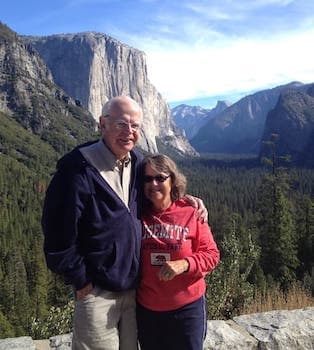
Curated with aloha by
Ted Mooney, P.E. RET
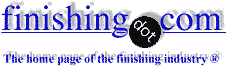
The authoritative public forum
for Metal Finishing 1989-2025
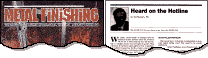
-----
Anodizing Hardness vs. temperature, current, and other parameters
2004
Q. My name is HC Lee and I am working as an QA Executive in a anodizing services company.
I urgently seek consultancies on the problem of the anodizing material hardness.
Specification require = hardness 400 Hv minimum
Operating temp = 13 °C voltage = 23V time = 20 minutes sulfuric acid = 200 g/l Al content = 5 g/l Sealing = 15 min/98 °C
Any of the above factors that contribute most to the failure of the hardness? It seems hardness went down from 430 to 375 hv by using the same operating parameters. Can any one advise me?
Thanks
Hwa Chang LeeAnodizing Industry - Kuala Lumpur, Malaysia
![]() |
A. Suspect one is that your agitation , air and / or liquid, has dropped. Two is the temperature control throughout the run is not consistent-possibly larger loads. Three is your temperature control has lost calibration. Four is your power supply has lost its calibration. five, someone changed some parameter of the tanks chemistry or times. Finally, your anodize tank has too much copper or aluminum in it. James Watts- Navarre, Florida 2004 A. If you used the exact same operating parameters, and the same aluminum, the hardness would not change, so you will have to look at your operating parameters and see which have changed. Let's take temperature for example. You say 13C, but there must be some operating range, an upper and lower control limit. If you were to anodize today at, say,11C and tomorrow at, say 15 C, the work you do tomorrow would likely be softer. Find out exactly what your parameters were when you did good work, duplicate them, and you'll do good work again. ![]() Jeffrey Holmes, CEF Spartanburg, South Carolina 2004 |
A. Sounds like you are trying to coat type 3, should coat @ 30 amps per sq/ft not by volts.
Chris Snyderplater - Charlotte, North Carolina
2004
![]() |
"The Surface
Treatment & Finishing of Aluminium and Its Alloys" by Wernick, Pinner & Sheasby ![]() (note: this book is two volumes) on eBay or AbeBooks or Amazon (affil links) A. Amen to what Chris said. - Columbia, Maryland, USA Ed. note: it is our sad duty to advise of the passing of Paul Yursis in August 2005. A. Drop the sulfuric acid from 200 g/L to 165.3 g/L and the pore gets smaller and the surface gets harder. ![]() Robert H Probert Robert H Probert Technical Services ![]() Garner, North Carolina ![]() 2004 |
November 12, 2012
Q. I am a new supervisor in an automotive industry>
We have a new project involving "hardcoat anodising on aluminum alloy"
Our customer requests the specification as
1. max roughness 2,4 Rz
2. minimum hardness 310 Hv (microvickers)
3. minimum thickness 4 microns
We conduct the trial with
1. Anodizing material Al alloy AC2B
2. 20% W/W sulfuric acid
3. Temperature 5 °C
4. 21 V with Constant Voltage
We can get a fine result for Roughness and thickness, but when we test the hardness, it failed.
Sometime we can get at about 300-310 Hv.
But most likely the average hardness is 190-270 Hv.
For your information, we conduct anodizing in 2,5 hour and the thickness is 10-15 micron and we use cold resin to make sample moulding.
Please anyone can give us some advice to increase the Hardness?
thank you very much for your help
anodising line supervisor - Jakarta, Indonesia
![]() |
November 14, 2012 A. Hi, ![]() Harry Parkes - Birmingham, UK A. "Normal" hardcoating parameters are 0 °C with constant current density of 3.5 to 4.0 A/dm2. The final voltage should be higher than 21 VDC. I would expect to achieve 10-15µm in about 20-30 minutes with a terminal voltage of 30-40 VDC. Chris Jurey, Past-President IHAALuke Engineering & Mfg. Co. Inc. ![]() Wadsworth, Ohio ![]() November 15, 2012 |
Temperature, Hardness and Coat
September 19, 2016Q. Specifically I would like to know how to set the parameter between coat and hardness according to several specifications (COAT: 10 to 30 µm Hardness: 330 to 430HV).
I have some idea that the temperature is totally involved in the process as more hot less hardness and more cold more hardness, is it correct?
We can consider a table of parameter for this?
- Leon, Guanajuato, Mexico
Q, A, or Comment on THIS thread -or- Start a NEW Thread