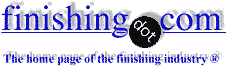
-----
citric acid Passivation on SUS430
Hi,
May I know what's the different between SUS303 & SUS430? Which is more suitable for citric acid passivation? When using citric acid passivation on SUS430, hard particle:Al/O, Si/O, Si/C & Al/O are detected. But passivate on SUS303, there is no hard particle detected. Anyone know why?
OOI HKUSM - Sungai Dua, Penang, Malaysia
2004
303 Stainless steel is a free machining form of austenitic steel, while 430 is a ferritic grade, quite different. If you look at the charts you will see that the 303 is a much "better" grade of steel, but contains 0.15% sulfur, which can cause major problems in cleaning and passivation no matter whether you use nitric or citric passivation.
Both of these grades can be readily passivated with citric acid based formulations. Both should be pretreated with alkaline cleaner (especially the 303 to remove the sulfur).
You would have to explain more about "hard particles" of AlO, SiO, SiC being present. These particles are likely from the polishing or cutting process.
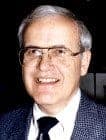

Lee Kremer
Stellar Solutions, Inc.

McHenry, Illinois
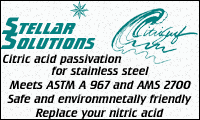
2004
Hi,
Thanks for your opinion. Sure, I would like to talk more detail about the hard particle. We used water extraction on the passivated part. After this we collected the residue from the water by filtration and the filter paper analysing by SEM/EDX. The hard particle detected are Al/O, Si/C, Si/O and Cr/O. I don't understand what is wrong with the result. As what you say, the part had gone through pretreatment by alkaline cleaner before citric acid passivation but without nitric acid. Do you think this is the key point why hard particle detected. May I know what is the function or purpose add in nitric acid before passivation? If the particle come from polishing or cutting process, why it wouldn't remove by pretreatment or passivation? Is it the two not good enough to remove it?
Thank you for your valuable opinion.
OOI HK- Sungai Dua, Penang, Malaysia
2004
2005
The only way you can get these oxide particles left on the surface is if the surface was not cleaned properly and/or the surface is fairly rough (rough by comparison to the size of the particles you are finding). The particles could be hiding in the rough surface until you do the water extraction.
430ss is not a very corrosion resistant steel, but can be hardened nicely to 60-65 Rockwell, which makes it good for many applications. The surface is not nearly as good as with the 303 after the same treatment, but it is much harder.
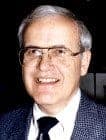

Lee Kremer
Stellar Solutions, Inc.

McHenry, Illinois
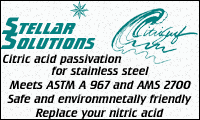
Q, A, or Comment on THIS thread -or- Start a NEW Thread