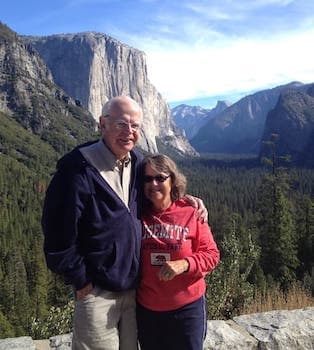
Curated with aloha by
Ted Mooney, P.E. RET
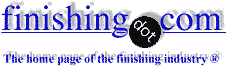
The authoritative public forum
for Metal Finishing 1989-2025
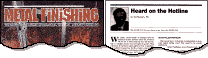
-----
Etching Problems with Manganese Phosphate Coatings
Q. We routinely manganese phosphate our products at various coating companies here in the Houston area, using both the Aerocote and Keykote products. Our parts are typically 4130, 4140, or A707 steel. They are also typically quite large (100-300 lbs each). We've had parts blast cleaned and chemically cleaned.
From time to time, we have very serious problems with etching of parts. When this happens the parts are scrapped because the tight tolerances and surface finishes are destroyed. We have had to throw away more than $250K of parts just in the past 2 years due to these problems. We've had this etching problem with all alloys, surface cleaning methods, chemical manufacturers, and coating vendors...it's pervasive.
We cannot get straight answers from either our coating vendors or the chemical companies as to why this occurs or under what conditions it can occur. We suspect that it is mostly due to either the part surface or phosphate bath temperatures being too low when the part is first put into the tank. But we've heard as many excuses and reasons as you can imagine.
Is acid etching in the manganese phosphate process typically strictly a problem with temperature, or are there other issues that can cause this? Is etching more or less a problem with zinc phosphating (compared to manganese)?
Any help would be appreciated. Thanks.
Ed Galle, Jr.- Houston, Texas
2004
Q. I am interested in knowing the answer.
Murtaza Choudhry- Pakistan
2004
![]() |
A. You must adjust the free acid immediately prior to processing the 4000's. Bring the buret to the tank side, start heating, when you get to 185 °F, then titrate for free acid and knock it down to a ratio like T/F=6/1. Continue heating to only 195 °F. Then you must use a grain refiner with the 4000's. ![]() Robert H Probert Robert H Probert Technical Services ![]() Garner, North Carolina ![]() 2004 A. Your problem is most likely not heat related. Chemical etching is accelerated by temperature, of course, but the processes you're running would have to be wildly out of spec for temperature to have much effect. There are several possibilities, time in the bath, pH, free acid, and the exact acids in use are all things that will affect the amount of etch. You need a regimented testing process that will pinpoint the part of the process causing the problems. Start by making sure the chemical baths are in spec, then be sure times and temp instructions are followed. Measure the results and log all variation. Then make changes one at a time and log the differences in the results. This will give you an idea of what parameters really make a difference in your process. ![]() Jeff Watson - Pearland, Texas 2004 |
A. Years ago I seem to recall Pre-Heating large components prior to a Manganese phosphate, (immersed in Very hot Water) as the temp. drop at the metal/solution interface, could cause problems. Iron concentrations are of course to be titrated for.
ALAN THOMASEarly Retiree - Chandler, Arizona, USA
2005
A. The problem with addressing your problem is the lack of knowing your process first hand. The things that affect these types of coatings are surface finish as an outside problem. The internal problems can be time in bath, concentration, and heat. Most times, these process controls are automated and don't pick out certain parts to be bad. With the type of steel and the type of phosphate, I am inclined to say we have a different issue. All incoming surface conditions should be able to be handled in a robust phosphate process. I believe there is a flow of fluid problem within the Phosphate bath. The type of steel you are processing require a quick zinc seal. The flow must be strategically set to all parts in the bath. Parts with low flow will pit and parts with too much flow will smut.
Gil Walker- Summerville, South Carolina
2006
Ed. note --
Readers: This forum is for camaraderie, education, non-commercial technical info, and fun. We decline to print postings which direct the reader to buy product X, retain consultant Y, or privately contact person Z.
July 6, 2015
Q. Hi
We are processing different kinds of alloys in Mn Phosphating, and I am facing a peculiar problems, some components are getting etched, and the etching lines are so much visible and Ra value of the component get changed, because of this some parts are rejected,
Can someone tell me what exactly the reason for this, is the Free acid culprit?
metal coatings - Dubai, UAE
A. We have dealt with this issue before and the best solution was a hot bath. We have found with higher alloys and mass that the bath would be "shocked", lose heat and not be able to recover quick enough to beat the etching. Preheating helps, but the tank design must allow for a quick response to the temperature drop. Our rule of thumb was to have the bath temperature of at least 208 °F with F/T acid ratio around 9. The same parts that etched before would have a 4 min cycle time.
Lane
- New ulm, Texas
May 28, 2016
Q, A, or Comment on THIS thread -or- Start a NEW Thread