working with our Q.C. Department using a microscope to try and measure the thickness of Yellow Chromate Coating on a Aluminum bar. We've taken a part and cut it into smaller pieces to do the testing with. I've tried dipping one of the parts in Etching solution which we have in-house and it will change the color of the Zinc and the Aluminum enough where under a microscope I can get a reading but it also takes away some of the Zinc, Which gives me a false reading.
Does anyone out there know of a solution I could dip the part into and it will change the color of the Zinc to make it stand out from the Aluminum where I can get a true reading without loosing some of the Zinc Coating in the process.
I was told I could try vinegar
⇦in bulk on
eBay
or
Amazon [affil links] or Food Coloring, I've not tried these yet. Anyone got any better Ideals ?
Thanks
Eddie Knopps
- Huntsville, Alabama
2005
![]() |
A. The Military specification and the ASTM specifications show a procedure for measuring the weight gain of chromate coatings, then from that if you really desire the actual thickness you can compute. The industry does not consider thickness of chromate coatings, rather coating weight is measured. A. How thick of a coating are you expecting? Chromate coatings are generally extremely thin (typically on the order of tens of nanometers) and, unfortunately, I doubt dyes and a light microscope are capable of giving you any sort of valid data. Weight gain is a potential indicator. A quick google search found this paper on chromate coatings that you might find helpful. https://www.surtec.com/Publikationen/DeltacollE.pdf Regards, |
A. Coating weight analysis of chromium on metal substrates can be done easily on an x-ray analytical instrument conforming to ASTM D5723.
Tom Cronin
Pittsburgh, Pennsylvania
for Shops, Specifiers & Engineers
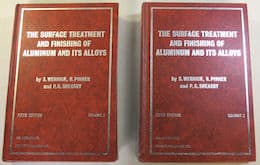
avail from eBay, AbeBooks, or Amazon
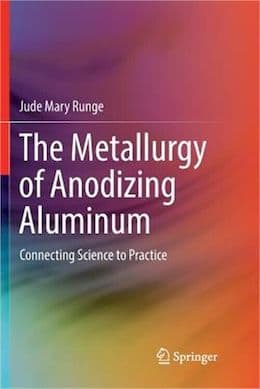
avail from eBay, AbeBooks, or Amazon
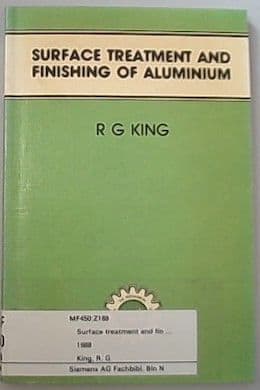
avail from eBay, AbeBooks, or Amazon
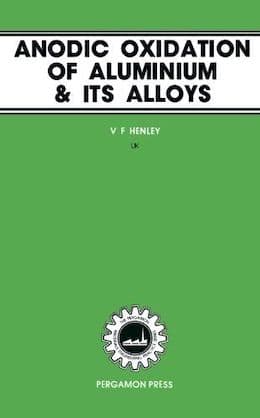
avail from eBay, AbeBooks, or Amazon
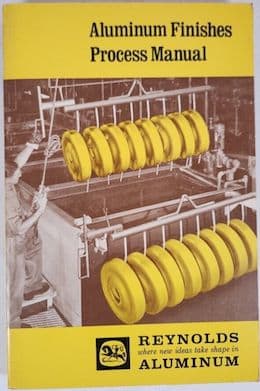
avail from eBay, AbeBooks or Amazon
(as an Amazon Associate & eBay Partner, we earn from qualifying purchases)
Q. Hi,
My name is Thomas Kelly, I am a MEng student currently working at Goodrich Engine control Systems in Birmingham, England. As part of my work placement I am undertaking a project to look at Alocrom (Hexavalent chromium conversion coating) replacements. I am looking at a range of products;
Alodine 5200
Iridite NCP
Surtec 650 (TCP)
Sanchem Safeguard 3000CC
I was wanting to know how thick these coatings are? I have had some trouble finding this information from the suppliers info and also varying reports on the thickness of the current Alocrom (Alodine 1200) coating.
Any help would be much appreciated,
Cheers
Thomas kelly
Student/Materials Engineer - Birmingham, England
2007
A. The thickness of chromate conversion coatings (hex or trivalent) will vary greatly by the parameters of the application and handling of same.
Gene Packman
- Great Neck, New York
Q. Hello all,
We are having a lot of trouble passing salt spray tests on our chem film line. I know that old 2024 panels most likely won't pass a salt spray test, but will they still plate well enough to use them to check coating weights? Any help is greatly appreciated.
Thanks,
Zander Naes
- Denver Colorado
December 2, 2022
A. Hi Zander
if you are speaking about panels that have an existing coating on them and are old, iI would not take the chance. however if you are speaking of etching the panels to remove the existing coating and performing the chem film process again then I would say go for it. There is probably nothing better for a coating than getting down to a clean new surface which the etching process would do. unless something has gone awry with your bath, you would be no worse off than where you are at currently.
I am also kind of scratching my head as to why you think that old panels would not pass salt spray. If you mean the panels themselves are old or the panels have a coating that has been applied some time ago.
Philip J. Verzal
supervisor - Cicero, Illinois
Saporito Finishing Co.
A. Thanks Phil. But, yes, many people feel that old 2024 panels will fail salt spray testing. Please see thread 30544 for one of several discussions on the subject.
Luck & Regards,
Ted Mooney, P.E. RET
Striving to live Aloha
finishing.com - Pine Beach, New Jersey
Clarification on MIL-DTL-5541F Testing
Q. Hello all,
Our shop has been dealing with repeated salt spray failures over the last 6 months. After copious amounts of troubleshooting, we finally got all of our panels to pass, but just barely (nearly exceeded the total number of pits per 5 panels).
I have been experimenting with various immersion times and checking coating weights and I am hoping someone can help me out. I know that MIL-DTL-5541
[⇦ this spec on DLA] no longer specifies minimum coating weights, but what should I be aiming for for both clear/yellow Class 1A and Class 3? I've read that 40mg/sq ft is ideal for yellow and 12-20mg/sq ft for clear, but that didn't specify what class. If anyone can provide any information (even if it is dated/irrelevant to the actual MIL spec) on coating weight targets, that would be greatly appreciated.
We are not currently in a position to run numerous panels and to salt spray test all of them so I am hoping that focusing on the coating weight could be a big help. Additionally, if anyone has any other advice on passing these dang salt sprays, that would also be greatly appreciated. I have thoroughly combed through various entries on the topic and have implemented many of the suggestions (check deox, rinses, panel quality, etc.) but any additional advice is always helpful. Thanks in advance to anyone who can help us out!
- Denver Colorado
December 15, 2022
Q. We are in Machining business High as well as HMLV [high mix / low volume]. Never done any jobs that require a surface coating of Clear Chromate Conversion MIL-DTL-5541 [⇦ this spec on DLA] Type 1 Class 1A. Print the closest tolerance is 14 Microns ( 0.014). Just curious to know what is the standard thickness tolerance achievable for this coating. My concern is that if the coating tolerance is wider than 14 Microns then our capabilities are limited and do not want to waste time processing the RFQs. Please share your thoughts. Rajeev
Rajeev VIJAYANEmployee - Bangkok -Thailand
January 4, 2023
A. Hi Rajeev
Since this is a "conversion coating", i.e., a coating which converts some of the raw material and incorporates it into the coating, along with other reasons described in the dialog, people usually discuss it by coating weight rather than thickness, but we've appended your inquiry to a thread where one reader says his requirement is 0.00002-0.00005" and another estimated the thickness of heavy coatings as less than 0.0001" (2.5µm) ... so, not even close to 14 microns. No worries.
Luck & Regards,
Ted Mooney, P.E. RET
Striving to live Aloha
finishing.com - Pine Beach, New Jersey
Q, A, or Comment on THIS thread -or- Start a NEW Thread