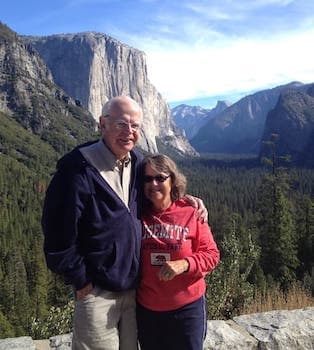
Curated with aloha by
Ted Mooney, P.E. RET
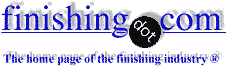
The authoritative public forum
for Metal Finishing 1989-2025
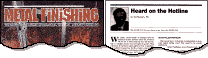
-----
SMPS rectifier for plating
In India we have been traditionally using tap-switch or auto-transformer 3 phase full wave rectifiers with claimed 5% ripple. There has always been a problem of less coverage in low current density areas, and we want to improve on this.
We have heard about SMPS (switch mode power supply) DC supplies, which are same as used in computer, but with large current. The working principal is: first the three phase mains is full wave rectified to give high voltage DC, then a high frequency chopper circuit creates pulses, which are passed through a step-down transformer to produce low voltage pulses, which are again full wave rectified to produce low voltage DC. There are large capacitors used as filters, and it is claimed that the ripple is 0.01%. These are compact units with water cooling and it is claimed to give 30% energy saving as there are no bulky transformers. Due to very high frequency the transformer size is drastically reduced, hence the copper losses (no-load losses) are very less.
I would like to know if it is a proven technology for plating, and what are the benefits or cautions.
Best regards,
Ashish VacherPlating plant - Cu, Ni, Cr, Ag, Sn, Antique Brass - Moradabad, UP, INDIA
2005
They are a proven technology, but the implication that this technology will improve coverage in LCD areas is wrong, Ashish.
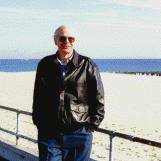
Ted Mooney, P.E.
Striving to live Aloha
finishing.com - Pine Beach, New Jersey
2005
Q, A, or Comment on THIS thread -or- Start a NEW Thread