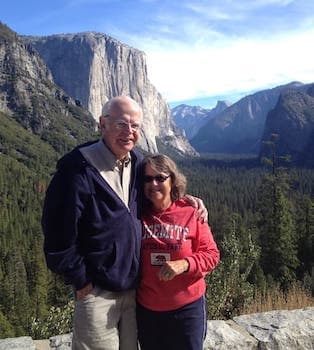
Curated with aloha by
Ted Mooney, P.E. RET
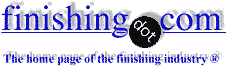
The authoritative public forum
for Metal Finishing 1989-2025
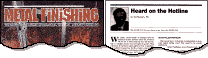
-----
Anodizing Titanium for Wear Resistance & Anti-Galling
DFL = dynamic fatigue life
SFL = single fracture load
! Regarding the anti-galling issue, we have done titanium anodize for years, but it has been using a highly alkaline recipe that was created by the chemist who worked here forever and died on the job in his 80s - a few decades ago.
There are spec requirements for putting SFL/DFL on titanium anodize - mostly for threaded applications. Both the traditional titanium anodize specs, AMS 2487 and AMS 2488, have a periodic test that tests the ability of the titanium anodize coating to bond well with the post-anodized DFL/SFL coating. It is loosely referred to as the "block on ring" test, and it uses special test "blocks" and "rings", produced only by Falex, which have been titanium anodized and then coated with the DFL/SFL. The ring is put through several thousand cycles of wear against the block, and if the DFL/SFL or anodize coating wears off before the required number of cycles, the test is a fail. I have been told that the vast majority of test attempts fail.
All that said, there is very little I have found that might help people pass that test -- which costs upwards of several thousand dollars depending on how many cycles the test goes. I can find no information on what DFL/SFL might be best suited to pass, and I have talked to the big DFL/SFL makers as well as other titanium processors. I can find no information on whether the titanium test blocks/rings should be "grit blasted" before the anodize, as that grit blast is a usual pre-treat for the application of all DFL/SFLs, etc.
I was told a month ago by Everlube's expert that they stopped doing the test because it was so hit or miss with the results. I made an inquiry to the AMS people for test clarification - because besides requiring the test, the 2487 and 2488 specs don't clear anything up - and I was simply told to raise the issue at the next committee meeting.
If anyone wants to exchange any info/experience on this - it would be greatly appreciated. Thanks!
VP, Operations and Engineering - Gardena, CA
June 22, 2022
Falex test equipment on eBay (affil link)
A. Mike,
We ran such tests with Falex back in 2013. Their results (71K) were very close to required 75k. I can forward the official Falex report upon request. The Falex rep told us that it is very unusual. Other companies cannot come so close to the required results. He encouraged us to improve the processing and submit the samples again for testing. However this testing is very expensive. I usually suggest that companies who bought this technology from us and desire to obtain 2488 certification to do testing on their own.
adv.
Concerning grit blasting - our technology does not create "fur" on the surface, but grows thick enough micropore surface to hold lubricant inside the pores. As to others' methods with "fur" growing on the anodized surface - I suspect it will be smeared away after the first ring-cube cycles.
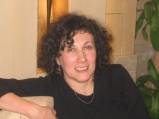
Anna Berkovich
Russamer Lab

Pittsburgh, Pennsylvania
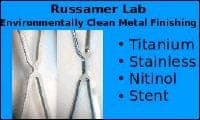
⇦ Tip: Readers want to learn from Your Situation 🙂
many readers skip abstract questions.
Q. Hi
I understand titanium anodizing will reduce the wear & galling.
Can I know if the galling still exists when both contact parts are titanium anodized?
- USA [ed. note: doubtful]
October 17, 2024
Tip: This forum was established to build camaraderie among enthusiasts through sharing tips, opinions, pics & personality.
The curator & some readers who publicly share their info will be less likely to engage with those who don't.
A. Tiffany,
As a variation of AMS 2488 or 2487, where anti-galling surface is for multiple operations, it is possible to achieve a pretty inexpensive thin anodizing layer that possesses anti-galling properties for a limited times of screwing-unscrewing, for example for medical implants.
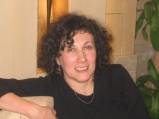
Anna Berkovich
Russamer Lab

Pittsburgh, Pennsylvania
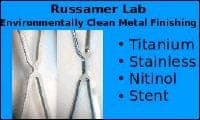
⇩ Related postings, oldest first ⇩
Q. I have a situation revolving around the galling of Ti. I understand from some research that the anodizing/oxidizing of Ti has some positive effects on wear. This seems to be an industry of well kept secrets and I have no knowledge of thickness or process effects on actual durability. It is very cute that many vibrant colors are obtained, but I am not concerned with this. I need a more functional wear layer.
Tom OathoudtSAM - El Cajon, California, USA
2004
by Zhentao Yu
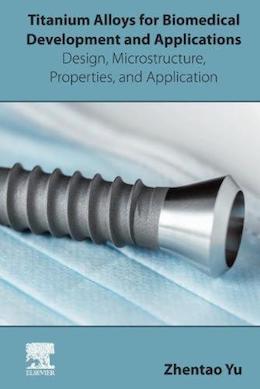
on eBay or
AbeBooks
or Amazon
(affil links)
A. There is no great secret to the protection of Titanium for anti-galling applications. Anodising of the Titanium may offer some assistance. Alkaline anodising produces a thicker coating than sulfuric acid anodising and both processes are freely available. For anti-galling I would probably look at the application of a dry film lubricant such as Molybdenum disulfide lubricants, again freely available on the open market. There has been a tendency over the last couple of years to go away from anodising Titanium as the benefits are seen to be minimal. A very simple process for the application of a dry film lubricant would be to vacu-blast the surface, ensure the surface is clear of the vacu-blast dust and then apply the lubricant.
Brian TerryWestland Helicopters Ltd - Yeovil, Somerset, UK
A. Dear Tom,
I am with titanium for 20 years. The practical way to improve its anti-galling or frictional properties is to oxidize it by thermal heating. There are some peculiarities here yet.
Andrey Igolkinprometey - St.Petersburg, Russia
A. Titanium nitride is pretty good at resisting galling, so you might look at either nitriding the surface or having a titanium nitride deposited on by physical vapor deposition (PVD). There are also several solid lubricant coatings that can be deposited by PVD, but I don't know if anyone is putting these on titanium.
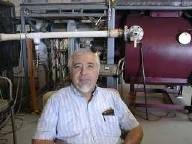
Jim Treglio - scwineryreview.com
PVD Consultant & Wine Lover
San Diego, California
Readers may also be interested in these related threads:
• Topic #3649 "AMS2488 & AMS2487 Type II Anodizing of Titanium Q&A"
Q, A, or Comment on THIS thread -or- Start a NEW Thread