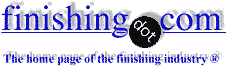
-----
Salt spray life of Paints & coatings with various pretreatments
2004
Q. Sir, please let me know the relationship between the Salt Spray Life of the system with the life of that component.
Example :
System A : Phosphate + ROZC Primer
System B : Phosphate + Epoxy Primer
System C : Zinc Plating + Epoxy Primer .
In all the three system...what is the Salt Spray Life ? How can we co-relate the life of that component in years?
Thanking you Sir,
With regards,
Umesh Singh- Lucknow, Uttar Pradesh, India
A. Hello, Umesh. This question comes up perennially but the answer remains the same. Salt spray testing is a QA test that is used to insure that a process has stayed under control, and it has no predictive value other than that.
If one of these coatings offers, for example, a 5-year real-world life and a 500-hour salt spray life, then it is reasonable to hope that as long as the parts continue to last 500 hours in salt spray testing, they will continue to last 5 years in the real world. But if the salt spray life suddenly drops to 250 hours, it does not mean a 2-1/2 year predicted life -- it means the process has fallen out of control and all bets are off.
The reason that salt spray testing has no predictive value for one type of coating vs. another is that the corrosion mechanism in accelerated testing is fundamentally different than in real life. Some examples:
- What is the effect of years of strong sunlight on ROZC (Red oxide zinc chromate) vs. Epoxy? Salt spray testing offers no clue.
- What is the effect of freezing or high temperatures on ROZC vs. Epoxy? Salt spray testing again offers no clue.
- In real life, corrosion products forming on the surface of the parts have dramatic effects. For example, hot dip galvanizing can offer a real-world life of 75 years because the zinc reacts with carbon dioxide in the air, forming a tough impervious zinc carbonate skin. This skin doesn't form in a salt spray test, so galvanizing is not impressive in salt spray tests.
Phosphate is an excellent pretreatment, but it is not equal to zinc plating as a pretreatment because zinc offers sacrificial protection. I'd probably bet on "System C" for both salt spray superiority and real life. Good luck!
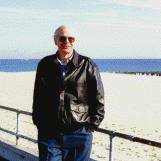
Ted Mooney, P.E.
Striving to live Aloha
finishing.com - Pine Beach, New Jersey
2005
Q. Hi,
We are changing the process of one component from C.R.C.A sheet over epoxy paint to G.I component over epoxy paint DFT of 80 microns. We decided to conduct salt spray test. Please guide us what parameter is to be checked in this test? Suggest the duration of salt spray test.
Ganapathy K.S
- pune , Maharashtra , India
October 20, 2012
A. Hi Ganapathy. You decided to change this component from CRCA to galvanized, presumably for better corrosion protection. You haven't told us the galvanizing spec, but you are asking what the appropriate salt spray duration is. I feel that this is somewhat backwards.
Ideally, the question should probably start with what kind of component it is, and what environment it will see, and therefore what is likely to be a good finishing specification. Then with the specification in hand, you process some parts, see how well they perform in service and how many salt spray hours they survive, then you periodically re-conduct the salt spray test to insure that the process hasn't deteriorated (salt spray testing is a process control, not a prediction of real life).
You can take a shortcut and ask the epoxy vendor how many hours the epoxy should survive if applied to a properly prepared substrate. It wouldn't surprise me if it were about 300 - 500 hours. You could run the test for that long, improving your pretreatment as necessary to achieve that rating. But taking a guess at what other shops get isn't really the ideal way to go. Best of luck.
Regards,
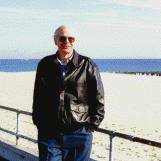
Ted Mooney, P.E.
Striving to live Aloha
finishing.com - Pine Beach, New Jersey
October 22, 2012
Q, A, or Comment on THIS thread -or- Start a NEW Thread