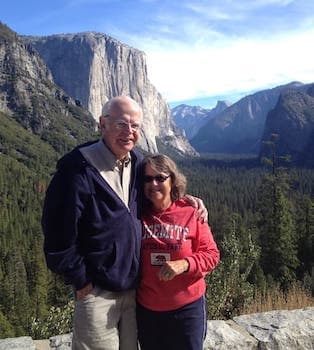
Curated with aloha by
Ted Mooney, P.E. RET
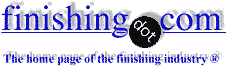
The authoritative public forum
for Metal Finishing 1989-2025
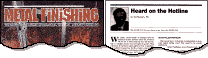
-----
Acid attack in condensing gas boilers
2005
Dear Sirs:
We're a new company established to manufacture copper heat exchangers for domestic heating gas boilers.
We're successfully launching a non condensing model and are currently preparing a condensing one with higher performance.which demand is estimated in 150.000 pieces/year.
The condensates have a water solution of nitric acid with a Ph 4'5 to 3 and the condensing temp is about 90 to 75 °C First tests have been made with a cataphoretic coating ( the ones used in automotive parts) and they resist this acid solution below the am temperatures , but as you can see in the attached picture , in the upper part -where the fumes temperature drops from 700 °c to
200 ° the paint burns out, but as there is no condensed acid , the copper is not corroded, this part is the copper color one and measures some 15 mm.
Then it comes a black zone of about 10 mm on which the temp drops from 200 to 90 °C, the paint resists the heat and there is no condensation yet
Below you see a green area which is the critical one, there condensation starts below 100 °C The acid has corroded the paint.......
Coming down- with a temp of about 80 to 70°C the acid water
-and vapour-flows flows along the fins , that keep the paint and show almost no corrosion
This picture shows a cross cut of the heat exchanger wich is similar to a car radiator, with flat tubes and willow (or zig-zag ) fins brazed to them on the edges
The sample pictured has worked non stop for 1500 hours which is a tenth of the expected life time.
Do you have any product that would help us in this project ?
We would appreciate your prompt answer and comments.
Many thanks and best regards
JM Vergara, President
gas heat exchangers - Bilbao, Bizkaia, Spain
2005
Hi Jose,
I don't know if this is of any help but when I saw the BILBAO address, this reminded me of something.
Back in the Dark Ages (the 50's or early 60's) a Company in Bilbao had problems with their turbines being hit by reasonbly high temperature and high velocity steam ...which contained droplets... which eroded said turbines. Ah yes, it was, I now remember, Babcock and Wilcox.
They solved the problem with a TS5-4 stainless mist eliminator supplied by Euroform of Aachen (now belonging to MUNTERS).
Food for thought.
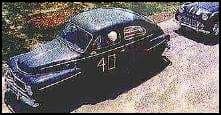
Freeman Newton [deceased]
(It is our sad duty to advise that Freeman passed away
April 21, 2012. R.I.P. old friend).
Would it be possible or even thinkable to coat the copper with aluminum or chrome, or even better, make the part out of solid aluminum? Without knowing much about the actual environment (if it has something else besides nitrates, for instance) it is very difficult to make any suggestion. Nevertheless, it is well known that aluminum and chrome are among the very few common metals that resist nitric acid. Other metals known for their good general corrosion reisitance such as nickel, copper and silver are more easily attacked by nitric.
Guillermo MarrufoMonterrey, NL, Mexico
2005
Jose,
I have my doubts with cataforetic coating. Seems to me it would be difficult to apply inside all the cavities of an heat-exchanger like that.
Ever thought about using a Nano-coating? We had to solve a similar problem once for a client, and found the solution in that type of coatings.
Good luck,
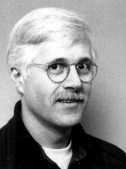
Remmelt Bosklopper
- Enschede, The Netherlands
2005
I've made some Teflon coating onto heat exchangers with problems similar to your application.
Teflon resist temperatures up to 290îC and is chemically inert.
Try it and let us know.
Suerte!
- Sant Celoni, Barcelona, SPAIN
2005
Q, A, or Comment on THIS thread -or- Start a NEW Thread