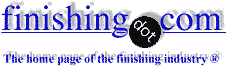
-----
Can Copper-Tin Reflow cause inadequate thickness
Q. Hi there,
We currently are faced with a dilemma regarding our Copper Tin Reflow Line.
We have plated some parts with Copper Tin and x-rayed the parts and found them to have adequate thickness per our customer's specification. After reflowing and shipping the parts to our customer, they cross-sectioned the parts and found them to have inadequate thickness. The question I have is:
Could anything happen during the reflow process which would cause the copper thickness to decrease. Please advise and provide any applicable reading material in this regard.
Thank you very much for your help in advance.
Best regards,
Fouad Sqalliseals - Murray Hill, New Jersey, USA
2004
A. By X-ray, I suspect you mean you have done EDAX. This will show tin of a certain thickness, but since you have reflowed it, some of the tin will have migrated into the copper to form an intermetallic compound and the lower levels of your tin layer will certainly be associated with copper. The amount of free tin on the surface will have been reduced.
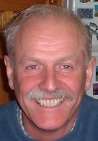
Trevor Crichton
R&D practical scientist
Chesham, Bucks, UK
Q. Thanks for your response. The problem actually we are having is the reading on the copper rather than on the tin.
Please advise of any further information on this.
Thanks,
Fouad Sqalliseals - Murray Hill, New Jersey, USA
A. We had similar problems as this: correct specification for the tin and after reflow it was under specification. After some experimentation it was found to be the reactivation of the item that was removing some of the tin. To solve this we cut down reactivation times and only reactivated the item once. I also found that items should be reflowed as soon as possible after reactivation. Also if the tin is too thick or over spec this also allows the tin to run off and de-wetting or blisters occurs. We also found the time used to reflow had to be reduced -- less time is better; also the temperature we found best was 250 °C.
You will always have problems reading the copper after any reflow and will be given false readings, the copper should be checked before reflow as the reflow process does not alter the copper spec.
Christopher Page- Saffron Walden, Essex, UK
July 9, 2012
? What is the step-by-step for tin fuse (reflow) after tin plating. Thank you.
john dennyemployee - Anaheim California
March 7, 2023
Ed. note: Folks, please introduce yourself and describe the situation facing you. Sorry John, we're not sure if you're asking Fouad for further detail about his sequence so you can better help him, or whether you're asking a new question and want to be referred to books/papers about reflowing. Sorry.
Q, A, or Comment on THIS thread -or- Start a NEW Thread